Leveraging technology for military fleet optimization
StorySeptember 11, 2024
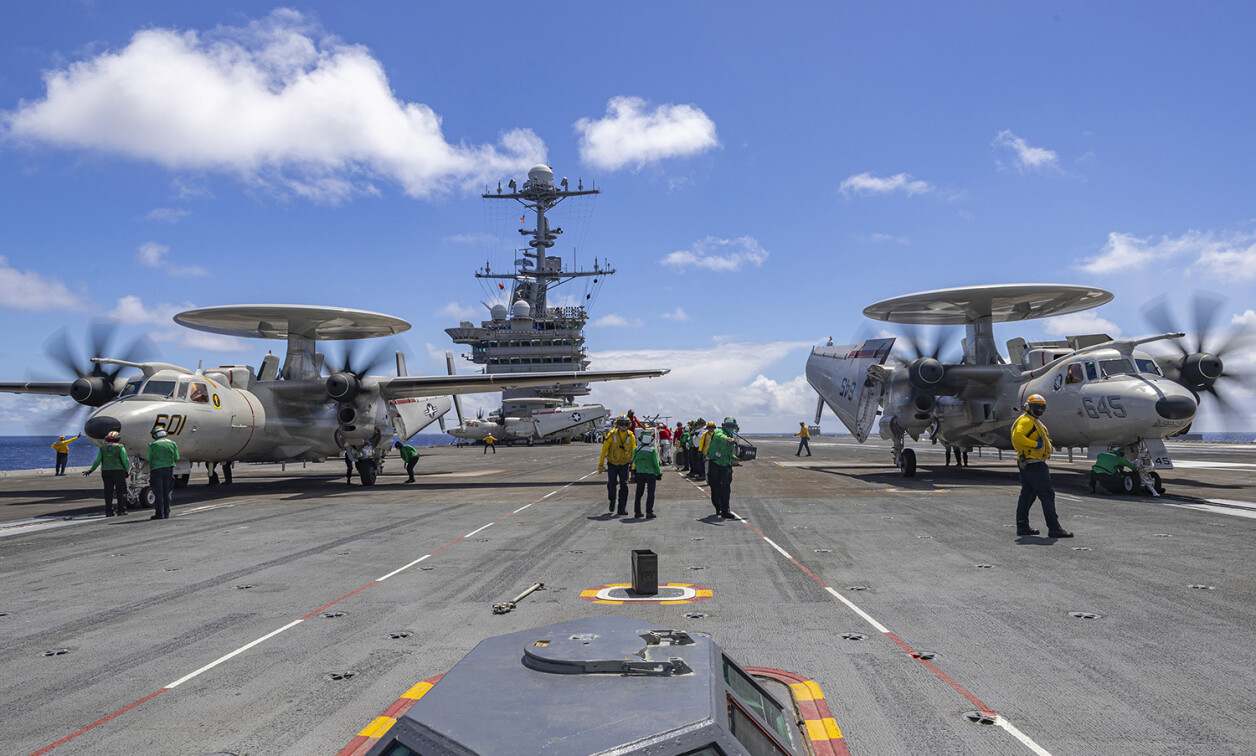
Military aviation depots must overcome many hurdles to maintain operational readiness and fleet sustainment. Aircraft maintenance officers in the U.S. military constantly face mounting costs, antiquated support equipment, and challenges around training and keeping maintenance personnel. On top of these challenges, maintenance crews do not know what components of the aircraft need to be repaired or replaced until they open it up, making it virtually impossible to plan ahead for parts and personnel. All of these factors can substantially impact the mission readiness of aircraft fleets. Deployment of predictive modeling software can have a major impact on optimizing facilities, equipment, workflow, and assets in dynamic environments.
For those not familiar with military aircraft maintenance depot operations, here’s a short explanation: Each aircraft arriving at a depot requires its own unique maintenance. This reality is based on the environments it has been exposed to as well as its operational history. In other words, where has this aircraft been flying, what were the environmental conditions, and how long has it been in service? This data is not always readily available to the depot, which creates uncertainty. Combine that with the fact that most components of an aircraft don’t have sensors that can signal potential failures or point out where stresses may warrant repair or replacement.
Needless to say, this makes it very difficult to plan and execute for an arriving aircraft. Now multiply that one aircraft by hundreds of arriving aircraft across all maintenance depots annually, and it is easy to see that optimization is a huge ongoing readiness and sustainment problem.
This problem is further complicated by the fickle nature of global events. Geopolitical shifts can impact military operations with a potential need for rapid deployment and a heightened pace of operations. This uncertainty negatively impacts the ability to make informed decisions and further stretches already thin resources. The current processes simply can’t account for all of this uncertainty which frequently causes delays. These delays then create a domino effect across the entire maintenance chain. As such, the industry needs to consider adopting innovative technology to help effectively implement maintenance and make sure fleets are maximizing readiness.
Deploying decision analysis technology
One answer to overcoming the uncertainties facing military depots is to deploy decision analysis technology. This technology can help depots more accurately forecast maintenance and staffing decisions even with the potential for extreme uncertainty. With advanced modeling software, it’s possible to predict maintenance needs and outcomes for numerous scenarios. This scenario-based software enables users to test decisions and have visibility into how each decision will impact the process prior to allocating resources. Each step in the aircraft maintenance process has a range of possible outcomes. Leaders and workers alike can analyze these different simulations to account for uncertainty and thus provide more reliable forecasts for maintenance schedules.
In military depots, this approach helps with forecasting and planning to reduce induction wait times from many months to weeks or even days. These moves can increase aircraft readiness and mitigate time lost to out-of-service aircraft waiting on parts and/or personnel. (Figure 1.)
[Figure 1 ǀ U.S. Navy personnel perform routine maintenance on an F/A-18F Super Hornet in the hangar bay of the world’s largest aircraft carrier, USS Gerald R. Ford (CVN 78). U.S. Navy photo by Mass Communication Specialist Seaman Tajh Payne.]
Reducing maintenance cycle times
Shorter maintenance cycles are another crucial piece to ensuring fleet mission readiness. The main roadblocks here are procedural inefficiencies and the resistance of large organizations to change. However, technology and best practices can more than overcome these challenges.
Analyzing current maintenance procedures makes it easier to identify and eliminate any inefficiencies that may have surfaced. For instance, assessing hourly-based inspections across multiple locations can reveal variations in the required person-hours expended for each event. Prioritizing efficiency and standardizing procedures can reduce inspection length – saving both time and resources.
Implementing predictive “condition-based maintenance” software is another way to reduce maintenance cycle times. These systems use sensors and data analytics or sensorless digital twins to predict if and when a component will fail, enabling proactive maintenance before a problem surfaces. The condition-based maintenance approach is much more accurate than the calendar-based maintenance approach, thereby reducing downtime and extending the life of many different aircraft components.
Optimizing the whole process
Deploying predictive modeling software can have a sizable impact on optimizing facilities, equipment, workflow, and assets in dynamic environments. Developing a digital twin of the entire operational process enables comprehensive optimization through simulation.
For example, models can examine the usage and availability of resources, pointing out any potential bottlenecks or other issues. Using modeling guarantees the right people, facilities, parts, and tools are available, reducing delays and improving efficiency.
Moreover, predictive models can improve overall fleet readiness for other operations, such as helping training commands successfully manage flight-training operations across multiple bases. Optimizing aircraft and training schedules leads to significant improvements in pilot production output, ensuring a steady supply of personnel remains mission-ready.
The adoption of advanced analytics is critical to the future of military fleet maintenance. These technologies provide a clear snapshot into the challenging parts of aircraft maintenance and help deliver more precise forecasting, better resource allocation, and significant reductions in maintenance cycle times. Tools like these help military aviation depots keep the necessary high level of operational readiness.
Robert Harrill is the Vice President of Operational Optimization Solutions for Lone Star Analysis. Previously he served as the Director of Maintenance Repair and Overhaul (MRO). Harrill has over 40 years in the defense industry, with 26 of those years serving as active duty in the U.S. Navy as a CWO4 Aircraft Maintenance Officer. After he retired from the Navy, he worked for the Naval Air Systems Command (NAVAIR), supporting PMA-273 and the PEO in acquisition and sustainment. He obtained his Level 3 ACQ DAWIA [Defense Acquisition Workforce Improvement Act] certification. Readers may reach the author at rharrill@lone-star.com.
Lone Star Analysis https://www.lone-star.com/