Hot problems: Designing a thermally optimal data-acquisition unit
StoryAugust 13, 2020
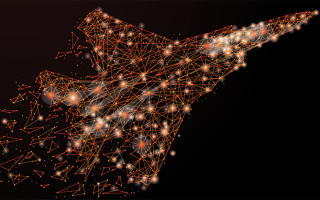
By Pat Quinn
Flight test instrumentation (FTI) data-acquisition systems (DASs) use data-acquisition units (DAUs) distributed throughout an aircraft, often in tight spaces, which drives demand for smaller chassis. In parallel, the demand for higher DAU performance is on the rise, resulting in more heat-generating components packed tighter together. Since chassis act as a heat sink for the components inside, a smaller chassis provides less metal to drawing heat away from the components.
In order to properly understand the accuracy of a flight test instrumentation (FTI) measurement, the designer needs to know the measurement accuracy for the temperature of the electronics. Electronics expected to perform in more extreme temperatures will be tested, and certified, over a range (typically -40 °C to 85 °C for rugged aerospace electronics). It’s therefore good practice to check the details of accuracy claims by manufacturers because of the possibility that a best-case specification has been cited that may not match performance in realistic conditions.
Heat also ages hardware. Even if systems are operating to a target specification, if they are running hot, their effective lifetime is reduced. An approximate estimate is that a 10 °C increase halves the lifetime of the component (via Arrhenius equation, a formula for the temperature dependence of reaction rates). In reality, while system failure is more complex than the lifetime of components, it is still important, especially when high temperatures are involved. Effective life should be considered, since a low initial data-acquisition unit (DAU) cost may end up more expensive in the long run if the item requires more frequent replacement.
Increasing heat in flight test instrumentation
Since the DAU chassis acts as a heat sink for the components inside, a smaller chassis means less metal to draw the heat away from the components. This situation is compounded by the trend for higher channel densities. What’s more, increases in throughput and channel count require more power to be drawn into a chassis, generating even more heat. Today, many aircraft use composite materials in the airframe, which are significantly less thermally conductive than metal. For example, the thermal conductivity (k) of fiberglass is ~ 0.04 vs. 236 for aluminum (in SI units of watts per meter-kelvin (W·m−1·K−1) at 0 °C). This means a DAU is unable to use conduction cooling as effectively as before; the lower the k value, the poorer the material is at conducting heat. (Table 1.)
[Table 1 | Thermal conductivity of some common materials used in DAUs and aircraft.]
Dissipating heat in FTI systems
Which heat dissipation methods are used in existing FTI systems generally depends on the age of the installation and the size of the aircraft. For example, older DAUs tend to be relatively large and bolted to metal in an aircraft made primarily of metal, which enables good conduction cooling from the DAU and – assuming a good design – from the components in the DAU to a larger metal chassis. There may also be some open space that enables decent convection cooling. (Figure 1.)
[Figure 1 | DAU heat dissipation is typically accomplished using conduction, convection, and radiation.]
Some DAUs are placed in racks that use passive or forced air cooling (usually only an option in large aircraft). These benefit from good convection cooling as well as some conduction in the rack. The trend towards smaller chassis located in tight spaces, sometimes on composite structures, makes it increasingly difficult to dissipate heat from the DAU components. (Figure 2.) This reality makes it critical to properly understand and implement good thermal-design decisions in DAUs to meet current and future FTI DAU requirements.
[Figure 2 | Heat sinks are effective for removing heat but are often impractical for ultracompact systems due to their size.]
Optimal thermal design
Generally, DAU components are mounted on printed circuit boards (PCBs). Several thermal-design decisions should be followed for optimal operation: At a high level, it is important to ensure that heat can be quickly transferred away from components and that heat isn’t concentrated in any one spot.
Flight test DAUs typically consist of a chassis and modules. It is important that there is a good method of moving the heat away from the modules in order to help the chassis move heat away from components. In this way, the chassis itself acts as a heat sink. How effective this function is depends on a few factors such as how the chassis is constructed, the quality of the thermal contact between the chassis and its modules, and how power is used in the chassis. There are generally two methods of constructing chassis, either using a solid chassis and separate modules or using a “slice-of-bread” design.
A solid chassis has slots in which modules can be inserted, similar to inserting disk drives into a recorder. In the slice-of-bread method there is no separate chassis. Instead, the chassis is constructed out of the acquisition cards themselves, connecting several acquisition cards together, and securing them via a locking mechanism.
A solid chassis has the advantage of being a large piece of contiguous metal that enables heat to quickly flow from a hotter region to a cooler one. A disadvantage of the solid chassis is that insertion and removal of modules makes it difficult to create a perfect thermal contact between the modules and the chassis. A slice-of-bread approach has the advantage of being able to very tightly connect the PCB to the chassis, as the chassis is part of the module. The disadvantage of this approach is that it is difficult to create a fully conductive seal between the modules.
Whichever chassis design is chosen, it is likely constructed from metal, typically aluminum or steel. Steel is cheaper and stronger than aluminum, so chassis walls can be a little thinner and material costs will be lower. However, aluminum appears a better choice as it is a significantly better heat conductor (k = 236 versus 15) and is lighter and easier to mill. In practice, there is little cost saving for a finished steel chassis, as any size difference is trivial and the superior thermal properties of aluminum help move heat from the chassis into the surrounding environment.
There are also design decisions that can help a DAU better use power. It is common for DAUs to supply multiple voltages to modules as there are different voltage requirements for module operation, sensor excitation, and so on. To avoid data loss in the event of a black or brown out, power holdup capacitors are used in the power supply. Reducing power supply voltages lowers the number of holdup capacitors required. This reduces the power drawn and heat generated, as well as the power supply size. Voltage conversion can instead be performed on the modules.
Whisk the heat away
The Axon DAU is an example of how to design a power-wise and thermally efficient compact data-acquisition unit. A dual side-rail system is used to closely couple the Axon module to the chassis, while still damage-free module removal. A solid chassis, milled from a single block of aluminum, minimizes any gaps that could lead to hot spots; aluminum’s excellent thermal properties ensure quick heat transfer away from the modules, without requiring more expensive or exotic materials. The chassis acts like a heat sink attached to a microprocessor in a PC. Within the chassis, use of a single voltage rail allows a single holdup capacitor to be used. This draws less power, ensuring the DAU can effectively deal with common supply voltage variances or interruptions. (Figure 3.)
[Figure 3 | This design maximizes thermal dissipation at each stage to keep the components cool enough without external heat sinks or forced air.]
For the module, a large ground plane is used to help draw heat away into the module side rails. For a traditional DAU, there is a limit on how small a DAU can be shrunk to house a single module; the chassis must also house a transmitter card (to send data via Ethernet, IRIG 106 chapter 4 PCM, or IRIG-106 chapter 7) and a power supply.
Axon DAU backplanes use a serial point-to-point link for each module that provides data and power lines, which enables a unique solution for particularly tight or hot locations (such as wings or engine nacelles): the Axonite chassis, which houses a single module. Axonite is connected to an Axon chassis using a single wire via the serial backplane. To the Axon chassis, the module appears to be internally integrated, but can be located up to 10 meters away in a dedicated Axonite chassis. Axon DAUs integrate I2C temperature sensors for thermal monitoring into all parts, including top blocks, modules, power-supply units, etc. The sensors provide insight into how hot elements get, which is useful for troubleshooting and data-integrity assurance.
Patrick Quinn is product line manager for Aerospace Instrumentation at Curtiss-Wright Defense Solutions. He holds an Electrical & Electronic Engineering degree from the Dublin Institute of Technology.
Curtiss-Wright Defense Solutions
www.curtisswrightds.com