Planning for and minimizing the costs of obsolescence in military and aerospace applications
StorySeptember 06, 2023
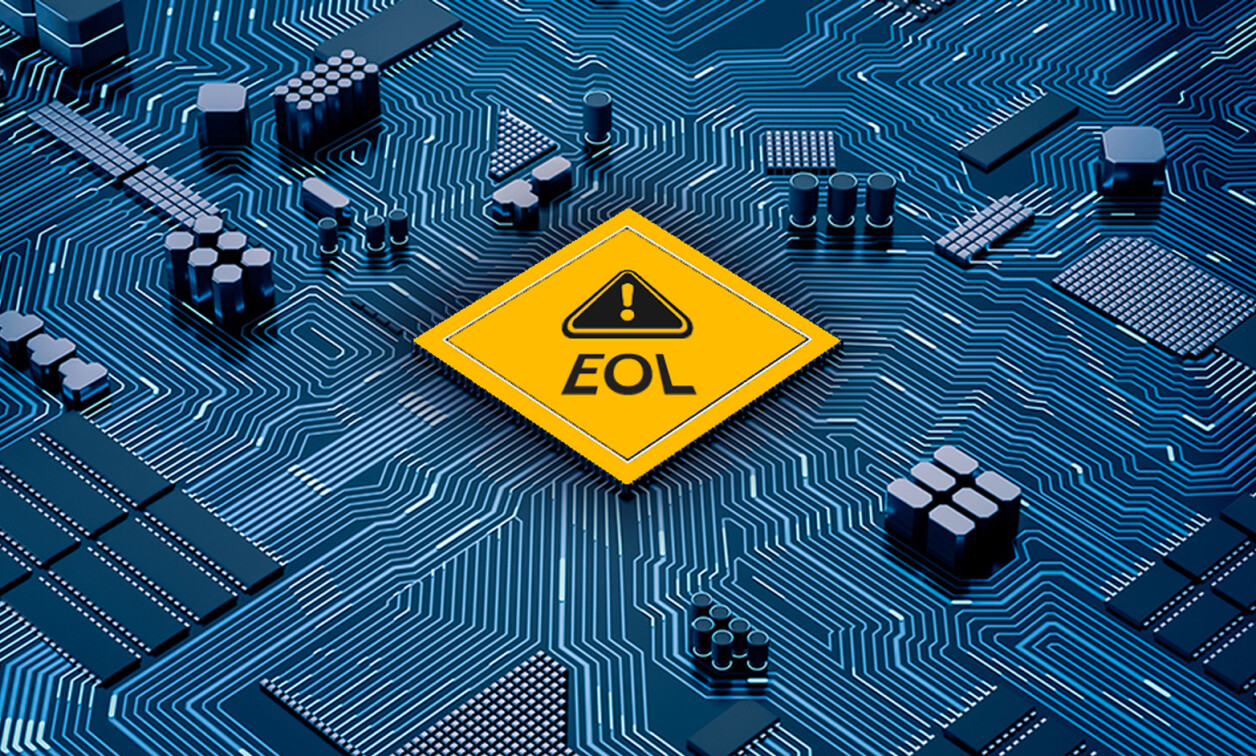
Military and aerospace supply chains are facing greater challenges than ever before, as systems in these arenas require longer development times and have longer production life cycles than any other industry. The industry must work to overcome such obstacles as component obsolescence in aging systems, prioritization of funding for long-term procurement and maintenance, coordination on the timing of and transition to newer systems, and lengthened budget cycles.
The investment and component life cycle decisions of top semiconductor manufacturers are driven by high volumes, demand for higher performance, lower power requirements, smaller plastic packages, and cheaper costs. Moreover, expected product life cycles can be as short as a single year, or can be as long as five to ten years. Overall, while industry certainly benefits from technological advancements, semiconductor life cycles do not align to the time requirements of most military programs.
When faced with critical-part obsolescence, manufacturers need to find reliable replacements that not only address single-replacement events but also cover the requirements for the full life cycle of a program. Redesigns are an option, but often entail costly development, testing, and requalification. Normal customer/supplier relationships rarely allow customers to work directly with the semiconductor suppliers to extend technologies, or transfer intellectual property (IP) to prolong component life. Finding replacements in the “gray market” is a hugely risky route, one that raises the prospect of illegal or counterfeit supply.
1. Obsolescence management begins at design and product definition phases.
We have all heard stories of products being launched with obsolete components. This is a particularly relevant issue for customers with lengthy development and qualification cycles. Choosing the right component technology and supplier can have dramatic impacts on long-term availability. The lowest-cost sources may not be the best choice for long-term supply. Understanding the risks associated with component selection during the design and product definition phases requires a deep understanding of the timeline for long-term system development and when components are introduced by the semiconductor company. Market misalignment occurs when a long-term system is designed using short-term market products or already-mature products. Architecture misalignment occurs when the choice of processor architecture is clearly close to the end of its life, usually when the cost of architectural change has postponed an inevitable future. Board design misalignment is what happens when board layouts knowingly specify densely packed, shifting commodity products. Component selection during development often leads to potential premature product redesigns and requalification, as component choices are frequently influenced by the aim of maximizing the potential of older software and hardware solutions.
Market misalignment: There are times when the easy or most efficient component selection is the wrong choice, due to market misalignment. This scenario could be feasible if there is a planned and budgeted last-time purchase within a few years of selecting the components; however, this is seldom the situation. For example, graphics-driver products have a very short lifetime compared with military or commercial avionics displays. Opting for a PC-oriented component in a market where the sole purpose of those components is product development will lead to obsolescence even before the first production units are shipped. When it comes to choosing a graphics driver product up front, it is crucial to consider the long-term system cost and allocate a budget for an early last-time-buy. This move is necessary to safeguard military or commercial avionics displays and avoid obsolescence in a market where PC-oriented components may not meet the requirements of product development.
Architecture misalignment: Commercial avionics has long settled on the PowerPC processor multicore architecture, due to the control for multicore operation and speculative execution across multiple processor cores. The existing multicore PowerPC products have been certified for commercial avionics and software development is proven. It is also true, however, that the end of the PowerPC architecture is on the horizon. It is only a matter of time before the commercial avionics market adopts Arm or RISC-V as its favored architectures. Every single PowerPC-based product being designed today is already on a processor product line that is over a decade old.
Board design misalignment: There is always the temptation to pack DRAM [dynamic random-access memory] as tightly as possible. Many systems have variable amounts of DRAM, whether to enhance the product or to provide tiers within a product family. Packing that DRAM into the smallest possible space could be an advantage. However, the challenge with long-term systems lasting 15-20 years is that DRAM technology will evolve markedly within that time. It is crucial to anticipate this change by strategically designing board layouts up front, thereby minimizing the need for large future modifications.
Market misalignment: Memory products are designed for short-term systems. Fact: The largest memory suppliers no longer stock DDR3, but – coincidentally – DDR3 is the primary memory type supported by the latest PowerPC product. Designing long-term systems without a long-term memory product plan up front is an issue. Memory has been a fast-moving product for decades, as innovations occur at a rapid pace to keep up with data center demands and portable product demands. Long-term systems are a misaligned use for all memory types because all memory types are short-term products.
When addressing obsolescence end users need to consider a number of key questions:
- What is the component’s life cycle status across the application’s lifetime? Not only does the end product’s lifetime need to be considered in component selection, but when the component’s lifetime started, as well as the product’s lifetime start dates and end dates, must be accounted for. Choosing the right components means alignment of product dates with all component dates.
- Are the key components of the design comprehensively documented? Changing software costs about 10 times more than changing hardware. Any component that is directly controlled by software will be the most valuable to keeping a long-term system shipping. These components are typically the highest price items in a BOM [bill of materials] as well. The documentation and archive requirements associated with these types of components must be elevated to alleviate long-term system risk of sustainment.
- Can the true design files (VHDL, Verilog, SPICE models, constraints, source test vectors) be archived at the design phase to offer a chance of rebuild if the unexpected happens? This question pertains to the most intricate, expensive, and software-dependent products: To minimize maintenance risks, it is crucial to create an archive that contains all relevant information about these products. This archive should be independent of any EDA [electronic design automation] tools and operating systems.
- Does the design contain proprietary IP? If so, the ability to “port” such designs when the components are made obsolete may be compromised, or subject to relicensing and royalties. Embedded IP blocks, particularly within FPGAs [field-programmable gate arrays] and ASICs [application-specific integrated circuits], are commonplace. However, these IP blocks can also make portability and sustainability almost impossible if efforts are not taken to ensure there is a plan for these products. This plan may have to be a fully funded last-time buy or IP licenses up front that allow porting from one technology to another. Simply clicking a button and incorporating IP blocks (presumably because it’s easy to do so) is not a solid long-term system plan. If IP blocks are not incorporated into a long-term plan at the design phase, it may be impossible to come back to them years later for a solution.
Many companies do almost none of this planning for long-term systems in the design phases where the impact would be maximized. From component selection all the way through IP block selection, there are many ways a long-term system company can mitigate risk and schedule for system longevity.
2. Understanding the total costs of obsolescence
It is important to understand and model the costs and risks associated with obsolescence.
Key questions:
- Does the project plan need to include anticipated product refresh or redesign during its life? If yes, how will it be funded?
- How will the business account for the capital locked down in long-term component sourcing?
- What will the component obsolescence impact be on after-sales service commitments?
- What effect would a shortened product life cycle have on customers and end users?
3. Planning for obsolescence and resource management
If the equipment has long qualification, production, or in-service time frames, it will face component obsolescence. Best-in-class organizations devote skilled multidisciplined workers to handle obsolescence management. Preventative planning can reduce or eliminate cost and risk.
4. Identify important product discontinuation notices (PDNs) that may affect the business and monitor them.
Proactively monitoring component life cycles is crucial to anticipating problems before they occur. Excellent commercial tools are available that can track a component’s life cycle, lead times, and specification changes. Such tools provide alerts that can be triggered when PDNs are issued.
Key questions:
- Will sub-tier suppliers share their BOMs?
- Do sub-tier suppliers have adequate obsolescence-management processes in place?
While many electronics manufacturers offer proactive component life cycle management as a service, others are completely reactive. PDN notifications are typically only aimed at the direct purchasers of the component of the last two years.
5. Last-time buy (LTB) –What to forecast?
Forecasting is not an exact science, and it is likely that forecasts will be inaccurate. It is difficult to anticipate product needs years in advance or possible market disruptions. Underestimating needs has a risk of prematurely terminating a product, while overestimating ties up unnecessary capital in stock and excessive storage costs. If a redesign in the future is planned to limit the cost of the LTB, then the design, requalification, and the opportunity costs of using engineering resources must all be factored in.
6. Purchase from 100% authorized sources
There is a misconception that when a component is discontinued that unauthorized or gray- market sources are the only option. The risk-free option of an authorized after-market supplier should always be the first choice.
The risks of counterfeit and poor-quality components from unauthorized sources represent a significant risk to production yields and mean time between failure rates (MTBR) in the field. Inferior or substandard testing by unauthorized third parties provides a false veneer of confidence that authenticity can be tested. This mimicry of testing may be a visual, an x-ray, or a poor partial copy of the original manufacturer’s test processes. Full tri-temp testing is rarely offered, and the risk of commercial-grade components being remarked as industrial, automotive, or military parts is always possible. (Figure 1.)
[Figure 1 ǀ Inferior or substandard testing of electronic components by unauthorized third parties may give a false sense of confidence that parts are authentic.]
Unauthorized component risks include:
- Poor handling, resulting in electrostatic damage and the destruction of the device.
- Poor storage, whether in excessive heat, cold, or moisture during any part of its storage life. Risks include external lead corrosion, failed solderability, moisture ingress, and/or a catastrophic failure of the device.
- Fake documentation that mimics the original specification or lies about performed tests.
- Recovered, re-marked, or repackaged components masquerading as another product.
There are also documented quality problems related to cleaning chemicals used to recover, wash, and re-mark used components, which can slowly migrate into the products, shorting and corroding bond wires and pads. Superficial testing is not guaranteed to find these faults. Although recovered components may pass these tests and survive for a period in service, their inevitable failures will destroy MTBR figures and result in reduced reliability and damaged reputations.
Original component manufacturers (OCMs) do not provide guarantees for products purchased through unauthorized channels. Providers who are not fully authorized may market themselves as AS6171/4-compliant. While better than no compliance at all, if AS6171/* testing is offered in isolation, this potentially indicates that the parts were not sourced directly from the OCM but have only passed AS6171 testing. This merely minimizes but does not eliminate risk.
Fully authorized distributors are compliant with the SAE Aerospace Standard, AS6496. Simply stated, they are authorized by the OCM to provide traceable and guaranteed products with no quality or reliability testing required because the parts are sourced from the OCM. (Figure 2.)
[Figure 2 ǀ Component manufacturers that are not fully “authorized” but market themselves as “compliant” may offer parts that are not usable for critically important installations in military and aerospace applications.]
Bottom line: Expect and plan for the unexpected. The unique qualities of many military and aerospace designs add to the challenge of finding viable solutions to obsolete components. It is more vital than ever before to have partners who can support businesses during unforeseen or unplanned component discontinuations, completely risk-free whenever they occur.
Dan Deisz, Rochester Electronics’ vice president, design technology, has more than 35 years of semiconductor design experience. Dan’s group performs all authorized product replications and customer-specific design solutions. Dan is an active member of the Anti-Counterfeiting Task Force (ACTF) for the Semiconductor Industry Association (SIA) and has trained more than 200 CBP/HSI [U.S. Customs and Border Protection/Homeland Security Investigations] agents. Reach him at ddeisz@rocelec.com.
Ken Greenwood has over 30 years of experience in the electronics industry, working in strategic roles at Nortel Worldwide and Matra Comms France before moving into management roles in the connectors and RF/microwave markets. In his current role as Rochester Electronics product & technology solutions manager EMEA, Ken interfaces with Rochester’s supplier partners and the market. Email Ken at kgreenwood@rocelec.com.
Rochester Electronics https://www.rocelec.com/