Hypersonic weapons systems: Getting in sync with MEMS-based timing
StoryFebruary 15, 2023
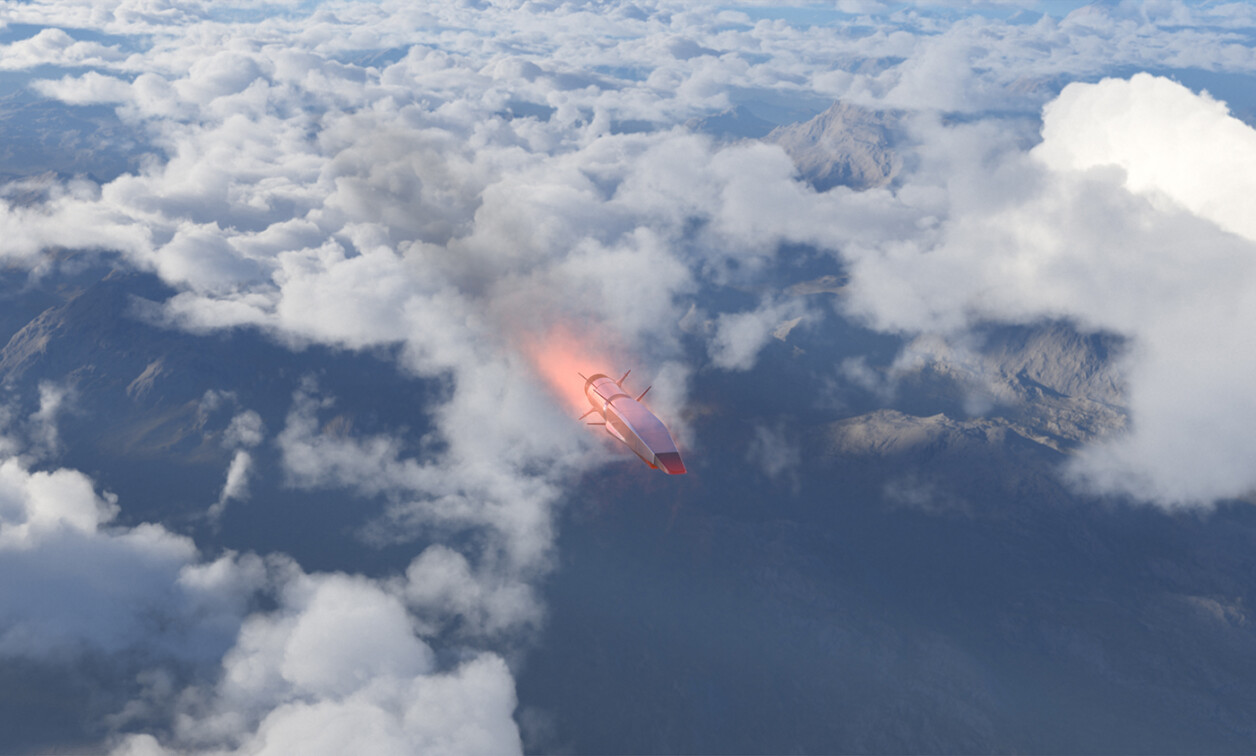
Quartz-based timing components have provided timing references for aerospace and defense applications for many decades. While quartz-based oscillators have been enhanced over the years to mitigate their shortcomings, they still have inherent disadvantages that make them a weak link in the design of next-generation defense systems such as hypersonic weapons systems.
The industry is transitioning to timing devices based on microelectromechanical systems (MEMS) technology to overcome these shortcomings. MEMS-based timing devices outperform their crystal-based counterparts across many key metrics. They are smaller, more reliable, rugged, and ultra-stable over time, temperature, acceleration, and vibrations, which makes them better suited for extreme operating environments, including hypersonic systems.
Hypersonic weapons are ultrafast, low-flying, agile, and highly maneuverable missiles and glide vehicles designed to travel at speeds between 3,000 and 15,000 mph. They are are capable of changing their trajectories to avoid detection and defense systems. High temperatures and high-temperature transients create challenges for timing devices, sensors, and other electronic components, including radomes and antennas. Moreover, timing devices in hypersonic systems pose unique challenges because they synchronize mission computing, flight control, real-time signal processing, and communications – all while facing many environmental challenges, from extreme temperatures and pressure to vibration, shock, and extremely high G-forces.
MEMS timing technology overview
MEMS-based oscillators – first introduced in 2006 – have continued to evolve their use of timing technology, including temperature compensation and phase-locked loops (PLLs), to deliver significantly higher frequency stability, lower jitter, and phase noise.
MEMS timing devices are designed to be free of spurious mode crossings with the fundamental mode and free of resonator-induced activity dips. The MEMS device uses a single mechanical structure of pure silicon with a tensile strength of 7 gigapascals (GPa), which is about 14 times higher than titanium’s 330 to 500 megapascals (Mpa).
The reliability of a MEMS oscillator is significantly better than that of a quartz oscillator, which has a much higher failure rate. Figure 1 illustrates the reliability of MEMS oscillators, measured in mean time between failure (MTBF) when compared to quartz-based oscillators, and shows that the MTBF of MEMS oscillators is over 2.0 billion hours – about 50 times greater than quartz-based oscillators.
[Figure 1 | The MTBF of MEMS oscillators exceeds that of typical quartz-based oscillators.]
Contaminants are controlled to an ultra-low parts-per-billion (ppb) level, while a process at 1,100 °C step-anneals the silicon crystal applied to the wafer. This process is done in an extremely pure high vacuum. The resulting clean resonator cavity effectively eliminates resonator aging mechanisms. Figure 2 shows a typical 10-year aging specification for a MEMS oscillator, at +/-400 ppb vs. +/-3,000 ppb for quartz.
[Figure 2 | Aging specifications are shown for a particular MEMS oscillator versus quartz-based counterparts.]
Quartz-based oscillators are typically housed in an open-cavity ceramic package with the IC and quartz resonator bonded to the package substrate with a different type of adhesive. In addition, each quartz device is individually trimmed to the desired output frequency using either ablation or deposition of metal onto the quartz resonator. The adhesives and metal trimming can be a source of contamination that can age a quartz resonator through mass loading and reduces reliability.
In contrast, MEMS resonators have about 1,000 to 3,000 times lower mass than quartz resonators and therefore are more resistant to shock and vibration. Acceleration imposed on a MEMS structure from shock or vibration will result in a lower force than on the quartz equivalent, which will induce a much lower frequency shift.
Another measure of vibration sensitivity is the frequency shift per g of applied sinusoidal acceleration. The most common unit of measurement is parts per billion (ppb) frequency shift per g of acceleration or ppb/g. Figure 3 shows the total acceleration sensitivity gamma vector (over three axes) of 30 MEMS units over vibration frequencies from 15 Hz to 2 kHz. The maximum observed value of only 0.0058 ppb/g is the best performance achieved.
[Figure 3 | MEMS units’ vibration sensitivity gamma from 15 Hz to 2 kHz is shown.]
Shock resistance is another key parameter for hypersonic systems and is a metric in which MEMS technology outperforms quartz technology. For example, SiTime Endura products are shock-tested up to 30,000 g (a multiple of the acceleration of gravity), which is significantly higher than most quartz products can achieve. To put this into perspective, a 155 mm howitzer projectile experiences a peak acceleration of 15,500 g over a 9-ms pulse. As typical system design margins are 1.5 times, this implies that 155 mm projectile components should be certified for up to 23,250 g.
Looking at oscillator technology
Recent advances in MEMS technology produce additional benefits, such as resilience to fast-temperature ramps and low-phase noise. One resonator is used as a temperature sensor, exploiting its relatively steep but linear -7 ppm/°C frequency versus temperature slope. The other resonator provides a reference clock for the downstream PLL, designed to have a relatively flat frequency-versus-temperature slope. Tight thermal coupling between the resonators results from their 100 µm fabrication on the same die substrate, eliminating the thermal gradient between them.
In contrast, the temperature sensor in a quartz-based temperature-controlled crystal oscillator (TCXO) is integrated within an IC sitting below the quartz resonator on the ceramic package substrate. The spatial separation between the temperature sensor and resonator creates a substantial thermal gradient between the two elements, introducing significant frequency error when subjected to fast thermal transients.
A key element of the MEMS temperature compensation architecture is the temperature-to-digital converter. As shown in Figure 4, this circuit block generates an output frequency proportional to the ratio between the frequencies generated by the two resonators. It has 30 microKelvin (µK) temperature resolution and bandwidth up to 350 Hz, enabling excellent close-to-carrier phase noise performance and Allan deviation (ADEV) performance.
[Figure 4 | A typical temperature-to-digital converter.]
ADEV is a time-domain measure of frequency stability. The main advantage of ADEV over standard deviation is that it converges for most noise types and is used for characterizing the frequency stability of precision oscillators. Good ADEV performance is critical for hypersonic weapons, satellite communications, and various precision global navigation satellite system (GNSS) applications.
Frequency response to fast thermal transients
Figure 5 demonstrates the benefit of the DualMEMS architecture during fast thermal transients. This example shows the results of a heat gun simultaneously applied to two devices: a SiTime DualMEMS Super-TCXO and a ±50 ppb quartz-based TCXO. In response to the heat gun stimulus, the quartz TCXO deviates up to 650 ppb peak-to-peak from nominal temperature, exceeding its data sheet specification by a factor of up to 9. The frequency change of the DualMEMS Super-TCXO is barely noticeable, about 3 ppb or less, far below its specification limit of 100 ppb.
[Figure 5 | Screen shot of a +/-50 ppb quartz TCXO versus a MEMS Super-TCXO under fast temperature ramp conditions.]
Air flow is another system stressor in hypersonic weapons and can cause die temperature changes produced by fluctuations in heat flow from the oscillator. Rapid, turbulent air flow can have an even more pronounced effect on heat flow from the oscillator to the environment and, in extreme cases, can cause vibration effects.
Power-supply noise rejection
In addition to external stresses, hypersonic weapons systems are subject to internal system stresses, such as power-supply noise, which can produce data errors. It is critical for the oscillator to maintain low phase noise and jitter in the presence of noise on the power-supply line to maintain optimal system performance.
Power-supply noise rejection (PSNR) is a measure of the oscillator’s resilience to power supply noise. PSNR is the ratio of output jitter in picoseconds (ps) divided by the amplitude of the injected sinusoidal jitter on the supply pin in millivolts (mv). The MEMS device’s low jitter is achieved using multiple on-chip low-dropout regulators that isolate critical components such as the VCO and MEMS oscillator. Figure 6 shows a MEMS oscillator’s peak-to-peak jitter and superior PSNR compared to quartz oscillators from six different suppliers.
[Figure 6 | Power-supply noise rejection of a MEMS DE-XO versus typical quartz oscillators.]
Hypersonic systems will be among the most effective defenses, with maneuverability and exceptionally high speeds. The harsh conditions that hypersonic weapons must endure – such as very high temperatures, rapid temperature changes, and extreme levels of shock and vibration – also can be devastating to their system-level components. MEMS oscillators can outperform their quartz-based predecessors, as they meet the demanding performance and reliability requirements of hypersonic technology.
Odile Ronat is director of product marketing, Aerospace and Defense, SiTime. Prior to SiTime, she worked at International Rectifier/Infineon in the high-rel and rad-hard groups. She holds an MS in engineering from École des mines de Paris and an MS in engineering management from Stanford University (Palo Alto, California).
SiTime https://www.sitime.com/