Rad-hard microelectronics demand on the rise in military, commercial markets
StoryJune 14, 2021
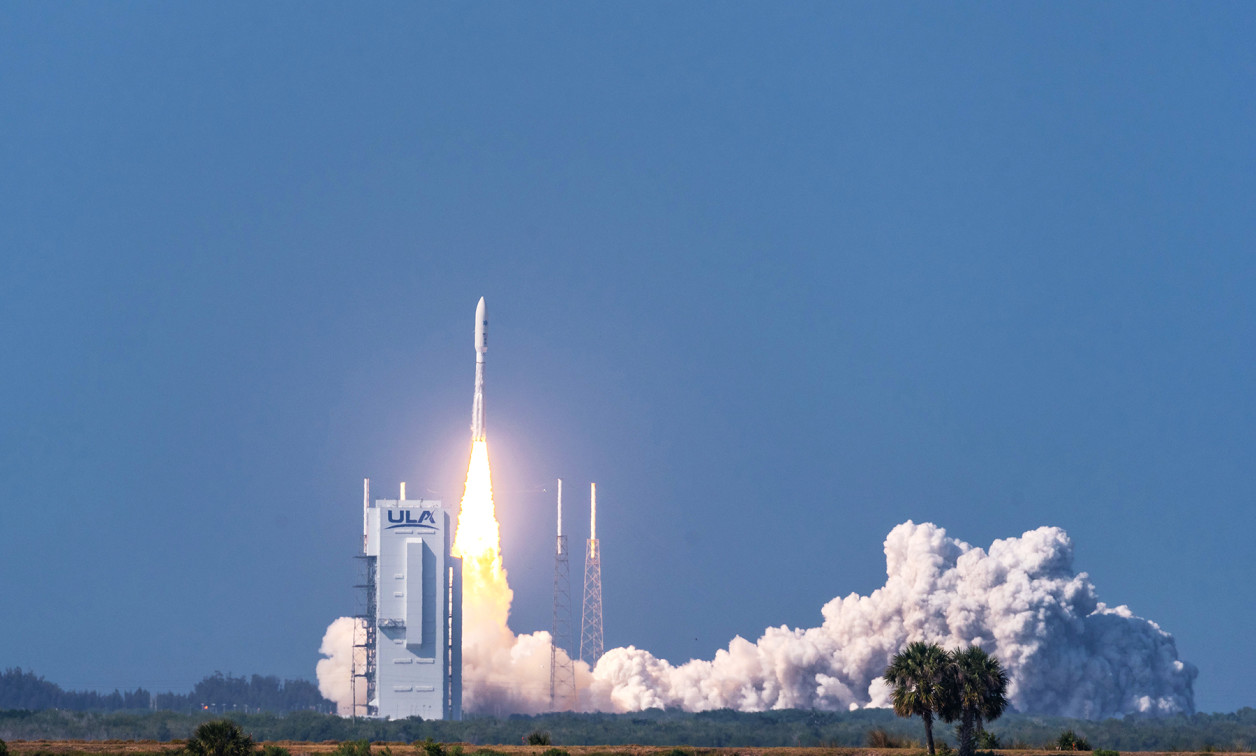
Radiation-hardened microelectronics are in demand, from commercial small sats to NASA manned space missions to military satellite missions in contested space. Designing components for these various applications is a matter of balancing reliability and cost as demand for more commercial off-the-shelf (COTS) components increases.
The space market from a microelectronics perspective is looking quite robust. Many sectors are booming, from commercial mega constellations of small satellites to NASA deep space and planetary missions to contested space and funding for U.S. Space Force and military classified programs.
Part of that robustness – even during a global pandemic – results from continued funding for military space programs from the U.S. Department of Defense (DoD), a trend that continues. Unlike in other markets, military space companies were able to navigate the pandemic with DoD current and long-term funding intact.
An example of the military’s commitment to the space market is the U.S. Air Force’s recent FY 2022 budget request for $885 million for commercial microelectronics, says Larry Hayden, senior director, sales and business development, Vorago Technologies. “We also see the strength indicated by the increased number of design requests and component orders from military customers.”
DoD space budget requests “can be hard to compile as funding is spread across multiple programs and services and each have their own pockets,” says Dave Young, CTO for Cobham Advanced Electronic Solutions (CAES). “However, when you aggregate this spending it represents significant growth for rad-hard microelectronic suppliers.”
It helps to be essential: “The deemed ‘critical’ business rating of this industry helped it weather the pandemic storm,” says Josh Broline, director of marketing and applications, Industrial and Communications Business Division at Renesas. “There have been extended lead times here and there, but it’s been fairly stable. Also, the customer base, since they were still really engaged throughout the pandemic, did their best to maintain procurement as needed, so the demand profile has been relatively stable, even though it’s growing. They also focused on getting POs [purchase orders] submitted in a timely manner, bought what they needed, and planned long-lead item buys to the best of their ability.”
Nothing motivates military planners and military spending like adversarial threats, and space is filled with contestants looking to dominate this domain.
“Contested space continues to be critical area of investment for the DoD as the adversarial threat has grown more complex in that domain,” Young says. “That threat is also a reason the U.S. Space Force was stood up. Adversaries shooting down our satellites could be a very destabilizing event. But, the use of electro-magnetic spectrum (EMS) weapons – directed energy in form of microwaves – against U.S. satellites to deny their warfighting capability is the more likely scenario. Ensuring that our electronics are reliable during such an event could be a key future requirement of the U.S. military.”
Microelectronics technology is a top priority for the DoD in terms of current procurement and future research and development. So much so that the U.S. government is investing in returning semiconductor manufacturing to U.S. shores to ensure a more trusted supply chain for strategic rad-hard electronics. For more on this, read the Editor’s Perspective on page 5.
Commercial pressures
While certainly motivated by external threats. DoD planners are also mindful of costs. Commercial small-sat applications and their low development costs have program managers pressuring rad-hard designers to deliver lower cost components while maintaining reliability and increasing performance.
When constellation providers cut prices “so drastically it becomes very difficult to provide reliable radiation protection,” says Timothée Dargnies, CEO of 3D Plus USA. “But this only makes sense for us when the volumes are high enough to justify adjusting the radiation and reliability performance to meet these cost requirements. Small sats are very interesting from a business case – but only when the volume comes with it.” 3D Plus offers rad hard DDR4 SRAM products. (Figure 1.)
[Figure 1: 3D Plus' DDR$ SRAM works with space-qualified high-end FPGAs: KU060, RT Polarfire, NG Ultra.]
Often it comes down to mission requirements as to what affordability means – whether it’s a commercial or military satellite. “I look at space and satellite applications as data collection – all kinds of data,” says Marti McCurdy, owner and CEO of Spirit Electronics. “The complexity and breadth of what components they launch depends on the cost of a particular satellite and how much the satellite company wants to spend. New space and constellation providers want cheaper components, faster time to market, even trading on reliability to meet that price point.”
Defense primes face similar cost challenges despite the essentialness of military mission requirements. “The Tier 1 primes are all interested in affordability and how to get more commercial technology into space vehicles, while at the same time maintaining reliability and radiation resistance,” Young says. They essentially want “commercial products with high-run rates packaged to survive in space,” he adds.
Those demands for low-cost components in extreme environments might be starting to get tempered as more data comes back on their performance in constellations.
“Many [mega-constellations] are already operational with their full quota of satellites just about launched,” says Anton Quiroz, CEO of Apogee Semiconductor. “So, they are starting to get really good data, from a reliability perspective, such as failure rates, etc. As they move to improve their hardware based on that data they are starting to see that they need radiation-hardened components than they originally thought. Some constellations are seeing a 1% failure rate, and some of that has to be SEU- [single-event upset] attributable.”
Striking the balance
For rad-hard microelectronics designers finding that equilibrium between reliability and affordability can be challenging as requirements differ from platform to platform so there is rarely a one-size-fits-all approach.
“Typically, we find that the customer determines the pedigree to start with; standard COTS or space parts depending on the application specific use of the device to perform additional reliability and radiation testing to their own specs and possibly extend a few parameters during for their own application,” McCurdy says. “This is in addition to testing that the manufacturer performs. The end applications for these parts typically are mission-critical, such as deep space or manned missions, so they want full coverage on the electrical test.”
Companies are also combining rad-hard processes and commercial manufacturing techniques to meet reduced cost requirements. “Our rad-hard microcontrollers target [commercial] applications and DoD programs,” Vorago’s Hayden says. “To meet that cost/performance/reliability balance, we leverage our rad-hard process, but do it with commercial-built parts, interjecting the rad-hard capability at the wafer level, which enables us to leverage commercial manufacturing capabilities to keep cost down.” (Figure 2.)
[Figure 2: Pictured is VORAGO Technologies' radiation-hardened VA416X0 PQFP Arm Cortex-M4 with FPU MCU, hardened with HARDSIL technology.]
CAES faces similar pressures from their commercial customers. “We continue to see that price pressure not so much on military programs, but in constellation space on the commercial space side,” says Tony Jordan, senior director of business development, Space Systems Division, CAES. “Our response is twofold, bringing commercial technology through qualification, then qualifying it for use in space. We take the reliability risk away by leveraging the pedigree of QML for constellation space, repackaging that die and those wafers and then guaranteeing the wafer performance along the lines the customer requires. This enables the customer to meet their reduced cost requirements while also meeting their radiation and reliability needs.”
It comes down to which development and manufacturing flow satellite integrators choose, Broline says. “There are advantages to being part of a large company that does the majority of their manufacturing for nondefense and space industries. You can take advantage of the existing economies of scale already in place. Also, you have to do your best to set expectations with the customer with these different flows or product types. That helps you to stay cost competitive no matter what the business model is.”
“Our rad-hard and rad-tolerant plastic products have been a good fit that provide a balance between [military and commercial] requirements,” he adds. “Both have their own certain level of radiation capability, where the rad-tolerant favors smaller form factors and cost efficiencies while the rad-hard favors reliability assurance.”
Leveraging high-volume commercial foundries and their flow is critical to lowering the cost of rad-hard products Apogee Semiconductor’s Quiroz says. “We leverage these cost and flow advantages on back end [with our TalRad solution], so, we can really take cost out while maintaining reliability. With larger volumes like in the automotive world, companies make many lots of ICs, which brings the cost of manufacturing down. We are leveraging those practices where it makes sense, then performing our higher-quality screening process at the lot level followed by extensive screening of 100% of the parts to ensure we are maintaining reliability. That’s the balance.”
The COTS dilemma
One might ask whether these lower-cost products are examples of commercial off-the-shelf (COTS) components being used in space. Not exactly.
“COTS is interesting,” Quiroz says. “Traditionally COTS components have fallen into the category of rad-hard by serendipity, or RHBS. The perception, right or wrong, is that COTS components are not reliable enough for missions where there are likely to be many SEUs. These components often come in plastic packaging and do not go through the same rigorous lot testing rad-hard by design components. SEUs are a real thing and a lot of commercial parts will fail as they cannot withstand the sustained impact of cosmic rays.”
McCurdy and her team are tackling the COTS low-reliability perception by redefining COTS. “There is a perception that these parts are reliable and not properly screened or qualified for long-term space missions,” she says. “So, we’ve changed the definition. We offer full turnkey solutions that we call military off-the-shelf, or MOTS. For example, someone buys a COTS product and then wants to screen it. Of course, as soon as they touch the product to screen it, the warranty gets voided. Then, after a nine-month screening process it still might fail and they get nothing for it even though they still own the expense of the components and the screening costs.
“Instead, we do all of that for them,” McCurdy continues. “For example, a customer needs 200 flight units. As the distributor we are doing the screening, qualification, and radiation testing, and delivering that specific part number. All the customer needs to do is order that particular Spirit part number and they get full lot traceability and the risk is Spirit’s, not theirs.”
COTS and rad-hard components together
For small-sat capability, system designers are looking at how they can marry COTS with rad-hard components in the same platform.
“In some cases, there is a combination rad-hard and COTS in the same system. Our rad-hard microcontrollers can act as a watchdog, monitoring current if something does go sideways with one of the COTS components, and then resetting the system supervisor,” Hayden says. “That is one way integrators may integrate COTS into systems while maintaining reliability – using rad-hard parts for the monitoring or mission-critical functions.”
“With small sats you could dial down the protection in the satellites then leverage COTS sensors in the payload for missions such as missile detection, ISR [intelligence, surveillance, and reconnaissance], and the like,” Young says. “The military could launch a small constellation to demonstrate the capacity of the small sat for these types of missions. It would be physically hard to shoot down 1,000 satellites, because you have to hit to kill all of them, otherwise the constellation is still operational. The microelectronics challenge would be to leverage the commercial manufacturing and commercial parts to get the price down, while ensuring those same components are sufficiently protected from radiation and EMS-type weapons.” For more on small sats, see our Special Report on page 12.
Once again, it comes down to balancing reliability and assurance, McCurdy says. “In space you want to assure the products on the design that are controlling the critical systems like power management to be rad-hard or rad-tolerant so you know the expected performance. For example, if requirements call for a 12-volt bus on a satellite, you rely on the GaN FET and its radiation resistance to step down the power in the system to manage the lower power products like a LPDDR4.” Spirit offers the Efficient Power Conversion (EPC) Corp.’s GaNFets. (Figure 3.)
[Figure 3: Pictured are EPC GaNFets from Spirit Electronics.]
Open standards
More COTS procurement – depending on your definition – may often coincide with greater adoption of open architectures and open standards.
“System engineering is so much easier with open-architecture designs,” CAES’s Young says. “It’s common sense, but unfortunately until it is widely distributed it work with proprietary systems. [That said] we are seeing demand for the RISC-V standard as opposed to PowerPC in NASA procurements. NASA tends to certify SBCs [single-board computers] and then make certified SBCs available to all deep-space missions.”
“The move toward RISC-V enables us to bring more cores to the table with more DMIPS,” CAES’s Jordan notes. “We are looking at a 16-core solution that gets 30,000 DMIPS, which would be perfect for robotics and autonomous applications, where it would sit behind an antenna or aperture and do intensive number-crunching. We continue to see activity under the NASA Artemis program and other applications for our memory and microprocessor products, including the GR765 microprocessor designed for the European Space Agency.” (Figure 4.)
[Figure 4: The CAES Gaisler GR765 microprocessor is based on the company's LEON5FT fault-tolerant processor core.]
As price pressures mount, there is also growing demand for a military plastic-packaging standard for space. “One of the big gaps in the military space industry is that there isn’t a standard for plastic packaging,” Quiroz says. “However, work has begun on a plastic standard within JEDEC [Joint Electron Device Engineering Council] and the DLA [Defense Logistics Agency]. Much work has yet to be done and the process could be years away, but that an effort is underway to standardize plastic in the military is significant and a positive sign. There is the SAE AS6294 standard that enables upscreening of plastic parts, but it doesn’t comprehend designing a rad-hard plastic part from the ground up, which is what the proposed standard seeks to do.”