Testing FPAs with protoboards versus COTS-based instrumentation
StorySeptember 10, 2024
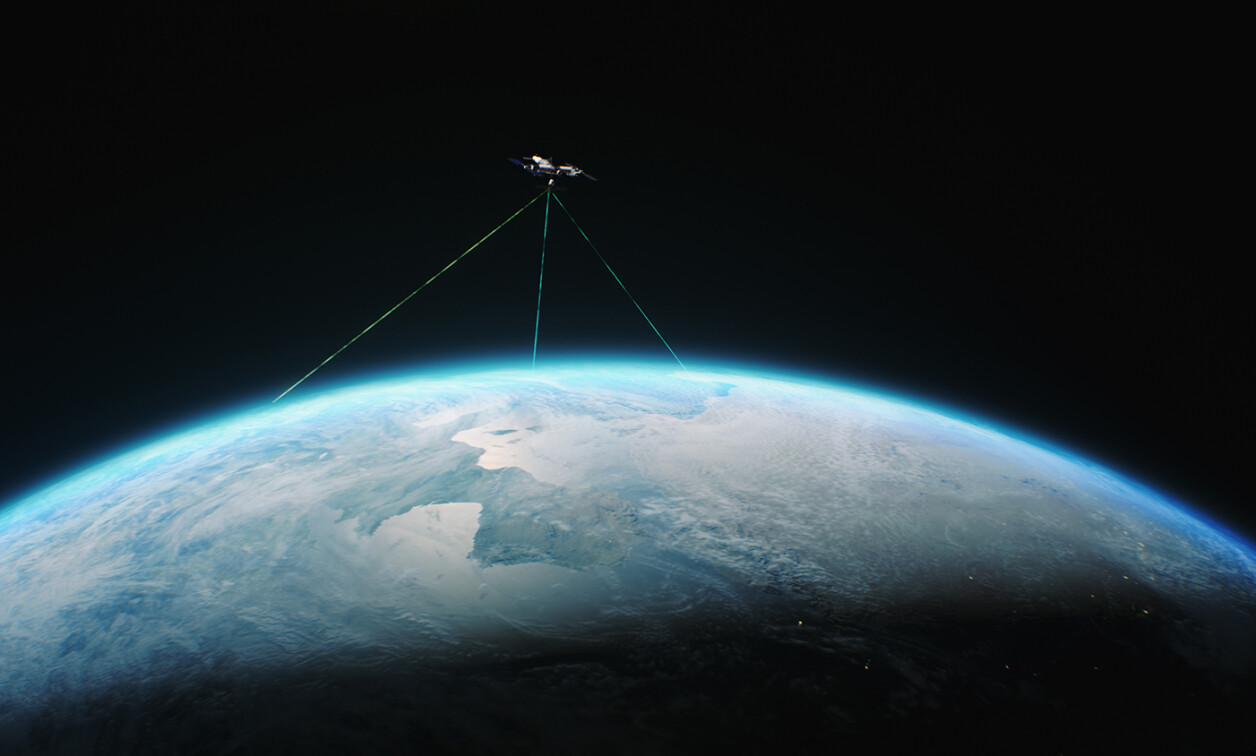
Image- and video-capture technologies have advanced significantly over the past decade, greatly benefiting warfighters and those on ISR [intelligence, surveillance, and reconnaissance] missions. Modern EO/IR [electro-optic/infrared] systems now demand extremely fast data transfer due to high-resolution focal plane arrays (FPAs). EO/IR systems are typically mission-critical and difficult to repair once deployed. One solution: FPGAs [field-programmable gate arrays] can be the backbone to support the design, development, and testing of EO/IR electronics, enhancing the capabilities and reliability of EO/IR systems for warfighters and ISR missions
When designing a new modern EO/IR [electro-optic/infrared] system for use on the battlefield and for ISR [intelligence, surveillance, and reconnaissance] missions, component emulation and testing shortens development by enabling changes to functionality without needing to first build the system. The emulation device outputs signals just as the actual device would; it likely also takes inputs to control its operation. The test equipment takes input signals, just as the actual device would, to characterize the behavior of the component being tested.
The main focus is on emulating either the focal plane array (FPA) or readout integrated circuit (ROIC) to test the FPA electronics or vice versa. Emulation facilitates parallel development, eliminating a common scheduling bottleneck.
Modern EO/IR systems generate high data rates and have large pixel counts. Field-programmable gate arrays (FPGAs) are preferred in emulation and test systems for two primary reasons: First, because FPGAs can be programmed to support different FPAs; and second, because FPGAs offer deterministic, no-jitter behavior. (Figure 1.)
[Figure 1 ǀ Shown are the major components of a typical EO/IR [electro-optic/infrared] imaging system.]
These features ensure that an FPA/ROIC or FPA electronics device connected to a programmed FPGA behaves as if it were connected to the actual hardware. In other words, the electronics that “catch” the signals can’t tell that the electronics that “pitch” the signals are in fact using FPGAs to emulate the subsystem. The two main development paths when using FPGAs are prototype boards or commercial off-the-shelf (COTS) modules. Each of these has its own pros and cons for use.
Traditionally, FPGA prototyping boards, also known as development or evaluation boards, are used due to their state-of-the-art hardware specifications, use of the latest FPGA models, and low cost. Using protoboards for FPA testing requires extending these standalone devices to include, for example, the ability to:
- Interface to device under test I/O via hardware and electrical connections
- Store and recall the large amounts of data contained in images
- Support of ancillary test equipment, such as DMMs [digital multimeters] and SMUs [source-measurement units]
- Define and run test procedures
So while protoboards have a low initial cost and offers maximum customizability, the time and cost to develop and integrate them into a complete test platform is significant. Another aspect to consider with protoboards is their typically short life cycle, since prior protoboard models are displaced by newer ones with the introduction of new FPGA models.
COTS equipment can offer many of the capabilities that the protoboard lacks. For example, COTS standards offer:
- Multilane PXIe buses for high bandwidth and multiple-channel byte streams
- Synchronization between FPGA modules for large numbers of channels
- RAID [redundant array of independent disk] hardware for image-data storage/recall at the data rates
- Tight integration with other instruments like DMMs or SMUs
- Test application development software platforms such as TestStand and LabVIEW
Further, COTS systems tend to have a longer life cycle than protoboards because the COTS vendors want to recover their development costs. This longevity is especially important for production testing, where the vendor of the FPA electronics will want a test system which can be purchased and supported for as long as they will be selling their product.
In the past, the major concerns about COTS systems have been twofold: Is the speed of a COTS system fast enough? And is the customization required based on COTS hardware nearly as large as a custom solution based on a protoboard?
These concerns have been mitigated in recent years mainly due to the fast multilane PXIe buses and emerging common electrical signal specifications – such as LVDS [low-voltage differential signaling] and current-mode logic (CML) serializer/deserializer (SerDes) – which reduce the need for so much customization. These technical advancements have led to systems built on COTS equipment that benefit military and government EO/IR imaging systems by accelerating development, easing deployment, and ensuring reliable products.
The next stage in the development of test and emulation systems for EO/IR FPA electronics leads to systems that heavily leverage COTS products into a ready-to-go instrument. Such an instrument would contain all the necessary hardware and software for emulating and testing, again, without the need for so much electronics integration.
Such instruments can be upwards of 80 percent complete for emulation and testing of FPA electronics, with the remaining customization driven by the unique requirements of every FPA, such as channel counts, connector and digital signal types, and byte stream packing. An example is the AEDIS platform, which can help accelerate FPA and downstream electronics testing by speeding up development times and significantly reducing risk compared to an in-house-developed platform. (Figure 2.)
[Figure 2 ǀ AEDIS is a platform instrument for testing FPAs and/or the downstream interface electronics. It is a pre-built system of both hardware and software components to meet the needs of custom FPA interface protocols. Image courtesy Viewpoint Systems.]
Whether using a protoboard or a COTS-based instrument, FPGAs can be the backbone to support the design, development, and testing of EO/IR electronics, enhancing the capabilities and reliability of EO/IR systems for warfighters and ISR missions.
James Campbell is co-founder and principal engineer of Viewpoint Systems. He is passionate about engineering automated measurements. Jim holds a Ph.D. in electrical engineering from the University of Rochester.
Viewpoint Systems https://www.viewpointusa.com/