Countering unpredictable future threats demands MOSA
StoryFebruary 13, 2024
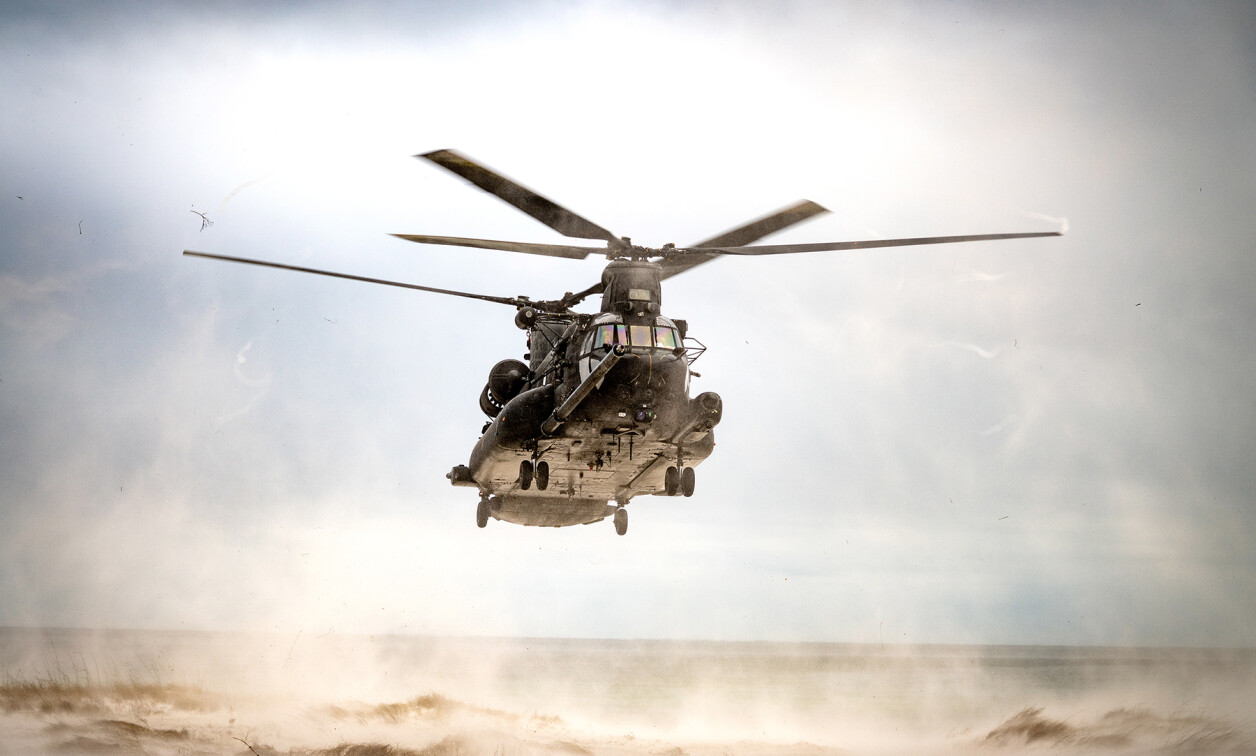
Distributed multidomain and joint all-domain operations (MDO and JADO, respectively) are becoming the defining doctrines of a new era on the battlefield. JADO integrates platforms, sensors, weapons, and joint all-domain command and control (JADC2) systems used to synchronize aircraft, ground forces and vehicles, satellites, and ships. An unprecedented onslaught of data involves comprehensive connectivity, which means linking complex sensors, processors, and effectors to support required environmental and electrical performance specifications. Time-sensitive applications, such as tracking, moving targets, and defensive countermeasures, need ever-faster data throughput.
Today’s threats can morph before warfighters receive the new systems designed to counter them. For acquisition decision-makers to keep pace, the U. S. Department of Defense (DoD) endorses a modular open systems approach (MOSA). MOSA seeks to transform system design, development, integration, and sustainment for future military systems.
Yet some MOSA-enabled installations are inadequate because digital architectures lack equally robust interconnects. Interconnect systems should be future-proof while reducing the overall cost of ownership. Interconnects that enable operational systems must be resilient to harsh environments of perpetual combat and training operations. They should further provide significant performance margins to support future capability requirements and upgrades. Finally, as rapid increases in computing power continue unabated, backbones must have sufficient expandability and reliability to maximize functions, whether they depend on RF, microwave, or other architectures.
The solution: Engineers must consider systems trade-offs, balancing critical size, weight, and power with survivability metrics. These factors are vital to MOSA success, which, more than defining cards, boxes, and subsystems, must include interconnects.
Building successful MOSA-enabled digital systems faces four formidable challenges:
- Cable selection, making optimal trade-offs over time and system requirements, e.g., throughput, size, weight, and power.
- Post-installation, ensuring interconnect architectures are effectively designed for installed performance.
- Overall cost of ownership, codifying specifications into solicitations requiring lower life cycle costs via standardization, interoperability, and plug-and-play upward compatibility.
- Staying power, guaranteeing winning choices remain so in three years, when threats have likely morphed.
Ensuring performance after installation
Currently, most programs do not measure performance difference between data cables through pre-installation, post-installation, and operational use. Considering potential damage during installation, validation of post-installation interconnectivity is imperative to establish a baseline for signal integrity. The DoD says that for standardized interfaces, programs must have a method for verifying compliance with the standard.
Although DoD encourages digital modeling, models must mirror data links considering post-installation signal integrity performance. Otherwise, installation itself might cause system susceptibility to degrading factors like changing temperatures, electromagnetic interference (EMI) and mechanical stress, which can affect performance and reduce bandwidth without warning.
Poor cable performance caused by near-end cross-talk (NEXT) increased insertion loss, impedance mismatches, etc., often leading to insidious impacts like auto-negotiation (slowed data rates) with no indication in the cockpit. A system using sub-standard Ethernet CAT6a cables at 10 gigabits per second (Gbps) could move data at 1 Gbps without operator indication. Unintentionally slowed data speeds, induced by poor connectivity, endanger mission-critical systems, aircraft survivability equipment and other sensor systems as well as warfighters.
For illustration purposes only, Figure 1 (left) shows sensor performance differences where the data signal has been auto-negotiated to a slower speed on the left compared to full resolutions throughput on the right.
[Figure 1 (L & R) ǀ Effects of auto-negotiation: A poorly performing cable can cause a system to auto-negotiate to a slower data rate, reducing resolution and diminishing the benefits of expensive sensors.]
Change in system performance can be explained by looking at test results of Ethernet cable performance in Figure 2. This graph illustrates comparative signal testing of three different cables following a simulated installation. Although all three met industry specifications before installation and routing, only one clearly met and exceeded the specified performance after installation. That Ethernet cable maintained a sufficient margin below the specification limit for return loss compared to alternative cables 1 and 2, which either partially failed or failed to meet the specification, leading to poor signal transmission. These results demonstrate that installed performance varies based on quality and resilience of selected cables.
[Figure 2 ǀ Return loss comparison is shown after routing of Ethernet cables.]
Trading off data cables for performance, size, and weight
Robust interconnects are fundamental to mission and maintenance success. From installation through operation, data cables confront rapid temperature and pressure changes as well as potential contamination from fluids like fuels and oils. Several options can maintain signal integrity in this environment. Figure 3 compares the signal loss of two CAT6a cables at an elevated temperature of 100 °C and emphasizes the need for safety margin at room temperature to allow for degradation at elevated temperatures that may prevent CAT6a cables from meeting requirements.
[Figure 3 ǀ Insertion loss comparison of Ethernet cables at elevated temperature is shown.]
As aircraft are upgraded, requirements for data increase exponentially. Planning ahead keeps legacy and enduring fleet aircraft and vehicles ready for upgrades without costly re-wiring efforts. Although CAT6a is the current default choice for copper Ethernet, options are available for CAT8 performance with 4x the data rate at the same size and weight and enabling less costly and complex future upgrades.
Lighter than copper with a much higher weight-to-data ratio, fiber-optic cables are immune to EMI, radio frequency interference (RFI), and crosstalk when transmitting signals. Smaller, more durable fiber-optic cables have evolved to become relevant options for modern aircraft and vehicle applications.
For example, the Army recently selected a fiber-optic interconnect system on its Limited Interim Missile Warning System (LIMWS) for the UH-60 Black Hawk rotorcraft fleet. The system processor serves as the high-bandwidth digital backbone of the system. It houses advanced machine-learning missile warning algorithms specifically designed for complex, high-clutter environments and rapid threat updates. This system is migrating to other Army rotorcraft, including the AH-64 Apache rotorcraft. The fiber-optic cable system easily handles this current requirement with sufficient margin for the next-generation Integrated Threat Detection System.
Lowering overall cost of ownership
Interconnect technology choices benefit design decisions, from maintenance hours, line-replaceable unit (LRU) longevity, and testing to troubleshooting, repair and replacement, and aircraft availability.
For example, the U.S. Army 160th Special Operations Aviation Regiment (SOAR) had an RF cable issue with its aircraft survivability equipment (ASE) systems. After analyzing the issue on the MH-47 Chinook rotorcraft, they replaced existing cables with an alternative designed for the environment. The program office was impressed they no longer had routine failures on an installed cable set. Improved reliability equated to improved availability with reduced maintenance and sustainment costs.
MOSA’s inherent benefit to upgrade capabilities depends on interconnect architectures with significant margin built in during the design cycle. Margin can negate costly, time-consuming interconnect A-kit upgrades when installing new MOSA-enabled capabilities.
Investing in a reliable MOSA future
As new threats proliferate, service personnel will increasingly rely on modular systems, requiring greater data throughput, to keep ahead of the threats. Similarly, acquisition professionals must consider all performance factors and trade-offs against future projected needs. Interconnect technology based on lowest price/technically acceptable solutions will not provide warfighters with the edge they need. Only highly reliable, future-proof interconnect architectures will realize mission and maintenance goals at greatest value to all stakeholders. Decision-makers must acknowledge these vital pieces of the MOSA puzzle.
Jeff Woods is market development leader for W. L. Gore-Americas. Previously he was a program manager at Northrop Grumman. Jeff knows threats firsthand: For 25 years he served as a naval flight officer, retiring at the rank of Commander. During 13 deployments, he flew more than 140 combat missions. Readers may email him at [email protected].
Tammy Yost, Ph.D., is the chief technologist for Defense Systems at W. L. Gore & Associates, Inc. with more than 20 years of experience developing high-performance digital and RF cable products across multiple markets. She can be reached at [email protected].
W. L. Gore & Associates www.gore.com/products/industries/aerospace