NASA tests 3-D printed component on RS-25 engine for SLS
NewsDecember 15, 2017
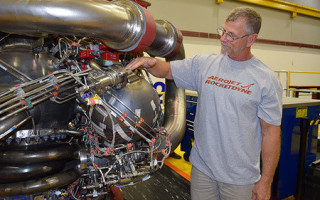
NASA/JOHN C. STENNIS SPACE CENTER, Miss. NASA and Aerojet Rocketdyne (a subsidiary of Aerojet Rocketdyne Holdings, Inc.) completed hot-fire testing of an RS-25 rocket engine containing its largest additively manufactured component to date. Additive manufacturing is commonly referred to as 3-D printing.
During the 400-second test at Stennis Space Center, NASA and Aerojet Rocketdyne evaluated the performance of a 3-D printed vibration-dampening device -- known as a pogo accumulator assembly -- which was manufactured at Aerojet Rocketdyne's facility in Los Angeles, California. The pogo accumulator assembly part acts as a shock absorber to dampen oscillations caused by propellants as they flow between the vehicle and the engine; without dampening these oscillations the flight would be less safe.
The additively manufactured pogo accumulator assembly consists of two components, the pogo accumulator and pogo-z baffle, both of which were made using a 3-D printing technique called selective laser melting; this technique uses lasers to fuse metal powder into a pattern by adding layer upon layer of material to produce the part. On the pogo accumulator part alone, the 3-D manufacturing technique reduced the number of welds by 78 percent.
NASA and Aerojet Rocketdyne installed and are testing the 3-D-printed components on a development engine that is used to test new technologies that are being incorporated into the RS-25 as part of the SLS program, which is NASA's in-process Space Launch System (SLS) heavy-lift rocket. The SLS, designed to send astronauts and cargo to explore the moon and other deep-space destinations (tentative start date late 2019), uses four Aerojet Rocketdyne-built RS-25 engines.