Unmanned aircraft certification challenges
OtherApril 21, 2017
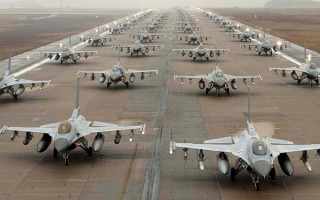
The industry understands how to enable safety certification for manned aircraft ? fixed and rotary, commercial and military ? but enabling such reliability on unmanned platforms remains a challenge.
“Unmanned systems are kind of hard because we still don’t have a full understanding of how to certify them,” says George Romanski, president and CEO of Verocel, in Westford, Massachusetts. “They are using DO-178C for aircraft components and aircraft systems, but even the FAA hasn’t fully found a way of certifying the unmanned vehicles. For the small ones it’s easy, class one and class two, they are light, they’re simple.”
Calling these platforms unmanned may also be inaccurate, say some. “There really aren’t any unmanned aircraft,” says Greg Tiedemann, Director, PLM & BD, Mission Systems Group, Mercury Systems in New York City. “At the end of the day, a UAV [unmanned aerial vehicle] is manned, it’s just the person isn’t in the aircraft. Rather, they’re on the ground. That’s a big difference. That’s important because even though UAVs are flying around up there, somebody’s controlling it. There is a level of safety that’s already in the system. The person is making a decision on whether to turn left or turn right and they can see ahead of that there’s another aircraft that must be avoided, whatever it might be.”
On the one hand, “the challenges are going to be when the UAVs are taking data from the sensors in the UAV, and then the UAV is going to autonomously decide what to do based on that sensor data,” he continues. “You can draw some similarities to what’s going on in the automotive market today, where you’ve got sensors in a high-end Audi or a BMW or a Tesla. You don’t see that completely in the UAV market today, but that could be coming, where some sensor data in the UAV is going to decide whether the aircraft climbs or turns or does something dramatic to avoid collision or steer to a particular mission or whatever they’re going to do.”
Mercury Missions Systems offers the Rock-2 (see Figure 1), a 3U OpenVPX, safety-certifiable, processing subsystem for avionics and command, control, communications, computers, intelligence, surveillance, and reconnaissance (C4ISR) applications.
Figure 1: Mercury Mission Systems’ Rock 2 for C4ISR applications. Photo courtesy of Mercury Mission Systems.
![]() |
|
|
(Click graphic to zoom) |
The real challenge will be with military certifying unmanned aircraft. “The military had a pass for a little while for UAVs, and that is starting to end now, so the challenge is that the military now has to adopt the civil requirements,” Romanski adds. “They have to meet the DO-254 and DO-178C requirements. They have to generate that much more documentation and they can’t self-certify anymore, so they’ll have to get the FAA involved.”
The certification process for military and civil aircraft are similar “in that the military side tends to use DO-178C for certification except where the FAA says, ‘you must use DO-178C or equivalent,’ he continues. “The military then makes their own assessment as they look through the materials.”
With a number of military projects under Verocel’s belt, the DO-178B or DO-178C were called out as a requirement. “So we developed everything as if it was for the FAA, but now the aircraft certification office from the military site takes a look at this, and then they say, ‘Yep, good enough. Yeah, we like it.’ And then they sign off,” Romanski explains.
“DO-178C has a pedigree, it’s been written and developed and we follow what the good book says,” he adds. “On the military side, some programs are very true to the interpretation of DO-178C, but what I found is some other programs tend to say, ‘well it’s good enough, it’s okay. If it’s cheaper you don’t have to do this part.’ That’s a little bit disappointing at times.”
The military does not mandate DO-178C, but they require the equivalent processes and activities of DO-178C, Romanski continues. “In fact, one of the things that is currently used, that the FAA uses, is an SOI, Stages of Involvement. During the audit, they will use the SOI checklist to make sure that all of the requirements of the DO-178C has been completed. The military uses the same SOI checklist. Now we don’t like it, or at least I don’t like it, because I think it draws out a ‘checklist’ mentality, but we find that the auditors much prefer to use a simple checklist because it makes their job easier.”
In the long run it will be up to the lawmakers to give the public confidence that UAVs can fly safely in civilian space with com¬mercial aircraft. “I think we, as a society, really haven’t yet addressed how to integrate unmanned vehicles of all types,” says Scott Engle, director of business development at Mercury Mission Systems, in Tucson, Arizona. “I think the legislation is woefully behind the technology at this point.”
As the complexity of aviation systems rises, certifying safety-critical systems in manned and unmanned aircraft has pushed engineers towards automation and working in parallel to increase the efficiency of the process. Multicore processors are playing a major role in this push, along with added tools to ease the process. However, challenges remain as the Federal Aviation Administration (FAA) and European Aviation Safety Agency (EASA) work toward streamlining the process.
To read the complete article: Next-gen aviation systems see push for automation, multicore processors in the certification process