GUEST BLOG: Military power conversion: the value of strategic customization
BlogSeptember 09, 2020
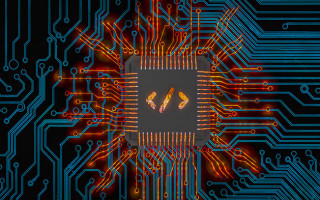
Customization of power supplies provides a distinct yet obvious advantage to the design engineer to meet performance specifications. Whether it be saving a card slot in a chassis, reducing the number of power supplies required, or addressing a unique EMC requirement, customization can reduce total system cost and technical risk to put increased capabilities rapidly into the hands of the warfighter. It also provides a pathway to support the Department of Defense’s (DoD’s) open-architecture standards. When approached strategically, customization can be a cost-effective and low-risk approach to address requirements.
Read Part One of Mike’s take on custom parts at https://bit.ly/32F5Hde.
The benefits of defined design standards are numerous, especially in support of open-architecture system designs that shoot for reducing life cycle costs and development time. However, the ability to deviate from design standards can be a priceless aid for engineers in order to meet the unique performance requirements prevalent in military platforms. Let’s look at a few real-world examples of this approach in practice.
Example one: varying output voltage and current
An engineer wants to use a commercial off-the-shelf (COTS) product with its baseline capabilities, but the specification requires specific output voltage and current levels to effectively support its rugged, single-board computer (SBC) and storage cards within the enclosure via custom backplane design. Rather than accepting the suboptimal COTS product and sacrificing the capability or performance of their existing design, the engineer should request to speak with the power-supply manufacturer’s design team. After learning about the target specification, the manufacturer’s design team rapidly implements the necessary changes to support the integration of those peripherals, providing a customized power supply that continues to comply with the vast majority of industry standards. Adjusting the outputs to meet the customer’s unique current and voltage requirements is a low-cost, low-risk, and rapid solution to enable system-level performance.
Leveraging the proven performance of a mature design, this approach allows the engineer to successfully achieve qualification of the system upon first attempt and leverage the unique backplane design. While the COTS product was 90% of the solution, rapid tailoring of the product to the needs of this customer ultimately addresses the unique needs of the warfighter without significant changes to system, cost, or delivery timeline. The intent of the U.S. Department of Defense (DoD) Modular Open Systems Approach (MOSA) program can be addressed with architectures, such as Sensor Open Systems Architecture (SOSA)-aligned system designs.
To further this point, modifying the mature design to provide increased voltage and current limits at these three outputs, and deviating from the VITA standard, ensures a second power supply was not required within the enclosure. This approach not only saved the cost of a second power supply, but also saves an open card slot to support integration of future product enhancements and capabilities. This is an excellent example of both how customization need not be considered risky or expensive, and how sticking with the VITA VPX standards to ensure an open architecture at the system level can significantly drive life cycle costs and development time down for the end user component versus system requirements.
Standardization is an industry trend providing positive results for both the cost and schedule of defense programs, large and small. A fine balance between component-level specifications and system-level specifications is a key aspect in any engineering effort. An excellent example of a component-level specification is the VITA 62 VPX standard defining electrical connector parameters, including voltage and current levels. Standards such as MIL-STD-1275 may be applied at either a component level or system level to control 28 VDC electrical power in a military ground platform.
It can be stated that industry appreciates and values standards at both the component and system level. However, it is often necessary to deviate from the standard to meet 100% of both component- and system-level requirements. Every system on the battlefield poses a unique set of challenges, forcing design engineers to make difficult decisions affecting cost, schedule, and risk. Customization to meet open architecture standards can be done in a cost-effective and schedule-driven environment.
Example two: unique mechanical and thermal management challenges
In this example, the engineer’s requirement includes the need to incorporate a redundant AC power connector into a 3U VPX power supply. This factor takes customization of a baseline VPX power supply one step further than our previous example, tailoring both mechanical and thermal design features.
In this instance, a customization effort similarly reduces risk while incorporating important capabilities at a system level. As before, the project starts with the engineer identifying a mature COTS solution that closely matches the specifications they’re looking for, then engaging with the manufacturer’s design team to discuss the unique specifications of their requirement compared to this COTS product. In this example, the mechanical housing can be quickly designed around the board to address the redundant input power requirements (a second connector compliant to MIL-STD-38999) at the system level. Such an approach not only addresses the redundant AC power connector requirement, but also allows for improved thermal management while ensuring the integration of other COTS VPX peripheral cards.
With close communication and collaboration with the manufacturer, it is realistic to complete the above design modifications and rapidly develop and test prototypes within 60 days. At the end of this exercise, a design review provides the engineer with enough confidence and data on the modified VPX power supply to begin design modifications to the enclosure and backplane to accommodate the added connector. Starting from an existing and mature MIL-VPX product that addressed a large percentage of the power supply performance specification was a no-nonsense and schedule-driven decision that enables the engineer to obtain a 100% solution for their requirement.
Considering our earlier example, a VPX form factor SBC required 360 watts of power, exceeding the VITA 62 standard for the VS2 connector contact. While deviating from the VITA electrical standard, the desired 3U mechanical form factor is not changed, ensuring an open architecture system and retention of the benefits of the VPX form factor.
Further, following SOSA-aligned design practices ensures the ability to maximize COTS components within the enclosure – the best of both worlds. At a system level, a standardized chassis and backplane can be maintained, along with use of peripheral devices, reducing total life cycle costs and maximizing the intended nature of standardized enclosure designs. Supporting both component- and system-level requirements is achievable by tailoring the design of standard products, which can be done in an expedited and cost-effective manner, significantly decreasing risk and keeping the project on course with existing delivery and cost projections.
Example three: EMC and standardization
In the ever-evolving world of defense electronics, higher power densities, increasing current and faster switching, and EMC continues to be one of the most challenging endeavors of the system designer. Modern power switches offer significantly higher switching speeds. This means that the rise and fall times for both voltage and current waveforms are much shorter – a root cause of many electromagnetic interference (EMI) issues in switching power supply design.
As such, solutions to address the litany of EMI challenges need to remain agile and creative when it comes to power-supply design. Standardization on the other hand, encourages repeatability and deincentivizes change. To solve EMI issues, customization is a key element in the toolbox of the design engineer, especially in keeping with the DoD’s intent of maintaining an open-architecture approach.
To qualify a power supply, it is tested in cascade with a line impedance stabilization network (LISN) to standardize test results and simulate the run of cables feeding the tested item. Typically, power supplies installed in small platforms are allowed to be tested with low-inductance LISN, so they will not become unstable and oscillate.
However, in scenarios where long cable runs are prevalent, the standard 50 μH must be used. In this example, an engineer identifies a COTS 350 watt DC/DC converter for integration into their airborne application. After engaging with the manufacturer’s design team, the engineer states that the converter must be tested for compliance with MIL-STD-461F when connected to the power line through 50 μH LISNs. The design team modifies the existing COTS product design by integrating a larger bulk capacitance to help support the 50 μH inductance requirement. Again, deviating from the VITA 62 electrical standard to rapidly address a unique EMC requirement, a close partnership with the manufacturer’s design team enables the engineer to identify a schedule-friendly, low-risk solution.
Powering nonstandard loads with standard power supplies
The standard VPX chassis is commonly used by integrators as an enclosure for a wide variety of applications, including radar, electronic warfare, communications, and more. Each application brings its own unique set of performance and operational requirements. In this example, an engineer needs a VPX power supply to feed a radar load, made up of digital circuits (signal conditioner), analog low power circuits (preamplifier), and analog high-power circuits (power amplifier). The form factor and connector are standard VITA 62 and 46, but the output voltages and current limits are completely different, with odd voltage levels, such as 6 VDC for the GPS board, 5.5 VDC for the wideband amplifier, and 28 VDC for the power amplifier. Not only are the voltage values not standardized, the digital and analog outputs’ return paths are required to be isolated from one another.
Leveraging an existing COTS product enables a manufacturer’s design team to tailor the output voltages according to the requirement and separate the outputs into two isolated groups. This design approach helps the customer achieve a complete radar design with an integrated power solution in a single VPX chassis, all of which can be completed in a short schedule of less than three months from engagement to delivery, and aligning to recent open architecture acquisition directives, such as SOSA and MOSA.
Mike Eyre is global marketing manager at Milpower Source in Belmont, New Hampshire.
Milpower Source https://milpower.com