System upgradability: key for U.S. Army’s next-gen vehicle fleet
StorySeptember 11, 2024
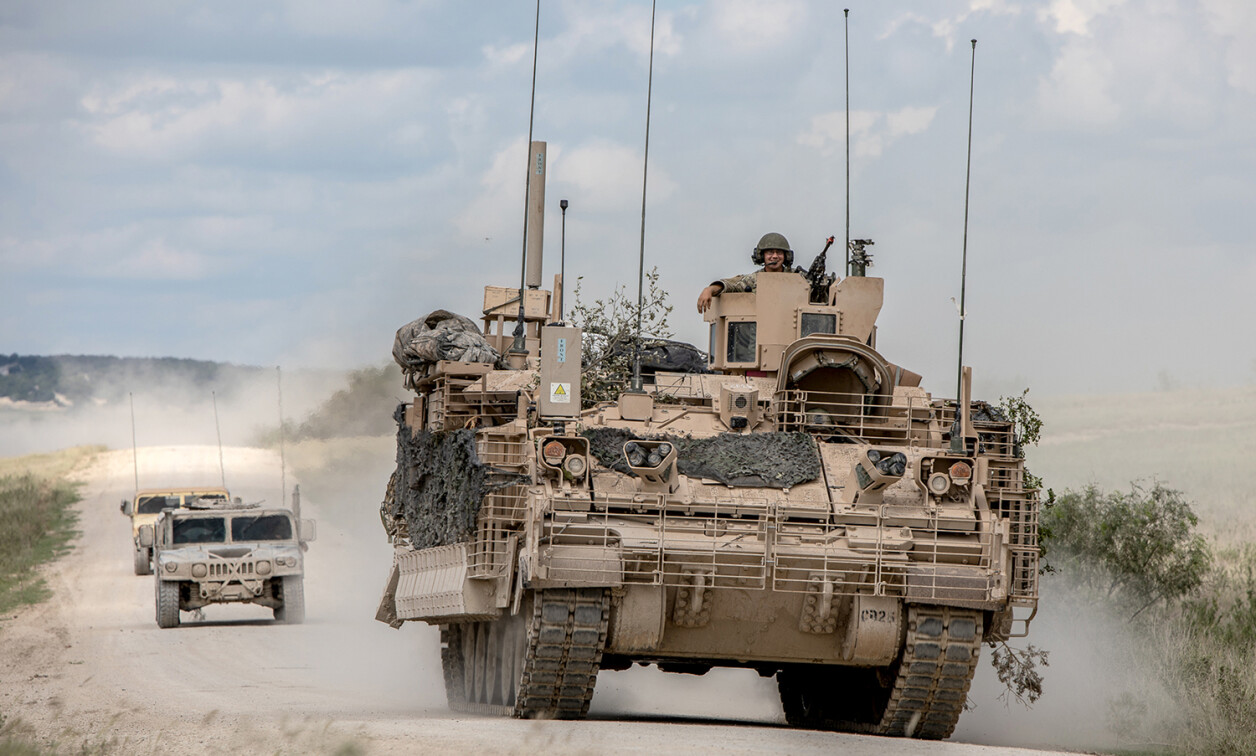
The U.S. Army is in a period of consequential modernization for its ground vehicle fleet. The vehicles that are set to be introduced over the remainder of this decade are likely to be in service for many decades to come, and will come up against a variety of threats in a range of different theatres. The need to easily upgrade electronic systems, spiral develop capabilities, and adhere to open standards, will be crucial for maintaining operational relevancy.
The global security environment is more dangerous than at any other time in a generation. Peer adversaries, including Russia and China, are now the pacing threats that are likely to challenge the U.S. and the wider global order for many years to come. The war in Ukraine in particular has demonstrated not only how dangerous Russia is, but also how the rapid pace of technology is transforming how nations fight.
Within this context, the U.S. Army is at a critical juncture and the decisions it makes today on modernizing its capabilities will have a significant impact on how it fights tomorrow. The U.S. Army is currently going through one of its biggest modernization periods since the Cold War, introducing a range of new capabilities that will provide U.S. soldiers with enhanced lethality, protection and mobility.
Critical to this modernization will be a range of new crewed ground vehicles, which includes the Armored Multi-Purpose Vehicle (AMPV), the XM30 Mechanized Infantry Combat Vehicle (formerly the Optionally Manned Fighting Vehicle), and the M10 Booker Mobile Protected Firepower (MPF). (Figure 1.)
[Figure 1 ǀ The U.S. Army Armored Multi-Purpose Vehicle (AMPV) is the replacement for the M113 family of vehicles, which comprises approximately 30% of tracked vehicles within the Armored Brigade Combat Teams, or ABCTs. U.S. Army photo.]
Additionally, the U.S. Army plans to acquire robotic vehicles that will augment crewed vehicles on the battlefield. The platforms – known as Robotic Combat Vehicles (RCVs) – act as autonomous battlefield surrogates that can increase mass and remove humans from dull, dirty, and dangerous missions. Previously segmented into Light, Medium, and Heavy variants, the U.S. Army’s RCV is now concentrating efforts around a single weight class.
Operating at the technological edge
These new crewed and uncrewed vehicles will be the most advanced combat vehicles ever developed and provide a significant capability uplift compared with legacy vehicles, some of which have been in service since the 1980s.
Fundamental to this capability uplift will be the significant increase in computing power that will underpin each of the new vehicles’ electronic systems.
The requirement for computing capabilities on ground vehicles has seen constant, if not exponential, growth as vehicles have added more onboard systems. No longer are ground vehicles simply armor, guns, and drive systems, but instead are carriers of complex, integrated electronic systems that deliver a combined effect for the mission they need to carry out. (Figure 2.)
[Figure 2 ǀ A U.S. Army Robotic Combat Vehicle – which integrated weapons systems, high-speed cameras, and data-collection systems – is trialed to test out systems operations and quality. Photo: U.S. Army/Angelique N. Smythe.]
These modern vetronics systems are critical for areas such as real-time data processing, communications, navigation, and sensor-weapon control. As vehicle computers become more advanced, so too are the capabilities they enable, which include system health monitoring and predictive maintenance, data fusion, as well as decision support through artificial intelligence (AI)-powered edge processing.
The demand for optionally-manned capabilities and robotic “wingmen” such as the RCV will only push the requirement for advanced computing capabilities further, requiring significant edge compute power – leveraging the latest commercial AI processors – that can handle AI and machine learning (ML) algorithms for autonomous operations.
The ability to interoperate as a mixed crewed-uncrewed formation, sharing data from multiple sources across the echelons of a networked battlefield, will also drive the demand for systems that can collaborate using networks such as Combined Joint All-Domain Command and Control (CJADC2).
It is these advanced vetronics and network capabilities that will ultimately give U.S. warfighters the edge on the future battlefield, potentially even more so than the thickness of armor or the lethality of a gun.
Common standards and SWaP will be critical
It’s a common engineering challenge that as more electronic components are integrated into a system, complexity grows and integration challenges increase. That’s no different for armored vehicles, and legacy vehicles in particular have struggled to integrate additional electronics systems thanks to closed architectures and proprietary interfaces.
A vehicle’s electronics can consist of many different boxes or systems that are designed for specific functions, whether that is core processing units/mission computers, sensor systems, communications, control systems, and much more.
Traditionally, many electronics systems installed on combat vehicles have had proprietary interfaces that have limited the upgradability of onboard systems, thus increasing the cost of updating as integration challenges have been significant. Life cycle costs in particular have snowballed.
Moreover, vendor lock – or a situation in which a customer using a product or service cannot easily transition to a competitor’s product or service – has added layers of cost and complexity in areas such as vehicle development and upgrade programs.
In the threat environment the U.S. and its allies face, it is no longer feasible to wait years to upgrade platforms and spend billions of dollars for changes that often become outdated as soon as they are fielded. The rapid pace of technological change will require vetronics to be upgraded at an equally rapid pace, ensuring that U.S. forces stay ahead of the threat – which, as has been seen in Ukraine, can change on a daily basis.
Thankfully, the U.S. Army is moving in the direction of open architectures, which will be critical to this effort. This forward motion includes the modular open systems approach (MOSA), which is the U.S. Department of Defense (DoD) “preferred method of implementation of open systems,” and is now mandated for all major defense-acquisition programs.
Additional open architecture frameworks such as the C5ISR/EW Modular Open Suite of Standards (CMOSS) – which fits under the MOSA umbrella – will also ease integration and remove the need for multiple discrete boxes that address singular capabilities, replacing them instead with systems that handle multimission compute capabilities.
At the same time, designers and integrators face the ongoing requirement to optimize, and often reduce, SWaP [size, weight, and power] requirements, even as computers become more powerful. Armored vehicles, and especially smaller robotic vehicles, are extremely limited when it comes to space and power. Excess weight on such vehicles is a fundamental issue that can compromise other areas such as mobility.
Computer manufacturers such as Systel are constantly optimizing their designs and addressing the demand for smaller SWaP, all while maintaining the ever-more-powerful compute capabilities required for modern military operations. (Figure 3.)
[Figure 3 ǀ Sparrow-Strike is Systel’s ultra-small-form-factor military-specification rugged edge mission computer – designed using a modular open systems approach (MOSA) – aimed at use in emerging autonomous and uncrewed missions.]
Computers must not only be open, but future-proofed
The computers that underpin modern vehicle systems will have to be easily upgradable and modular, allowing end users to configure and update them for the latest threat on the battlefield.
It is not enough just to be compliant with various open standards: Computers will also have to be designed for ongoing spiral development – another term for a systematic and iterative approach to software development – and rapid technology insertions that do not require full box replacements.
This is a critical area for developers: The architectural approach to rugged computer design enables customers to upgrade and customize chosen solutions, all while retaining the same form factor and interfaces, as well as being MOSA/CMOSS-compliant.
Under this approach, the computers also continue to meet strict military standards, such as MIL-STD-810 environmental standards and MIL-STD-461G electromagnetic compatibility standards.
The ability to easily upgrade systems will have a major effect on life cycle costs and future-proofing, enabling end users to update vetronics components rapidly without the need to fundamentally change the vehicle’s electronic or physical architecture, including mounting points, interfaces, or vehicle wiring.
This approach will be particularly important as AI is deployed closer to the edge, whether on crewed or uncrewed vehicles. AI at the edge requires huge amounts of processing capability, a situation that is constantly evolving, particularly as the commercial sector brings new AI and ML processors to market on a regular basis. Staying at the forefront of AI capabilities will require a steady cadence of processing upgrades to remain operationally relevant.
Brian Russell heads the product department at Systel, focused on creating and leading a product vision and strategy. He is a 22-year retired U.S. Army aviator, where he served as a CH/MH-47 Chinook pilot in both the conventional Army and Special Operations communities.
Systel • https://systelusa.com/