When OEMs and LEMs come together: A defense case study
StoryFebruary 12, 2025
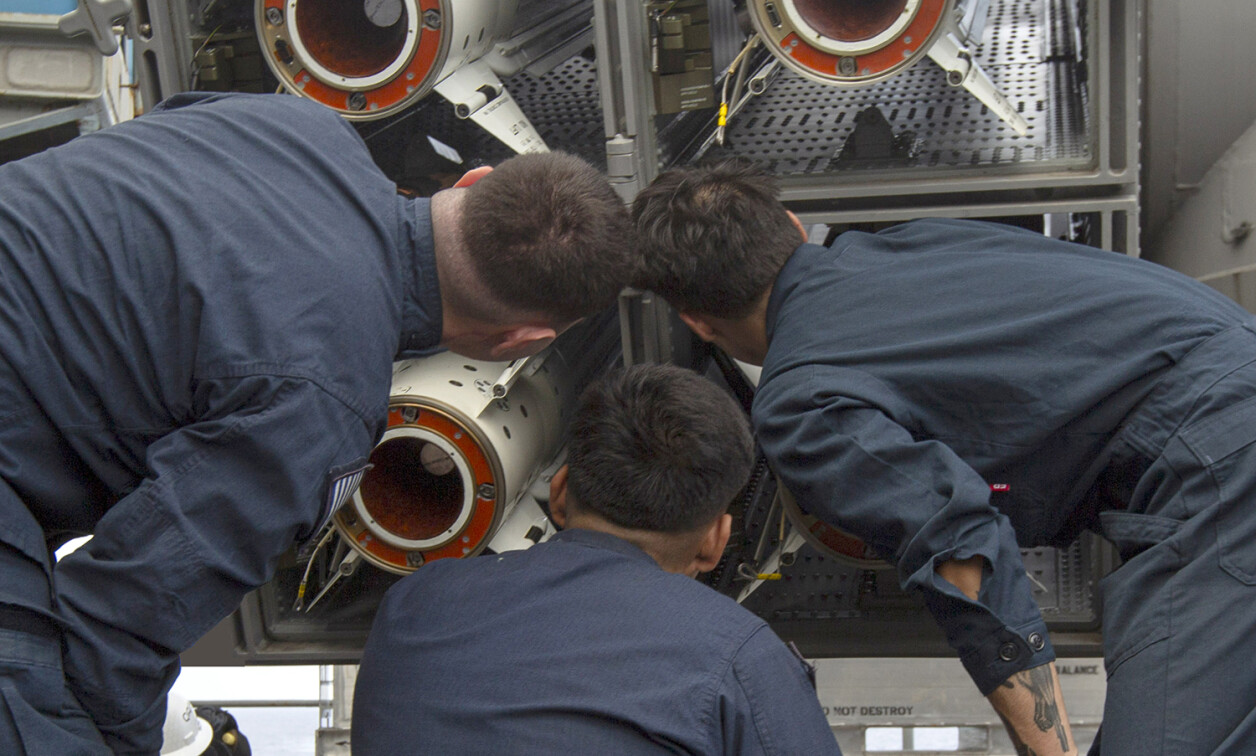
What happens when defense programs can no longer get support for obsolete electronics circuit cards, like computer boards, graphics cards, power supply controllers and many more specialized electronics assemblies that make defense systems “smart”? These circuit card assemblies (CCAs) are often commercial products that have been discontinued by their OEMs.
Commercial off-the-shelf (COTS) circuit card assemblies (CCAs) are great value for companies who make smart defense systems, because they’re ready to order and save all the time, cost, and risk of developing a similar design in-house. However, like all commercially produced items, they eventually become obsolete – meaning they get discontinued.
Legacy equipment manufacturers (LEMs) can offer answers to all players in the defense supply chain who experience these challenges by developing new-sources-of-supply (NSOS) for obsolete electronics. Military service (Army, Navy, Air Force) teams and their primes can take control of diminishing manufacturing sources and material shortages (DMSMS) and rebuild broken supply chains.
For example, over the past six years, we’ve worked extensively with the U.S. Navy and its OEM suppliers to provide obsolete legacy CCAs in support of the RIM-7 Sea Sparrow anti-missile defense system. The Sea Sparrow is used by NATO vessels and domestic U.S. Navy ships to defend against low-flying/high-speed incoming missiles. It’s a ship-saver and a lifesaver.
Obsolete CCAs proved to be a tough challenge after the Navy transitioned support for Sea Sparrow from its prime contractor to “organic” Navy depot support.
Within four years, the responsible Navy program office and their internal suppliers managed to restart the production lines for five DMSMS CCAs, from four different embedded electronics OEMs. Theoretically, these successes saved more than $10 million in taxpayer dollars. Pragmatically, they’ve enabled the program office to maintain readiness in the face of not being able to reliably get upgrade funding.
To enable this success, the Navy teams contracted GDCA to work with electronics OEMs so GDCA could resume production for DMSMS CCAs.
About the NATO Sea Sparrow Support Team
As with many U.S. Navy surface systems, the NATO Sea Sparrow Missile System is supported by a complex supply chain that has evolved throughout the system’s life.
From the acquisition phase through to full-rate production and deployment, the Navy engaged its prime contractor for design, manufacturing, and repair. Internally, the Navy program office, in-service engineering agent, logisticians and depots, and NAVSUP [Naval Supply Systems Command] all coordinated efforts to support the prime supplier.
At the time the Navy decided to take over primary operation and sustainment for the system (around 2018), there was a lot of electronics obsolescence, including many COTS CCAs. This situation meant that the Navy could not get the spares or repairs it needed to complete its sustainment mission.
Moreover, it was often impractical for the Navy to do technology refreshes of the system configuration, because of the extensive cost of hardware replacement and resulting certification. Some of the boards had been discontinued as early as 2006. By the time it assumed support responsibility, the Navy still needed reliable CCAs until the 2030s at least.
Initially, the Navy attempted to take on the remanufacture of these obsolete cards itself. However, after reverse-engineering the first DMSMS CCA, the service determined it didn’t have the resources to sustainably manage multiple and simultaneous reverse-engineering projects.
This is where LEMs come in, as they’re in business to help those customers who cannot upgrade. They also help embedded OEMs resolve a common dilemma: do they end-of-life less profitable products and leave customers in the lurch, or do they continue sustaining low-volume/non-strategic products to keep customers happy?
OEMs grow and maintain market share by introducing newer and better products; LEMs have a more service-oriented business model and partner with OEMs to sustain older “legacy” products. From manufacturing and engineering to sales and supply chain management, LEMs are set up to provide embedded boards that require life cycles beyond what makes economic sense for the OEM.
LEMs offer the added benefit of being OEM-authorized. This means that OEMs have qualified LEMs to take over their legacy designs: producing new, authentic boards and systems that are form, fit, and functionally the same as the products as originally manufactured by the OEM.
Since 2007, we (GDCA) have been providing the U.S. Navy with an obsolete CCA, originally manufactured by Motorola Embedded Computing Group (now Penguin Computing). With support from Penguin, GDCA was able to restart the CCA’s production line and had already provided nearly 500 newly manufactured units and more than 60 repairs over the years. The primary customer at that time was NAVSUP and there was no visibility into the end-users’ system.
We also went on to help the Navy with supplying end-of-life boards from Abaco Systems, Acromag, and Mercury Systems.
The success of these efforts delivered several benefits: First, the Navy was able to secure the boards it needed for as long as they will be required. This allowed the Navy to succeed in its mission to support the warfighter with timely parts and support. Secondly, OEMs could enable support for legacy products without having to spend valuable resources, which enabled allowed them to maintain customer satisfaction while simultaneously focusing on newer strategic products – essential to everyone’s success.
Often, the scope of work required to support legacy designs is so far outside of normal manufacturing processes the risks of project overrun and ultimate failure create a downward spiral of issues and resolution that can last years, with no end in sight. Working with an LEM is not only more productive, but also can save a lot of time, money, and headaches. The LEM acts as a shock absorber between OEMs who must move on to stay competitive and program offices who must stay put to sustain legacy systems.
Ethan Plotkin is the CEO of GDCA, Inc. (“Great Designs Continued Always”), who used his experience in supply-chain risk management (SCRM) to lead the company from its early days as a small OEM into becoming a trusted legacy equipment manufacturing (LEM) partner for defense and related OEMs across the country. Ethan has also worked extensively with the National Defense Industry Association (NDIA) and currently leads the Supply Chain Network Committee, which facilitates collaboration between government, industry, and other NDIA divisions to strengthen national security through industrial supply chains. Ethan Plotkin obtained a bachelor of science degree in industrial engineering from California Polytechnic State University-San Luis Obispo.