Software implements Physics of Failure Analysis
ProductApril 18, 2012
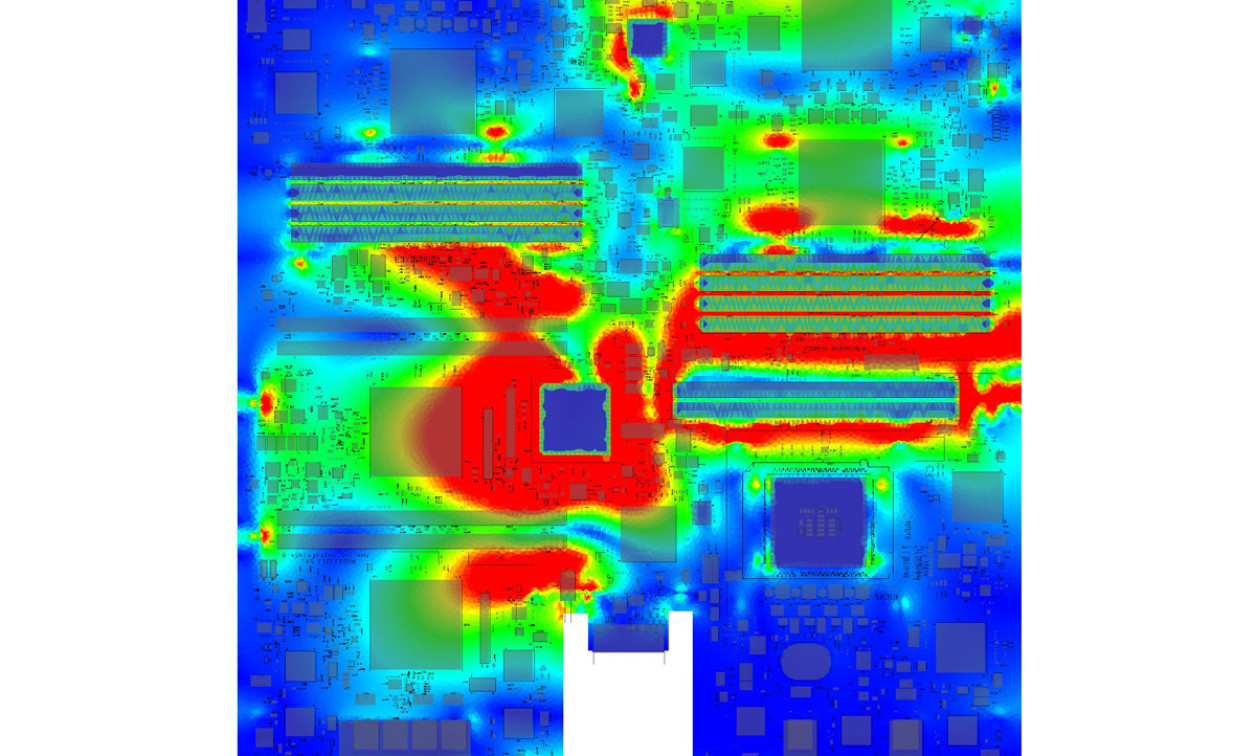
Physics of Failure Analysis is a topic that is critical to rapidly and cost-effectively delivering safe, highly reliable systems into military customers' hands.
Physics of Failure Analysis is a topic that is critical to rapidly and cost-effectively delivering safe, highly reliable systems into military customers’ hands. One company focusing on this paradigm is DfR Solutions, apparently, with its Sherlock Automated Design Analysis Tool software. Sherlock uses Physics of Failure Analysis to help designers spot the possible points of failure early in the design process, thereby eliminating the innate inefficiency of the build-test-fix cycle.
Sherlock works in three phases: 1) Data input – the same files that the user company would send to a manufacturer for board assembly can be used after data is easily imported into Sherlock. 2) Analysis – A holistic analysis is rendered, taking into account things such as time to failure, part failure, shock and vibe, and thermal, specifically: virtual thermal cycling, solder joint fatigue, virtual shock, Conductive Anodic Filaments (CAFs), virtual vibration, and Plated Through Hole (PTH) fatigue. 3) Report and recommend – Results are provided in several formats such as overlays, life curves, histograms, or in a tabular output. Reports are rendered in only a few minutes.