Qualified components in military and aerospace design: terminating and attenuating microwaves in space
StoryFebruary 12, 2025
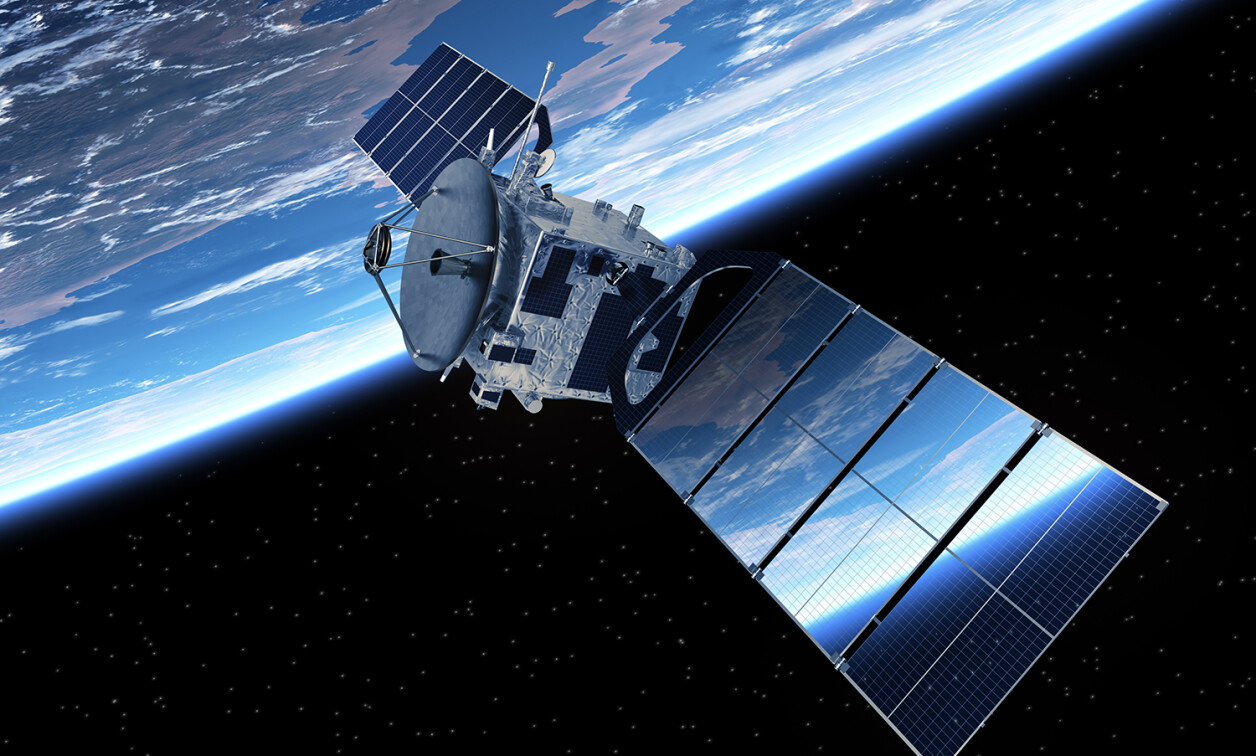
Using qualified components is vital to mission success in military- and aerospace-employed design and deployment, particularly for microwave technology in space termination applications. The parts-qualification process tests that components provide reliable performance for the lifespan of the mission, improving performance and safety. By adhering to industry standards – such as MIL-DTL-39030, which covers the qualification and general requirements for coaxial and stripline electrical loads for testing – and leveraging advanced testing and evaluation methods, designers and engineers can develop reliable and effective space hardware that can withstand the harsh conditions of space.
When designing for space applications, the reliance on qualified components must be balanced. At any given moment, lives may depend on the speed and accuracy of communications. The demanding environment of space missions, characterized by extreme temperatures, high radiation levels, and the absence of atmosphere, necessitates using components that are efficient and thoroughly vetted for reliability and performance.
Qualified parts for space (QPS) components, specifically those for microwave technology in space termination and attenuation applications, must undergo a meticulous part qualification process for the success and safety of space missions.
Build with the goal in mind
These components are essential building blocks in aerospace design, serving as the foundation for the reliability and functionality of spacecraft. Integral to space missions is microwave technology, especially for applications involving communication, radar, and telemetry, due to its ability to transmit data over long distances with minimal signal loss.
SubMiniature version A (SMA) terminations are used to maintain the performance of microwave circuits by terminating unused ports. SMA terminations absorb microwave energy, preventing signal interference and reflection. The use of QPS terminations in these applications ensures the integrity of microwave systems and affirms that these components can withstand harsh space conditions and perform reliably throughout the mission. (Figure 1.)
[Figure 1 ǀ Shown: an example of a space-qualified microwave terminator product.]
QPS attenuators and terminations undergo intense qualification and screening guided by MIL-DTL-39030 and MIL-DTL-3933, which specify the performance and reliability criteria for military and aerospace applications. This testing is conducted under simulated space conditions, including thermal cycling, vibration, and radiation exposure. These tests are designed to identify any potential weaknesses and confirm that the components can withstand the stresses of space travel. Parts are engineered and tested to meet or exceed 1% total mass loss (TML), and 0.1% collected volatile condensable materials (CVCM).
Qualification testing – a rigorous process
The qualification of QPS attenuators and terminations involves comprehensive testing guided by military standards. For QPS attenuators, the qualification process is guided by MIL-DTL-3933 level T, focusing on the rigorous demands of space applications. Note: While our qualification was based on MIL-DTL-3933 level T, attenuators meet the requirements of MIL-DTL-3933/14, /16, and /25 for parts ending with N and S. The T-level is associated with space parts requirements. (Table 1.)
[Table 1 ǀ MIL-DTL-3933 qualification levels summary.]
For QPS Terminations, the qualification is guided by MIL-DTL-39030, particularly /3 and /6. Since no standard exists for space-qualified terminations under MIL-DTL-39030, we developed our own qualification process. This process is partly based on MIL-DTL-39030 and partly on MIL-DTL-3933 level T, ensuring that these terminations can perform reliably in space conditions.
Screening levels tailored for space applications
MIL-DTL-3933 and MIL-DTL-39030 offer two screening levels: N (non-screened) and S (screened). For space applications, our company created three distinct screening levels for space attenuators and terminations: A, B, and C. These levels correspond to different degrees of testing rigor, with Level C being the most stringent and recommended for all spaceflight applications. Each screening level is tailored to ensure that the components meet the specific requirements of their intended application.
- Level A is recommended for nonflight applications, such as preflight system evaluation.
- Level B is the absolute minimum testing recommended for spaceflight applications, such as low orbit satellites, which may need cost-effective space terminations.
- Level C is the highest level of screening, recommended for all spaceflight applications and deep space missions.
Applications in space missions
QPS attenuators and terminators have been integral to several high-profile space missions, including the Emirates Mars Mission, Parker Solar Probe, and Europa Clipper. These components have demonstrated their reliability and performance in the harsh conditions of space; their ability to maintain signal integrity and manage power levels has proven critical in these challenging environments.
Detailed examination of part qualification
The part-qualification process is a comprehensive procedure to test that components meet the strict controls of aerospace applications. Design must account for factors like radiation resistance, thermal stability, and mechanical robustness. For microwave components used in space-termination applications, the standards for qualifying components include minimal signal loss and reflection, ability to maintain function under extreme temperatures and radiation levels, and durability against mechanical stresses such as vibration and shock.
Impact on performance and safety
Using qualified components directly affects the performance and safety of space missions, as microwave components must perform reliably to guarantee effective communication and data transmission. The challenges associated with microwave frequencies in space include signal attenuation, interference, and thermal management. Qualified components help mitigate these challenges, ensuring that microwave systems operate optimally.
Space-qualified SMA terminations are used in satellite communication and telemetry systems to reliably terminate signals and prevent reflection. Reliable microwave components are crucial for long-distance communication with Earth in deep-space missions. SMA terminations are also used in thermo-vacuum chambers to simulate space conditions when testing the performance of microwave systems.
Considerations for microwave frequencies in space
Signal attenuation – the loss of signal strength over distance – can be considerable and detrimental in space. Qualified components are designed to minimize attenuation, ensuring strong and clear signals. Because electromagnetic interference can disrupt microwave signals, space-qualified components are shielded and designed to minimize such interference. Moreover, microwave components generate heat, which must be managed in the vacuum of space. Qualified components are tested for thermal performance to operate within extreme temperature ranges. (Figure 2.)
[Figure 2 ǀ Shown: an example of a space-qualified microwave attenuator.]
Navigating space exploration
Successfully navigating the challenges of space exploration requires a meticulous approach to component selection, testing, and integration. Ensuring that all components can withstand the harsh conditions of space is paramount for aerospace engineers. This reality involves several key strategies:
- Thoroughly test and evaluate: All components must undergo comprehensive testing to simulate the extreme conditions of space. This move verifies that each part can perform reliably throughout the mission’s duration.
- Adhere to standards: It is essential to understand and follow industry standards for component qualification. Standards such as MIL-DTL-39030 provide detailed guidelines for ensuring components meet the necessary performance and durability requirements.
- Collaborate with trusted vendors: Partner with reputable vendors to source reliable, space-qualified components. These partnerships provide access to high-quality parts that have been tested and certified.
- Continuous monitoring and updates: Regularly reviewing and updating components is necessary to keep pace with technological advancements and evolving standards. This proactive approach helps maintain the reliability and effectiveness of space systems.
By implementing these strategies, engineers designing for space applications can effectively navigate the complexities of part selection, integration, and compliance. This consistency will drive the success and safety of their space missions, particularly in the critical area of microwave frequency operations.
From the earth to the sky – and beyond
Qualified components, meticulously vetted and certified for their intended applications, play an indispensable role in ensuring the safe completion of space missions. Through rigorous part qualification and adherence to industry standards, QPS terminations and attenuators are designed to meet the stringent requirements of space and military-industrial applications.
Tibor Urbanek, Product Manager at Cinch Connectivity Solutions, has nearly 30 years in RF and microwave design and leads three product lines at Cinch Connectivity: Midwest Microwave, Semflex, and ModICE. He holds a Bachelor of Science degree in networking and telecommunications and an MBA from the University of Phoenix. Readers may reach the author at Tibor.Urbanek@cinch.com.
Cinch Connectivity Solutions https://www.cinch.com/