Radiation single-event effects: the invisible enemy
StoryJune 15, 2021
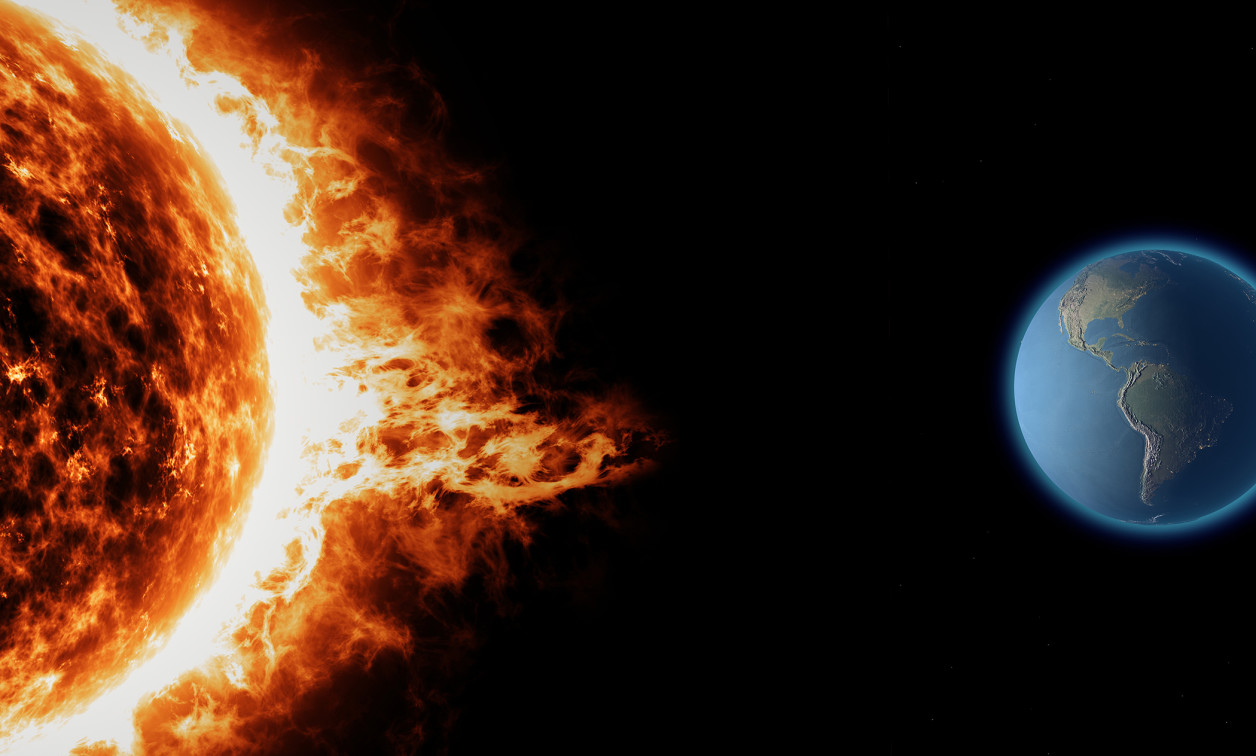
By Richard Sharp and Malcolm Thomson
Cosmic rays are able to cause the failure of electronics in service and may be difficult to separate from other causes of reliability issues. While the electronics failure rate has been reduced to a level acceptable in a commercial context (for example, how often does your computer hang nowadays, compared with 20 years ago?), the military requirements surrounding failure are more stringent. Additional measures are necessary both to achieve the level of confidence demanded for such applications and to prevent the malfunction or total failure of satellites, rockets, missiles, aircraft, unmanned systems, and other equipment.
Ionizing radiation presents an invisible and unpredictable threat to field electronics. The potential for a single high-energy atomic particle to destroy semiconductors has been known in space for decades, but has also become a real issue even at ground level.
Galactic cosmic rays (GCRs) are high-energy particles that come from outside the solar system. GCRs abound in space, but they also penetrate the Earth’s atmosphere. Their impact at sea level – or single-event effect (SEE) – is well-known in the semiconductor industry. SEEs can be either destructive or nondestructive but will both increase the risk of a mission failure. To prevent mission faiture, SEE testing must be performed on the ground to quantify the risks and, if necessary, develop a mitigation plan.
The need to test
Radiation hardness does not happen by accident; design techniques and part selection must be conducted carefully to ensure reliable operation. Testing and verifying the proper functionality of electronic systems against the threat of ionizing radiation is often perceived as time-consuming and expensive. Modeling helps with the design, but SEEs can often come up unexpectedly, which means that testing of the final product is always necessary.
Testing for cosmic-ray effects requires the use of a large particle accelerator, as defined in a number of U.S. Defense Standards, or MIL-STDs. Unfortunately, there are only a few particle accelerators in existence and not enough available beam time. This lack of access is exacerbated at the current time, as the space industry is growing rapidly, increasing the pressure on these facilities. The wait for access can be as long as six months, whether in the U.S. or in Europe.
Pulsed lasers – the new alternative
A recent development now brings the prospect of disrupting the SEE testing roadblock by providing low-cost and fast access to a new test methodology. Powerful, ultrafast, pulsed lasers can deliver the same effect as a cosmic ray. Benchtop-sized instruments make radiation testing possible, quickly and easily, to match tight product development schedules. In many cases, a final verification at an accelerator might still be required, but all of the screening and development can be done with the laser. Translation: Confidence that the product under test will very likely pass at a traditional facility. An additional benefit is that access to this kind of testing enables engineers to build in radiation-hardness assurance at a basic product level, from the very beginning of the design process. Early and fast test data can inform the design, in contrast with forcing engineers to change track with a nearly finished product. Test data speeds up the development process and keeps costs down.
The latest industrial pulsed lasers can blind a person at more than 10 miles. This is the equivalent energy to a single cosmic ray that can burn out a microchip. Laser SEE test systems deliver this energy precisely and in a controlled fashion on the surface of a microchip to identify whether it will survive a cosmic ray strike. Figure 1 shows an array of laser spots overlaid onto a silicon die. The size of the red spots indicates the magnitude of the response to the radiation pulse and where the design might be improved. Screening parts like this, early in the design phase for a product, gives you confidence that you have selected the right components to ensure your equipment will not fail in service.
[Figure 1 | Overlay of an array of laser spots on a microchip die.]
Full characterization of a complex part, such as a microprocessor, is simply too expensive and time-consuming for traditional techniques. NASA recently estimated that fully testing just a single device would require 14 years of beam time. In reality, a few tens of hours might be all that is available. Use of a laser SEE test system means that testing can run 24/7, in the lab or at a facility, making it much easier to accumulate critical statistics and establish confidence in the products.
Using a laser-based SEE testing system instead of trying to garner a spot at a particle accelerator ensures that testing can be done earlier in the design process. Figure 2 shows a typical laser-based testing configuration with a test sample mounted on the precise movement stages.
[Fig 2 | SEREEL2 laser-based SEE testing system with test sample on movement stages. Photo courtesy RTS.]
Richard Sharp is CEO of Radtest Ltd. (which was acquired by RTS in April of 2021). With more than 30 years of experience in the radiation-effects field, Richard brings insight into radiation testing not only for the space sector but also for applications in the military, nuclear, and high-energy physics fields.
Malcolm Thomson, president of RTS, has spent his career in the software and aerospace industries after graduating with a Masters in Computer Science from Hatfield University, Hertfordshire, U.K. He has been a successful entrepreneur and leader, including the formation of a software company that was listed on the NASDAQ and later purchased by Oracle. Prior to joining RTS, Malcolm was the General Manager of Cobham RAD and previously served as the Director of Operations for Aeroflex RAD.
Radiation Test Solutions www.radiationtestsolutions.com