Supply-chain management and obsolescence
StorySeptember 08, 2023
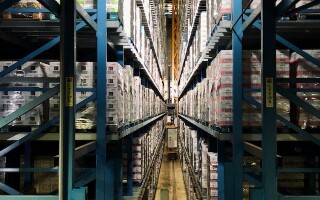
So much of our contributed content – and even our staff-written features – over the past few years have been focused on open architecture initiatives and modular open systems approach (MOSA) initiatives like the Sensor Open Sensor Systems Architecture (SOSA) Technical Standard. We even produce an annual full-sized magazine on SOSA, as well as an issue covering the Future Airborne Capability Environment (FACE). But for the last decade our coverage has often been dominated by the twin topics of obsolescence and supply chain, both of which we cover in this issue.
Fact: MOSA is about leveraging open architectures to bring capability to the warfighter more quickly while enabling lower life cycle costs. Also fact: These systems will help curtail obsolescence by enabling faster upgrades. Even so, all of this still depends on a robust supply chain and, even more importantly, a trusted supply chain.
Starting on page 40, our supply-chain section covers obsolescence management, counterfeit-parts mitigation, trusted sources, and overall supply-chain management.
Shan Morgan of Elma was spot-on in his piece (on page 40) when he described the situation this way: “ … a stable supply chain is critical for both national security and economic strength. And just like a surfer trying to paddle past the break, but who keeps getting rolled back to the shore, managing the complexity of supply-chain solutions needed in today’s defense industry can feel a bit like this same frustrating push-and-pull.”
Military platforms like the B-52 can last decades, while commercial components like semiconductors can have lifetimes as short as six months. We all know the defense industry is at the mercy of commercial component life cycles. This reality is also why the U.S. government is anxious to ensure onshore production of integrated circuits in the U.S so as not to be dependent on Taiwan.
As Dale Lillard, president of Lansdale Semiconductor (Phoenix, Arizona), told me previously, “They don’t make militarized ICs anymore, so the end user is forced to go with COTS [commercial off-the-shelf] technology.”
That shift makes it “more difficult for aftermarket support of commercial parts for military systems today,” he explained. “In the 1980s and 1990s, militarized products were consolidated and the Defense Logistics Agency (DLA) maintained the specifications in a QML [qualified military line], ensuring consistent support from the various manufacturers. The military components were designed into systems and aftermarket suppliers knew they would need to be supported.”
Lillard said he recommends to his customers with long-life systems using commercial ICs that they should make EOL [end-of-life] buys, “as you will never get the parts cheaper and also because you will not get the support that we have provided for military ICs of the 1980s or 1990s.”
The aftermarket business cycle is typically the opposite from the rest of the defense-electronics market, Lillard told me. “When the government doesn’t have money to buy new toys, they make sure they maintain the old ones.”
Regarding authorized suppliers, Lillard still said “there is no other solution except to buy from authorized suppliers.” Doesn’t matter if it’s an automotive part or military ICs, only the original manufacturer knows what they’re doing, he adds.
To demonstrate, he used his favorite analogy: “When I’m working on my 1965 Ford Mustang and looking for replacement parts, I can buy something from China that has on paper all the right information, but when I go to put it in the car I find that the holes don’t match or it’s incompatible in some other way.”
For more on Lansdale Semiconductor, visit www.lansdale.com. For more on aftermarket suppliers, read the article from Rochester Electronics on page 44; the authors, Dan Deisz and Ken Greenwood, also cover the value of authorized suppliers in counterfeit mitigation.
I like talking to the aftermarket suppliers like Dale and Dan and also Ethan Plotkin of GDCA, an aftermarket supplier of single-board computer designs. It’s a unique business, with not many players. Lansdale, Rochester, and GDCA have been doing this for decades; in fact, many of our key military platforms flying today depend on the IC designs they keep alive. Both companies are still supplying parts from the later 20th century.
Regarding counterfeit mitigation, I always think back to a visit I had with Tom Sharpe of SMT Corp. in Sandy Hook, Connecticut: Sharpe broke out a slide show showing a city in China built only on creating counterfeit ICs. It was eye-opening and depressing. Workers washed counterfeit product in contaminated rivers. Imagine that getting into a consumer product, let alone a military fighter jet. The counterfeiters get better every year, hence the need for multilayer trusted supply chains.
I’ve learned from all these guys. We always talk about artificial intelligence and laser weapons and augmented reality and how exciting those applications are. But many of our mission-critical platforms still rely on parts the grandparents of today’s engineers helped design. That’s a supply chain that has been supported for 50 or 60 years.