International Space Station's 3D printer makes first part in space
NewsNovember 26, 2014
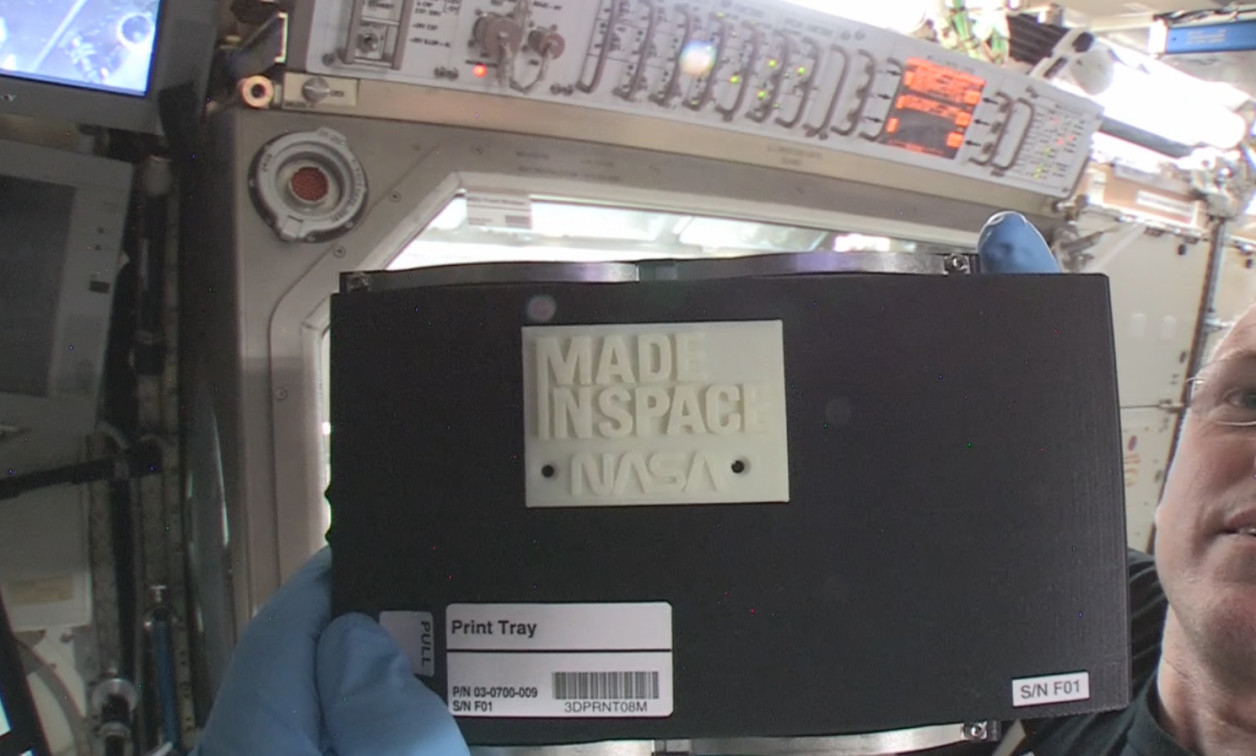
HUNTSVILLE, Ala. NASA officials announced that the crew in the he International Space Station put to use their 3D printer and produced the first 3D printed object in space -- a printhead faceplate for the printer. NASA officials see 3D printing of tools and parts as a way to reduce reliance on resupply missions from Earth.
"This first print is the initial step toward providing an on-demand machine shop capability away from Earth," says Niki Werkheiser, NASA project manager for the International Space Station 3D Printer at Marshall Space Flight Center in Huntsville, Ala. The printhead faceplate has engraved on it the names of the organizations that worked together on this demonstration: NASA and Made In Space, Inc.
For more on 3-D printing read "Defense electronics and 3D printing."
NASA worked with Made In Space, Inc., a space manufacturing company that worked with NASA to design, build and test the 3D printer. Made In Space is located at NASA’s Ames Research Center in Moffett Field, Calif. Made In Space engineers commanded the printer to make the first object while working with controllers at NASA’s Payload Operations Integration Center in Huntsville, Ala. As the first objects are printed, NASA and Made In Space engineers will monitor the manufacturing via downlinked images and videos. The majority of the printing process is controlled from the ground to reduce crew time required for operations.
The printer was installed on Nov. 17, then a first calibration test was made. Based on test print results, the ground control team sent commands to realign the printer and then printed a second calibration test on Nov. 20. These tests verified that the printer was ready to go. On Nov. 24, ground controllers sent the printer the command to make the faceplate.
The 3D printer uses a process, more commonly known as additive manufacturing, to heat a relatively low-temperature plastic filament and then extrude it one layer at a time to create the part defined in the design file sent to the machine. For a video on NASA's 3-D printer click here.
The part was removed from the printer on the morning of Nov. 25. When they inspected it astronauts found adhesion on the tray was stronger than expected, which might mean layer bonding is different in microgravity. A new print tray was installed and the ground team then sent a command to fine-tune the printer alignment and printed a third calibration coupon. Once the third calibration coupon is removed, the ground team will then be able to order the printer to make its second object. Precise adjustments are made by the ground team before every print to help understand how to effectively use 3D printers on the space station.
The first 3D printed objects made in space will be returned to Earth next year for further analysis and comparison to identical ground control samples made on the team's flight printer once final flight testing was completed earlier this year at. The goal will be to verify the 3D printing works the same in microgravity as it does on Earth.