Military rad-hard design activity robust despite supply-chain headaches
StoryJune 23, 2022
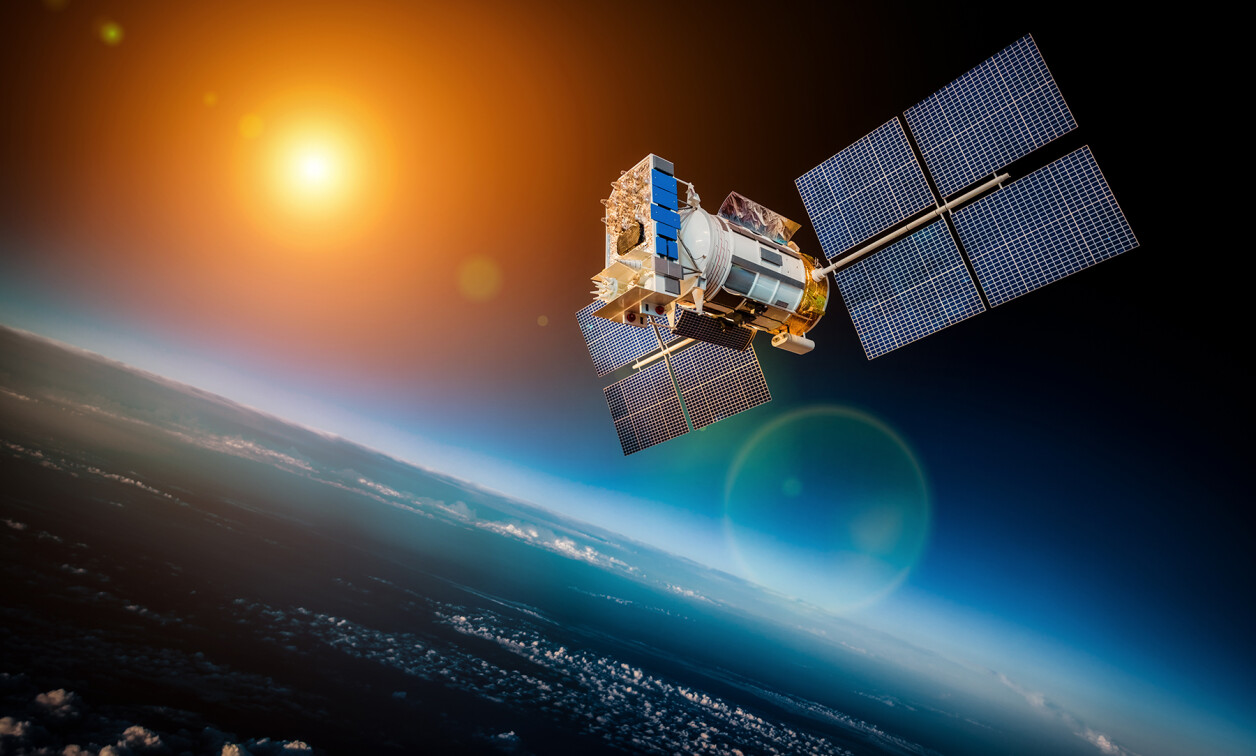
Military funding – not only for traditional long-life missions but also for nontraditional shorter life, lower-cost small satellite applications – continues to grow. Radiation-hardened component designers are working to meet the reduced size, weight, power, and cost (SWaP-C) demands of these new missions while maintaining radiation tolerance and dealing with the supply-chain headaches that continue to plague the electronics industry.
Robust growth in the radiation-hardened (rad-hard) component arena is due in part to the growing adversarial threat in space from nations like China, which motivates more funding from the U.S. Department of Defense (DoD). Mounting demand can also be ascribed to the success of lower-cost New Space applications like small satellites (small sats) and Low Earth Orbit (LEO) megaconstellations or satellite swarms.
Evidence of that motivation is seen the Air Force Fiscal Year 2023 DoD budget request, which provides increased funding for the Space Force. Examples of that investment, according to the Air Force, are the funding request for $987 million for space technology development and prototyping missile warning/tracking as well as the $1 billion requested for ground and space segments of the Next-Generation Overhead Persistent Infrared (OPIR) missile-warning system.
“We’re seeing stable activity with business growing in the military market. Previewing the DoD budgets, we see those and what’s requested and it’s steady looking forward,” says Bob Campanini, Vice President of Optoelectronics, for Micropac (Dallas, Texas).
The DoD funding commitments and market pressures are affecting the growth in rad-hard designs.
“We are seeing a very diverse and interesting market for radiation-hardened and radiation-tolerant components and systems today,” says Ken O’Neill, Associate Director, Space and Aviation Marketing, Microchip Technology (San Jose, California). “Every segment of the market is very active at the moment. There seem to be many different factors at play. U.S. and international funding for human spaceflight, increasingly ambitious robotic and autonomous missions, elevated priority on defense early-warning and communications systems, and commercial ventures offering earth observation and communications services are all factors in today’s buoyant space market.”
“Designs are constantly churning. The increased U.S. investment in military space is driving growth in classified and unclassified applications. The small sat business is growing even faster,” says Anton Quiroz, President of Apogee Semiconductor (Plano, Texas).
Manned missions are also getting funding dollars. “A lot of attention is going to shorter mission length in certain orbits but there are other longer, manned missions that have driven a lot of testing,” Campanini says. “The architectural approach of having multiple instances of the same satellite drive an attractive volume production for constellations. Of course, the radiation exposure to devices and signal paths does depend upon the intended orbit, potential shielding from the physical build decisions, choice in radiation tolerant device materials. Materials such as fiber optic signal paths seen great supplier advances in radiation tolerance and are inherently resilient to electric and magnetic fields.”
Long-life classified missions are still critical to the U.S. military, but there is increasing demand for shorter-life systems that are low-cost and high-performance that can be deployed more quickly than a traditional military-satellite mission.
“When electronics is involved, the ’hottest application‘ is always the highest volume application and currently that is the (small sat) LEO constellations,” Campanini says. “Several of these end applications drive the same/similar demands for electronics. LEO small sats and manned space flight have similar radiation needs (minimal radiation requirements if humans are also present). Manned missions drive other requirements related to redundancy, fault tolerance, and fail safe.”
“Military systems are exploring the trade-space encompassing mission success, procurement cost, and time to launch,” O’Neill says. “Traditional systems had high mission success, but were expensive and took a long time to build, test, and launch. While traditional systems are still under development, there are also military systems in development which seek novel ways to reduce cost and development time without sacrificing mission success.” (Figure 1.)
[Figure 1 | Microchip’s portfolio of radiation-hardened and radiation-tolerant solutions includes high performance FPGAs [field-programmable gate arrays], mixed-signal ICs, isolated DC-DC converter modules, custom power supplies, hybrid solutions, MOSFETS, and more.]
Supply-chain shortages
The only obstacle seemingly slowing this rapid growth is the supply-chain shortage plaguing the entire globe. Orders for components are coming in, but delivery delays abound for all types of parts.
“The supply-chain shortage is still haunting the industry,” Quiroz notes. “We still see quotes with 52-week lead times for certain components. Due to this crisis, we see military customs demanding systems be made in the U.S., with DoD investing more in long-term onshore semiconductor manufacturing. Building this infrastructure in the U.S will take time, but it will help and it’s better late than never. The tensions between China and Taiwan are still an issue and a risk factor with an unknown result in the long term, so this investment is necessary. From our perspective, we manage our inventory, maintaining IC components in stock for key contracts.”
It’s not just semiconductors that are on back order, but electronics components of every type.
“The delays have expanded to all materials, ICs, passive components, mechanical connectors, and more,” Campanini says. “It will take a comprehensive approach to overcome these challenges to the military supply chain. Micropac is part of the Defense Microelectronics Cross Function Team, among other consortia, working to overcome challenges to the warfighter. The microelectronics offshore challenge was not created in a year and it will take more than a year to solve. So yes, there will be a risk exposure for a few more years.
“Government funding will help, but that will take time to unravel and to flush out any bottlenecks,” Campanini continues. “They will want to make sure it’s not just a knee-jerk reaction, and that they maintain onshore capability. It will require providing electronics at lower cost – which is why everything moved to Taiwan in the first place. Running semiconductor fabs in the U.S. will be more expensive than in Taiwan due to labor and other costs.”
Many suppliers are expanding their facilities and also their workforces to combat the delays, but no one has yet gotten ahead of the supply curve:
“We see that our industry partners and subcontractors are investing to increase capacity and to hire additional staff, so we expect that the current supply constraints will ease in the near future,” O’Neill says. “Even though longer lead times on rad-tolerant FPGAs are driven more by assembly and screening-cycle times than by semiconductor wafer availability, we still welcome government investment in domestic microelectronics production as it will provide us with more choices for future generations of products and help reduce reliance on foreign sources.”
Some question whether government investment in the short term will be enough.
“The electronics market is fueled by lower costs and customers will always push for lower and lower costs, especially in the commercial markets which drives most of the demand for semiconductors.” Campanini says. “Will this lower-cost desire push production offshore again in the future? A more comprehensive approach beyond simply throwing some money at the short-term needs may be needed to avoid the future pendulum swing back to lower cost, offshore production.
Managing costs and COTS in space
While the supply chain remains a procurement challenge, designers are being forced to innovate to meet reduced size, weight, power, and cost (SWaP-C) demands with commercial off-the-shelf (COTS) while maintaining acceptable radiation-tolerance levels so the systems don’t fail when hit with cosmic rays.
The demand is for rapid deployment of systems with lower costs that are built with system-level redundancy rather than component-level redundancy, Campanini notes. “This makes it tough to pack in rad-tolerance, but the lower mission assurance goes along with the constellation architecture. On a positive side, designing these simpler systems can be done more quickly than larger, more complex systems, so you have a faster time to deployment.”
There is a “consistent trend to lower radiation levels, but guaranteed at those lower levels, in support of the vastly increasing LEO missions,” he continues. “While not to a low enough level to allow use of commercial or non-radiation hardened components without shielding or other system level mitigation features, there is an expectation of significant cost reductions. Semiconductor suppliers are stepping up to provide lower radiation performance products, often in plastic packages at significantly lower costs.
Leveraging commercial manufacturing can also help traditional rad-hard electronics suppliers mitigate some of the challenges with readying COTS components for space applications
“To manage the reduced cost requirements and demand for COTS components, we leverage commercial foundries,” Apogee’s Quiroz says. “For higher-volume applications like small sats, the price points are better than upscreening. When you upscreen a part, you’re basically wrapping a $100 bill around it. With a ground-up commercial silicon process, you’re bolting on the rad-hard components using plastic packaging. This allows you to take advantage of commercial test flows and tailor the product to an aggressive price target and high-volume applications – those that procure more than 100,000 units.” (Figure 2.)
[Figure 2 | Apogee Semiconductor’s rad-hard logic family is available at 30 to 300 krads, with plastic and ceramic package flows, for small sat, military space, and commercial missions.]
Microchip has two complementary approaches to the demands for higher-volume, lower-cost space components, O’Neill says: “One of our approaches revolves around the concept of ‘Sub-QML’ [qualified manufacturers list] devices. This concept takes products which have been designed to provide a high level of radiation tolerance and reduces or eliminates costly QML testing and screening. The result is a product line that has the radiation characteristics and the flight heritage of a traditional QML product line, but with optimized testing and reduced paperwork and a lower price point. The second approach is the ‘COTS to RT’ concept, which takes commercial or automotive products and provides additional screening and radiation testing to provide assurance on the suitability of the product for deployment in space.”
With the military, however, it’s never a one-size-fits-all approach. It always comes down to requirements and it’s a fact that those requirements – component, system, or platform – are all determined by the mission.
“Rad-hard product costs are driven by material costs as rad-hard components are often 500 to over 1,000 times more expensive than COTS components. The key to leveraging COTS components for space is to understand the true component requirements, why the engineers and procurement officers are buying this part,” Campanini explains. “They help us tailor the certification flows to a COTS level. Figuring out what you need and don’t need, understanding the true requirements, enables designs with next-level mitigation schemes to allow the use of components with no reduction in reliability.” (Figure 3.)
[Figure 3 | Pictured is the Micropac FMC card – high-rel board design.]
Open standards
Open standards and architectures are also a strategy for reducing costs and leveraging commercial technology for military systems.
“SpaceVPX and other standards have been seen across many military space customers,” Campanini says. “Micropac is advancing a Common Device Architecture (CDA) approach to standardization.
“The significant growth in small-sat applications is directly fueled by open standards,” he continues. “The very standardized CubeSat (available as catalog items) to the larger small sats using standard elements such as VPX cards and off-the-shelf building blocks (batteries, processor cards, etc.) within custom chassis is gaining in popularity. Short(er) lead times and ease of development is driving this approach.” (For more on SpaceVPX see the article on page 12.)
Standards are also being developed and discussed for packaging of components. “We are involved in the Space Power Consortium (spacepower.org), which looks to bring commercial standards to power systems for space exploration,” Quiroz says. “There is also a standard being developed around plastic packaging for space components. This is happening inside JEDEC [standards body]. While there is a standard process around traditional ceramic flow, with military specifications that must be met, there is not one for a plastic flow. As demand for plastic packaged devices increases a standard will be necessary to ensure consistent performance. I think we are at least a year away from a formal announcement regarding the standard.”
AI innovation in space systems
Open architectures and commercial technology also drive innovation in artificial intelligence (AI) and machine learning (ML), now being used in military systems. Suppliers are seeing increased requirements for AI solutions in space systems.
“There are a few companies coming up with AI-based solutions for imaging or other sensor applications in space systems,” Quiroz says. “Defense funding is driving some of this.”
Many initial applications for AI in space are geared toward imaging and other sensor applications.
“There are many reasons why AI is interesting to developers of space systems. An example often quoted is cloud detection,” O’Neill says. “In an Earth-observation system which seeks to capture images of objects on the Earth’s surface, images of the tops of clouds obscuring the ground or sea beneath are of no use. An AI system that can recognize images as cloud tops and discard them conserves storage capacity and downlink bandwidth. There are many other examples where AI can be used to conserve resources, or to make autonomous decisions on-orbit, removing ground-based humans from the decision loop, speeding response times for autonomous or robotic missions, speeding the acquisition of scientific data, or perhaps even enabling a rapid response during a national-security mission.”
Microchip has introduced the VectorBlox AI/ML software development kit and IP for use in its FPGAs for image-processing applications, O’Neill notes. It saves as much as 70% power when compared to equivalent SRAM [static random-access memory] FPGAs. The ability to perform intense AI applications while generating significantly less heat than competing solutions provides a significant advantage for space designers, he adds.