Parts, materials, and processes (PMP) and radiation hardening for space and defense systems
StoryJune 15, 2021
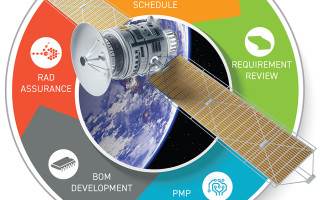
By Barry A. Posey and Bryan F. Hughes
Using cutting-edge microcircuits in space and defense systems with natural space-radiation requirements, while risky, also comes with potential rewards. There is a path for insertion of these cutting-edge solutions into space and defense systems: The use of a parts, materials, and process (PMP) program.
The performance and capability demands on electronic space systems for both the defense and commercial arenas continue to increase. Such systems – designed and manufactured for military, space, and launch vehicle applications – must exhibit the highest quality and reliability standards. Therefore, all hardware and processes, including design guidelines and fabrication procedures, must be managed and controlled. Controlling these factors must be the primary objective of an organization’s parts, materials, and processes (PMP) program.
Requirements review
An environmental requirements document may include thermal, pressure, acceleration design, acoustic, random vibration, shock, humidity, radiation, atomic oxygen, thermal vacuum, and electromagnetic interference/electromagnetic compatibility environments. Component and radiation-effects engineers will be assigned by the Mission Assurance Manager to develop plans to ensure compliance to these requirements.
These engineers examine system-specific design guidelines and requirements pertaining to part-qualification ratings, part and subsystem parameter derating requirements, system interface requirements, etc. to ensure compliance; they also develop procedures for controlling and implementing material and part waivers and deviations as required via inclusion in the PMP program. Also included would be procedures for reviewing and approving engineering drawings and engineering change orders (ECOs) for applicable parts, materials, or manufacturing impacts.
PMP program
A detailed PMP program ensures the selection, application, and procurement of standardized electrical and mechanical parts, materials, and processes that are controlled to meet contractual requirements, improve system quality and reliability, and reduce program costs. The key to a successful PMP program really is documentation. Program requirements must be understood, parts and materials selection criteria must be specified, and manufacturing processes must be documented and approved. (Figure 1.)
[Figure 1 | The radiation hardening assurance process is a cycle with five key areas. Scientic graphic.]
A typical PMP program focuses on the following areas:
- Program-specific design guidelines
- Electrical and mechanical approved-parts lists
- Material identification/usage list
- Specialized electrical and mechanical fabrication processes
Each of these areas contains numerous lower-tier functions which must be controlled and documented. Because of the complexity and importance of these efforts, many organizations have a PMP group separate from the engineering or quality core groups. These PMP groups are typically staffed by electrical-component engineers, mechanical engineers, chemical engineers, and process engineers. The Department of Defense Handbook MIL-HDBK-1547A, “Electronic Parts, Materials, and Processes for Space and Launch Vehicles,” offers guidelines for implementing and maintaining a PMP program.
Bill of materials (BOM) development
One of the key PMP program functions involves establishing requirements for the development and maintenance of an approved electrical-parts list and an approved mechanical-parts list. These approved-parts lists (along with the material identification/usage list discussed below) are the basis of a successful PMP program. The requirements set forth for the selection, qualification, and approval of electrical and mechanical parts for inclusion in the approved-parts lists directly affect the ability of the end system to meet all contractual requirements. This process typically involves selecting industry-standard component specifications for electrical and mechanical parts (i.e., military specifications) or creating unique specification control drawings (SCDs) for each part type used in the final system. Control documentation must also be created to provide guidelines for performing the required qualification and lot acceptance tests necessary for each part type. Requested deviations from these approved lists must be thoroughly researched, documented, and approved to ensure that all component and system level specification requirements are met. These deviations are typically requested and approved using a controlled Non-Standard Parts Approval Request (NSPAR) or a waiver process.
Similar to an approved-parts list, the material identification/usage list is a menu of materials qualified and approved for specific applications. Typically, this list will also document approved material finishes for specific environments and applications and will address any compatibility issues with other materials or finishes in the final system.
The PMP program must provide for the documentation, control, and approval of any unique or specialized electrical and mechanical fabrication processes used to manufacture all circuits, components, and subsystems in the end system. This method typically involves identifying the accepted industry standards or military specifications that cover processes such as machining and metalwork, circuit-board fabrication, component soldering operations, electrical wiring, and the like, and certifying that all work performed meets these standards and specifications.
Radiation assurance
Radiation-hardness assurance tasks include the identification of the radiation-sensitive parts in the BOM, which requires research to obtain valid data from radiation reports. The radiation analysis will apply valid statistical methods to determine confidence level for the total ionizing dose (TID) and displacement damage (DD) tolerance of the part and assess the likelihood of single-event effects (SEE) to determine the probability of success P(s) with data using error-bars in the analysis.
Shielding analysis can be performed using radiation-transport tools such as NOVICE, FASTRAD, GEANT4, and MCNP to model radiation-transport methods and effects. These modeling tools enable the design and 3D modeling of spacecraft and discrete space system components offering multiple views, including cross-sections, blueprints, cutaways, and blend operations, thereby enabling skilled radiation engineers to quickly perform complete analysis of radiation effects.
After performing shielding analysis, it may be necessary to perform radiation lot acceptance testing (RLAT) or characterization of specific electronic components depending on the criticality of the circuit. Test planning is most critical and may consume up to one-third of the test budget. It is most important to follow established radiation test methodologies along with detailed and vetted test plans.
Procurement of electronic components that will meet cost, schedule, and performance requirements is the goal. In the event that an established part number cannot be procured, the component engineer may have to create a source control document (SCD) that provides part descriptions and added screening tests needed.
Example: Program with a TID specification of 60 krad (Si), and an assumed 100 mil of shielding was established. A large number of 100 krad (Si) TID rated DC-DC converters were selected by circuit designers to meet program specification. However, the number of converters, the cost per converter, and lead times kept mounting and became prohibitive. Radiation engineers completed shielding analysis that determined the TID exposure in the volume of interest was 16 krad (Si) over all converters for mission life. By procuring existing converters with less TID tolerance, the program saved 75% of the cost of a higher-TID-tolerant converter while reducing device lead times.
In short: The benefit of a robust component engineering and radiation hardness assurance approach will lead to electronic components that meet reliability, quality, and radiation tolerance requirements while reducing program risk, cost, and schedule.
Barry A. Posey, director of component engineering at Scientic, has led numerous component and radiation-assurance engineering programs over his career. Barry received his Bachelor of Science degree in electrical engineering technology from Alabama A&M University. He may be reached at barry.posey@scientic.com.
Bryan F. Hughes is VP of operations and senior scientist at Scientic. He has 25 years’ experience in experimental and applied physics associated with the impact of radiation effects on semiconductors. Bryan received his Master of Science in physics from the University of North Texas. He may be reached at bryan.hughes@scientic.com.
Scientic • https://www.scientic.com/