Delivering high-voltage power to ground vehicle systems
StoryOctober 12, 2023
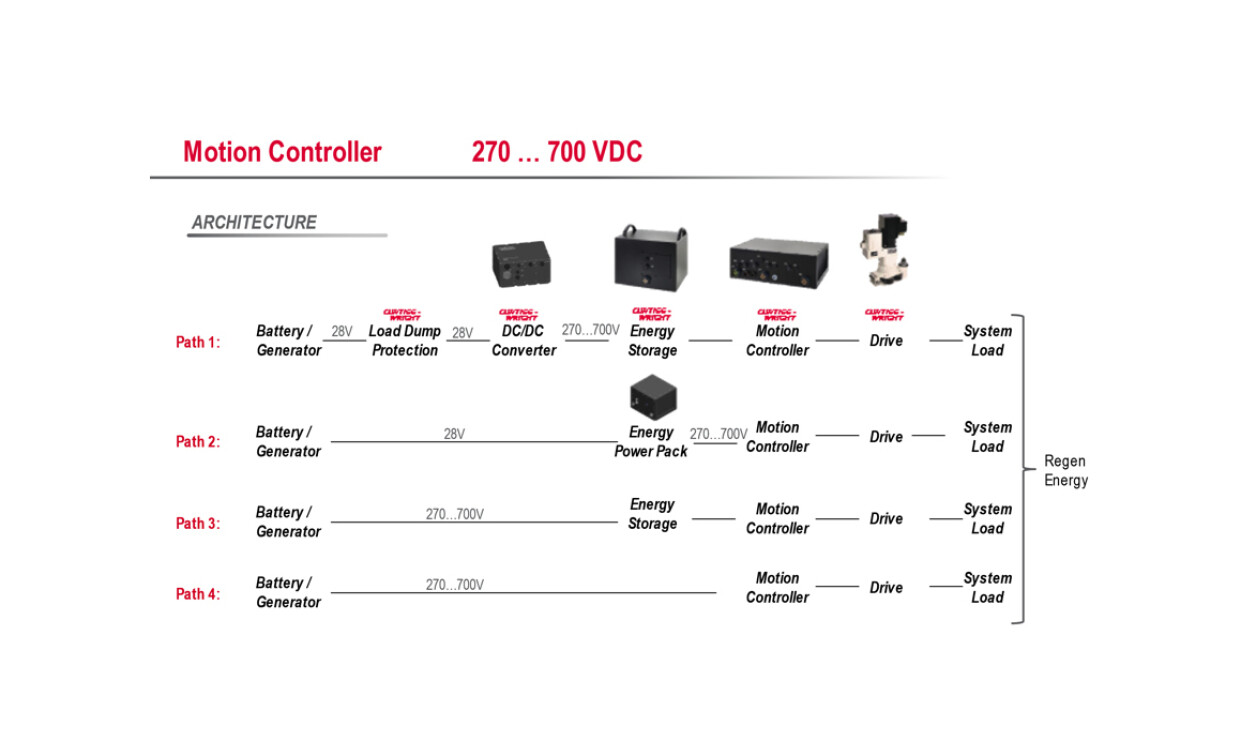
The ability to provide high-voltage power on ground vehicle platforms is a rapidly growing requirement as high peak power is often needed to accelerate a high-inertia load – such as a turret or a weapons system – to a precise position in the shortest possible time. Previously, the delivery of short bursts of peak power came with an associated risk of damage to the vehicle’s electrical systems. One alternative approach, which employs a higher current system, requires large banks of heavy batteries and large cable cross-sections and also wastefully produces large amounts of undesired heat.
As the roles and missions of ground vehicles become more complex, the demands placed on their electrical power-generation and distribution systems have increased dramatically. Even light, high-mobility vehicles are being mounted with sensor, weapons, and communications systems requiring much greater generating capacity than the vehicles were originally designed to provide. Legacy vehicle electrical systems were based on 28 VDC, but this rating does not scale well in size or weight when required to deliver the tens of kilowatts needed to meet future expectations.
In addition to the weapons, sensors, and mission electronics that are becoming part of the regular vehicle kit, dismounted soldiers are heavy consumers of electrical power. This is particularly true when they are away from base overnight and need lights and heat plus recharging of the many portable electronic devices they are obliged to carry. The traditional solution is to truck in mobile generators and fuel, but significant savings in logistics and cost could be leveraged using in-vehicle generating capacity.
The electrical needs of a typical light-utility vehicle such as an HMMWV [High Mobility Multipurpose Wheeled Vehicle, also known as a Humvee] can be met with a 28 V/50 A alternator providing all that is needed for driving, lighting, crew comfort, and battery charging. It’s also true that designers can already anticipate future needs, including support for dismounted soldiers, on the order of 10 kW, requiring 400 A or more at 28 V. Unless exotic, expensive materials are used in its construction, a 400 A alternator becomes disproportionately large and heavy and will therefore dissipate a lot of extra heat. The weight and cost of cabling to distribute this amount of power within the vehicle also become prohibitive; even if discrete bites are taken from the 400 A to distribute it to individual subsystems, the total – if distributed over any distance – will still add up to the same weight and cost. For these reasons, many new or upgraded vehicle programs are now generating and distributing power at a much higher voltage, such as 600 V.
Generating power at 600 V helps to resolve many SWaP [size, weight, and power] issues for new vehicles, enabling the extension of their capability and mission envelopes. This 600 V move can be done on not only light, high-mobility vehicles, but on many other land vehicles with large power-generation and distribution requirements. One advantage: the ability to share common converter, distribution, and power-management technology across a range of vehicle sizes. As the weapons, sensor, and mission systems will become more powerful and dissipate more heat, power- and heat-management systems will need to evolve with them.
An example of a solution for system integrators that require a high-voltage electric gun turret drive system for new platform designs or for upgrading legacy motion-control systems is Curtiss-Wright’s new High Voltage Turret Drive Stabilization System (HV TDSS) system that converts, stores, and controls the platform’s existing continuous low voltage 28 V systems and boosts voltages up to 750 V as needed. The system is aimed at aiming and stabilizing turrets on mobile platforms and for rapid direct drive architectures on mobile weapons systems. The system can be integrated into a vehicle’s existing power architecture without a major impact on size and weight while giving a boost in power. It is designed for use in applications that include large caliber turrets and main battle tank TDSS, and high-speed motion-control systems including active protection systems, optical tracking systems, and directed-energy weapons.
The modular high-voltage system leverages the continuous low-voltage power available on mobile platforms to enable the high-voltage energy buffering required for the higher voltage, short-burst peak power. It also enables the controlled flow of regenerative power back into the power architecture (e.g., energy storage or power source).
Christian Kopp is managing director, Drive Technology, for Curtiss-Wright Defense Solutions.
Curtiss-Wright Defense Solutions https://www.curtisswrightds.com/