DARPA teams make advances in the field of uncertainty quantification
NewsMay 18, 2017
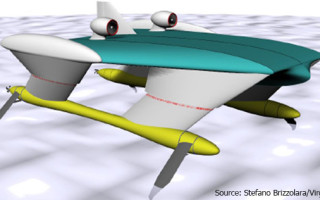
ARLINGTON, Va. Defense Advanced Research Project Agency (DARPA)?s Enabling Quantification of Uncertainty in Physical Systems (EQUiPS) program has made advances in the field of uncertainty quantification ((UQ), which focuses on methods to estimate how accurate a prediction may be. The program aims to harnesses advanced math to quantify uncertainties in complex systems to be able to better design yet-to-be-built military systems.
Within the program, researchers have developed mathematical tools and methods to tackle the challenges associated with large systems of many variables and account for the uncertainty in every step of the modeling and design process.
With advanced UQ tools, designers can better understand the risks involved in pursuing certain designs. With that information in hand, the chances increase that new designs for complex military vehicles, vessels, air- and spacecraft will perform as anticipated when a prototype is first built and tested.
In certain instances, models have proved to be inadequate because data is missing or there is incomplete information about the conditions the system will operate in. Consequently, designers find it difficult to predict how a system will respond or how much confidence the designer can reasonably have in the design.
“With EQUiPS we’re drastically changing the way we model and simulate physical-world, engineered systems,” explains Fariba Fahroo, DARPA program manager. “We aim to make UQ a tractable part of simulation and modeling even for the most complex of design problems. And the mathematical tools we’re developing should apply widely in areas ranging from new aerospace structures to leading-edge integrated circuits.”
While advanced computational tools and improved testbeds such as special wind tunnels or sea-simulation facilities have enabled engineers to develop and test designs for existing systems, newer designs looking at completely different regimes cannot be physically modeled. Hypersonic airspeeds in excess of 13,000 miles per hour or sea vessels able to slice through water at 120 knots, for example, have many uncertain parameters and therefore, need UQ methods to help produce better designs.
The EQUiPS program – initiated in 2015 - completed its first phase. It showed success by accounting for uncertainties that would otherwise interfere with performance predictions for newly envisioned high-speed marine vessels and exhaust nozzles for advanced supersonic aircraft engines.
The Brown University research team is developing theoretical foundations for what they call “Design Under Uncertainty (DUU).” DUU aims to simplify design processes for unconventional defense systems where the number of parameters can be in the thousands and the design requires taking into account such variables as uncertain operating conditions, novel materials whose behavior may not be fully understood, and manufacturing imperfections whose relevance has yet to be determined.
Under the program, the team has been designing an unconventional hydrofoil surface sea vessel that in foilborne mode would achieve speeds of more than 120 knots in calm sea states, and 60 knots in extreme sea states – a performance unmatched by any such vessel today. With no historical data for such a watercraft or its hydrofoil design, engineers needed a model that could account for the overwhelming number of uncertainties. Through the framework developed under the program, the team was able to look at the entire design process, utilize different models, and deliver not only the best design candidate, but also all other possible designs complete with predicted outcomes.
“One of the critical aspects of designing this kind of vessel is the complex physics associated with super-cavitating hydrofoils—structural components that enable an optimum lift-over-drag performance ratio,” Fahroo said. “Few experimental data are available for even simple super-cavitating foils, and resolving turbulent multi-phase flow around 3-D complex structures like these is a computational grand challenge. EQUiPS-based research has led to the development of new concepts of multi-fidelity simulation and risk-based optimization that have reduced the simulation and optimization costs by orders of magnitude.”
Who else is working on the hydrofoil design effort? The Massachusetts Institute of Technology, Virginia Tech, University of California, Santa Cruz, and the Naval Postgraduate School are working with Brown to achieve success within the program.
Another team in the program is lead by Standford University. The Colorado School of Mines, the University of Michigan, and Sandia National Laboratories are working with Stanford on the supersonic nozzle effort.
They are using EQUiPS methods in a study that seeks to optimize the design for a supersonic jet engine exhaust nozzle to ensure maximum thrust efficiency. Current advanced nozzle design practices are unable to take into account the large number of variables involved, including operating conditions and nozzle characteristics, along with the uncertainties associated with these variables.
Focusing on a model similar to an actual aircraft engine, the researchers used new mathematical modeling tools to reduce the number of parameters to a manageable subset. Specifically, applying EQUiPS methods to the aero-thermal-structural modeling of the jet nozzle, researchers were able to reduce the number of nozzle shape parameters, such as size and material thickness, from 28 different features down to seven, turning an intractable design problem into one that is relatively solvable and potentially reducing the design cycle time.
“We see the world in three dimensions, but imagine how complicated everything would appear if it were composed of 28 dimensions—and how much simpler life would be if we could get those 28 dimensions down to seven,” Fahroo says. “That’s what a huge difference EQUiPS approaches can make.”
“Ultimately, we want higher levels of confidence in the performance of a particular design,” Fahroo says. "We want to be able to increase the fidelity of the models and account for the uncertainty of the operating environment, but at a lower computational cost and turnaround time. The EQUiPS research in these various areas is enabling highly effective, robust and reliable design of systems by creating technologies to manage risk and uncertainty during all steps of the design process.”
Check out "Voices of DARPA" podcast with Fariba Fahroo:
[youtube=https://www.youtube.com/watch?v=53jrf0qYTFA;w=529&h=472]