Modular strategies for power conversion in UASs address SWaP concerns and increased electrification
StoryMarch 07, 2022
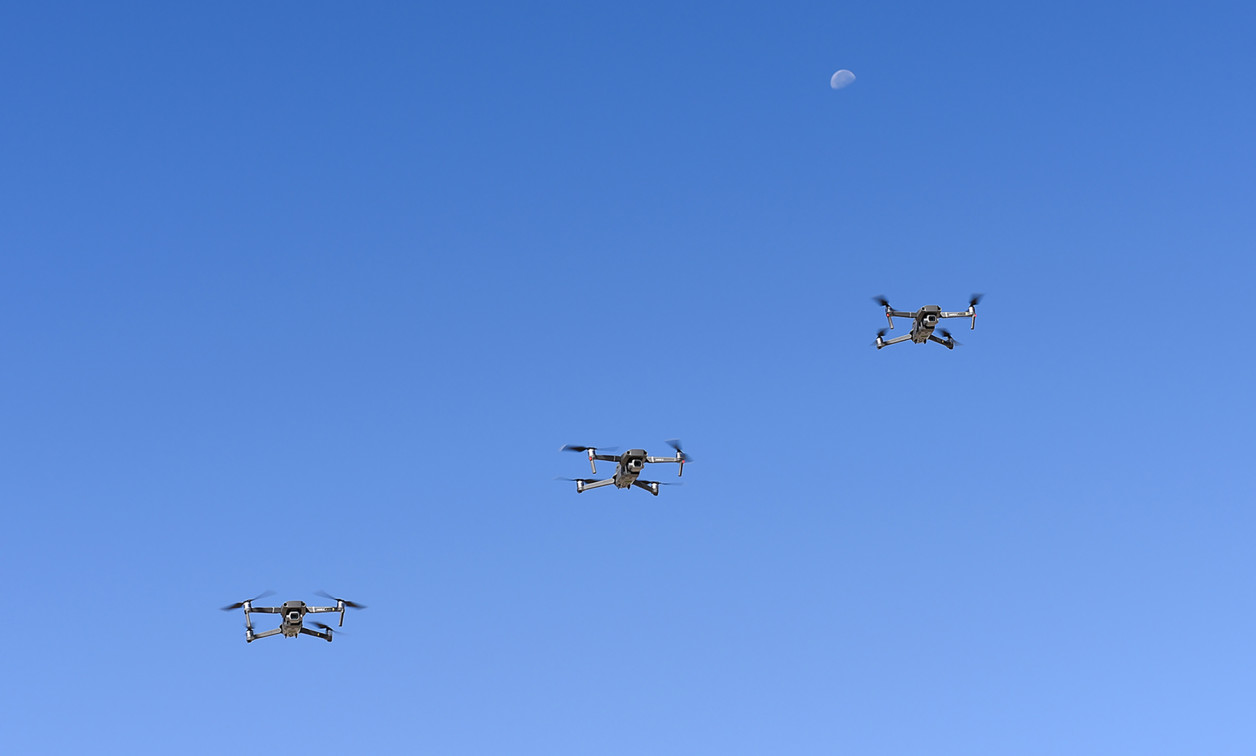
Electrical power onboard aircraft is traditionally generated from some type of engine and AC generator set. AC power is distributed and then converted to DC at or near the point of load, as every electronic system requires DC power. Increasingly, DC power distribution strategies are taking the lead in power-system design, especially for applications – like unmanned aerial systems (UASs) – where size, weight, and power (SWaP) concerns are paramount. Modular DC-DC options enable smart voltage trade-offs, flexible distribution architectures, and the ability to scale for reuse in various applications across aircraft used in military and civil arenas.
Urban air mobility is poised to transform aviation: This reshaping of the industry is moving much more quickly with the support of the U.S. armed forces. Once considered science fiction, carrying people via small electric flying vehicles is a near-future reality. The transportation of people, medicine, and supplies in urban applications proves the concept and value of electrified aircraft. This promise extends to transporting troops, resupplying support and equipment, search and rescue, securing base operations, moving cargo, and more – meaning that unmanned aerial systems (UASs) can potentially reduce or replace manned helicopter missions into dangerous scenarios worldwide.
DC power technologies are at the heart of many urban air mobility systems in development. These airframes, powered by batteries storing DC power, eliminate the demand for AC-DC power conversion at point of load. It’s an important shift in power-system design, enabling consideration of efficient, higher-voltage DC distribution systems that are simultaneously compatible with energy storage (batteries) and load requirements.
Meeting SWaP-C and DC power distribution needs
While traditional aircraft incorporate gas turbines driving auxiliary power units that are naturally AC, the required AC-DC conversion and distribution strategies may inherently increase the number of power electronics onboard. This design approach is in direct opposition to military design ideals of size, weight, power, and cost (SWaP-C) – a problem made more complex by the ever-increasing amount of electrical power required onboard aircraft. Power needs are anticipated to extend the SWAP-C challenge, continually growing in step with more sophisticated cockpit avionics and more electrically actuated systems.
When power is distributed as DC, voltage conversion and power conditioning is still necessary, varying based on how and where the power is to be used onboard the aircraft. Should the design deliver power, stepping it up or down at the device? Or is it smarter and more efficient to convert power levels before distribution to individual devices or applications? Both design strategies have value, and ideal design choices must reflect the systems involved, aircraft type and purpose, reliability, robustness, scalability, life cycle, and more. Building-block strategies demonstrate great potential in this type of power system design – capitalizing on proven designs and minimizing development timelines. It’s a competitive approach that protect SWaP-C ideals and keeps manufacturers focused on the next generation of aircraft design.
DC power distribution strategies
The power needs within a specific area of an aircraft, for example the 28 volts commonly used in cockpit avionics, could be handled with only power conditioning from a local battery source. Conversely, the necessary 28 VDC can be converted centrally and distributed as systems require. This design is best suited to smaller, less complex architectures, as cabling weight can increase when power is widely distributed to a spectrum of onboard devices. Modern, flexible distribution architecture can also provide a layer of redundancy and graceful performance degradation to improve safety and, in the context of military platforms, increase survivability.
A more strategic design might feature increased voltage as a trade-off to reduce cabling. By designing a primary distribution at 540 volts, supported by a localized secondary distribution at 28 volts, step-down is not needed at every individual load; the localized 28 volt network is instead designed to support multiple devices with a single conversion. Such a design is also beneficial for electronics performing in more isolated areas of the aircraft, such as a heating system or controls on the wing. Concerns over cabling weight increase with cabling distances, addressed with power distributed in a single higher-voltage option and then stepped to its required voltage locally adjacent to the device. This design strategy becomes more complex with systems that demand secondary loads demanding multiple voltages, such as 28/5/3 volts.
Modular options extend flexibility
In response to these evolving power needs, along with the demand for faster time to market, power solutions are more readily available as modular, building-block components that consider both performance and scalability. Two distinct levels of modularity apply, the first of which features the device itself. Defining design models parametrically eliminates the time and resources required for ground-up development, including a complete model and analysis of each design. These can be easily tailored and integrated into custom designs across the full spectrum of secondary power needs, whether the application requires a 100 watt low-power control unit or entails a heavier end load such as 6,000 watts.
Custom design resources can be further minimized when a single device is developed to meet a superset of requirements. In this case, system developers must pay close attention to overall device efficiency; a family of building blocks can help alleviate efficiency concerns, enabling interchangeability across various points in the design range. Each will deliver its own defined performance window, driving the need for scaling up or down to achieve maximum efficiency. Performance thrives, time to market is fast, and proven engineering is repurposed wisely.
The end unit itself defines the second level of modularity. Consider that a 2 kW converter can be designed for more than a single use, for example, applied to the power distribution strategy of a 4 kW or 6 kW application. This taps into proven technology in a modular design, meeting custom power levels and aligning with all-electric aircraft power redundancy requirements. Using this approach, system design could feature five individual, but coordinated, 2 kW converters to nominally deliver 10 kW. Flexibility and redundancy are engineered into the design, along with automatic power routing, so that the loss of a single converter doesn’t affect overall system integrity. If an unlikely failure occurs, the remaining components compensate to keep the aircraft safe and operational – much like the multiple engines onboard traditional aircraft. Such designs are also generally lighter than traditional “A lane/B lane” duplication. Historically, power-control systems tend to perform in isolation, yet today’s engineering advancements highlight this as an important shift and ideal design path for electric aircraft power.
Increased electrification and agility in defense scenarios
Advancements from the massive global investment in energy storage technology – fuel cells and batteries – are transforming aviation. Military operations are hazardous by nature; however, air operations may be considered safer than land-transport options exposed to improvised explosive devices (IEDs) or other ground attacks. Even more importantly, technology relationships add value to both sides of the equation. The defense industry benefits from commercial innovation, in step with its long-held goal of procuring commercial technology with military value. At the same time, its own extensive resources such as flight-safety testing and certification can help reduce risk and accelerate technology adoption, building up a global market for affordable urban air mobility technology. Flexible distribution schemes and modular power electronics can be used to design highly robust solutions with excellent survivability.
Julian Thomas is Engineering Director, Aerospace and Defense, at TT Electronics. Julian has over 30 years’ experience supporting the aerospace & defense and space markets specialising in thermal management, materials engineering, and electronics engineering and design for increased power density requirements and harsh environment applications. Readers can connect with Julian at julian.thomas@ttelectronics.com.
TT Electronics https://www.ttelectronics.com/