Strong signals: Improve antenna performance in high-frequency military applications with radome innovations
StorySeptember 13, 2021
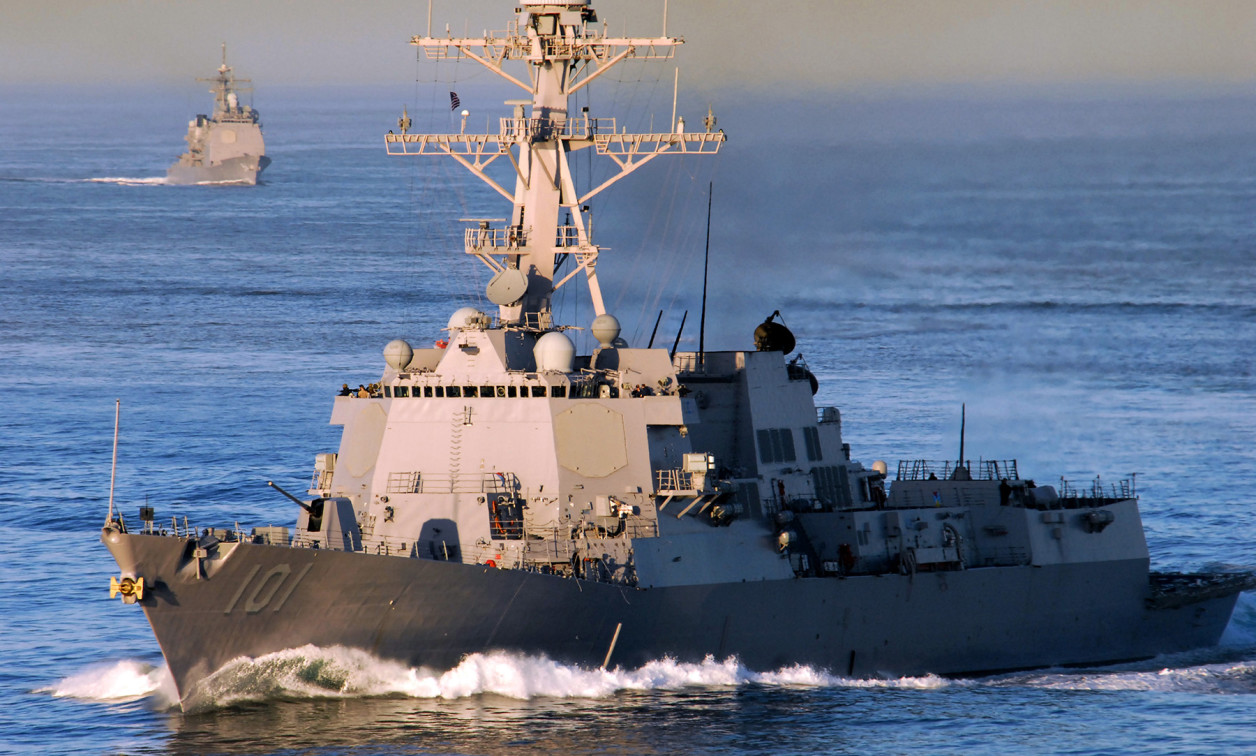
By Rick Johnson, Laird R&F Products and Eric Trantina, Laird Performance Materials
High-quality antenna performance protects lives and military assets. However, as defense and aerospace communications systems operate at higher frequencies, optimizing signal quality while also protecting antennas from harsh environmental conditions becomes more difficult. The key to addressing these challenges lies in the radomes that surround and shield antennas. Lowering the dielectric constant of the radome while also making the surround rugged requires a mix of in-depth knowledge of high-frequency communications systems, sophisticated modeling, materials science expertise, and rigorous testing.
From communications systems on ship masts to low-earth-orbit satellites to imaging radar for unmanned vehicles, high-frequency technology applications continue to proliferate in the defense and aerospace arenas. At these higher frequencies, protecting signal fidelity and ensuring pinpoint accuracy is complex and challenging. As with everything in these mission-critical industries, stakes are high.
Reliable and accurate antenna performance can save lives and military assets and is therefore crucial to mission success.
Radomes are at the center of this challenge. Designed to protect sensitive radar equipment from environmental conditions, the radome plays an important role in antenna signal quality. Let’s start by looking at the three big issues the defense and aerospace industries face today when developing and deploying radomes:
- High angles of incidence: Antennas used in defense and aerospace applications routinely need to scan at angles of plus or minus 60 to 80 degrees. Sending signals through radome material at these off-normal angles can create energy reflection and/or absorption and reduce signal quality.
- High-frequency communications: The use of high frequencies (30 GHz to 60 GHz) increases data throughput and enhances the military’s communications capabilities. However, the performance of an antenna in a high-frequency application can be degraded by use of conventional radome materials.
- Environmental conditions: While the radome material must be rugged and durable so it can handle whatever nature throws at it, the materials that help radomes shield antennas from wind and rain can negatively impact signal performance. Further, in some situations, snow and ice can build up on radome structures, thereby degrading signal quality.
The complicating factor here is that the solutions to these challenges often work against each other. Therefore, design engineers face a balancing act as they work to optimize both antenna performance and a radome’s ability to stand up to environmental conditions.
To successfully improve antenna performance in high-frequency applications, it’s important to recognize the complexities of designing radome materials for high-frequency signals versus standard communication bands below 18 GHz. In the latter case, standard, injection-molded thermoplastic material can be sufficient; but those materials don’t work well above 20 GHz. To achieve a dielectric constant of 2 or lower, designers should seek custom-designed solutions instead of traditional, off-the-shelf radome materials. Using such an approach, design engineers will more successfully balance competing considerations and deploy radomes that support the successful operation of antenna systems.
Mission #1: Reduce the dielectric constant
To improve the quality of signals passing through radomes, the designer can lower the dielectric constant of radome materials without compromising a radome’s ability to protect antennas from environmental conditions. There are two main categories of radome materials:
- A-sandwich materials: Foam is created by injecting air into a resin. Silicone resins, urethane resins, and epoxy resins have dielectric constants around 3. Thermoplastics have dielectric constants around 2-3. Adding air, with its dielectric constant of 1, can lower the dielectric constant of the material below 2. So, foam materials address the dielectric constant challenge. However, as porous, weak materials, foams are ineffective radome materials, which is where protective skins come in. These skins, in turn, must have the lowest possible dielectric constant. Specialty thermoplastic fibers have dielectric constants below 3 and add tough exteriors to protect foams from environmental elements.
- Syntactic materials: These types of materials are made by mixing encapsulated air into resins and calendaring (smoothing and coating) these materials into solid sheets without external skins that have dielectric constants ranging from 1.4 to 1.8. To enhance the impact resistance and ruggedness of these sheets, calendar a fabric inside of the sheet. So, unlike a-sandwich radome materials (which consist of a foam “sandwiched” between skins), these syntactic foam materials are homogeneous, solid radome materials with embedded reinforcement.
Both cases result in a material with a known dielectric constant. From there, signal reflection can be reduced – and in some cases, nearly eliminated – by properly sizing the thickness of the materials. However, eliminating reflection becomes more challenging as angles of incidence increase, which is why it’s important to keep the dielectric constant as low as possible. (Figure 1.)
[Figure 1 | This graph shows the performance of a half-wave radome. By adjusting the thickness and properties of the layers, constructive interference and reduced reflection coefficients are accomplished within the radome. In this example, optimal performance was needed at 28 and 39 GHz, so the radome was tuned to 34 GHz to maximize performance at both ends.]
The calendaring process is key to controlling thicknesses. Another important manufacturing consideration is the process used to manage the amount of air in the material. While air is helpful when it comes to lowering the dielectric constant, it needs to be controlled. High-speed centrifugal vacuum mixers are tools that help engineers manage the amount of air in the material with precision.
In addition to using advanced manufacturing capabilities, it’s important to understand the characteristics of radome materials and performance of those materials under different conditions (environments, frequencies, angles of incidence, etc.) must be considered. There are a number of techniques design engineers can use to measure the properties of their materials. For example, at high frequencies, free-space antennas can measure insertion loss and phase, helping engineers understand the dielectric constant, loss tangent, and overall performance of materials at different angles of incidence.
The last step is to test and verify material performance, with stringent processes that monitor the quality of those products emerging from high-volume production environments.
Creatively address environmental and signal challenges
Radome designers must of course think about rugged materials that can withstand impact, as described above, but they also must account for weather-related elements like snow and ice. After all, snow and ice have high dielectric constants. Engineers can add thermal conductivity-enhancing chemicals to their radome materials to melt any accumulation of ice and snow on the surface of a radome. Using the radome material to accomplish this dual purpose (dielectric and thermal) simplifies the overall design.
Fair warning: These thermal conductivity-enhancing chemicals raise the dielectric constant, so again – there’s a tradeoff. But by leveraging detailed knowledge of materials and sophisticated modeling and testing capabilities, design engineers can determine the proper mix of materials for the application and successfully reduce the dielectric constant while raising the thermal conductivity of radome materials. For example, designers at Laird R&F Products have created materials with dielectric constants of 1.4-1.6 and thermal conductivities of greater than .1 W/mK [watts per meter thickness].
When it comes to optimizing signal quality, design engineers can creatively use absorbers in their radome designs. It may seem counterintuitive, but the use of microwave absorbers can clear up radar signals and reduce back and sidelobes – especially over high angles of incidence – when used as a “skirt” along the sides of an antenna and around a radome.
[Figure 2 | An absorber “skirt” can combat back and sidelobes and improve antenna signals. The red lines in the image above show how signal scatters when unimpeded by an absorber. The black lines show how an absorber skirt reduces back and sidelobes and helps focus the antenna signal.]
Defense and aerospace design engineers can tackle the multifaceted signal challenges they face, first by recognizing the need for custom radome solutions. Next step: leverage materials knowledge, advanced modeling, and creative engineering to design and implement those solutions. Final piece: Rigorously test to verify performance. By taking this comprehensive approach to design and deployment, engineers can improve the performance of high-frequency defense radar systems.
Rick Johnson is the aerospace and defense director at Laird R&F Products, a DuPont business. Laird R&F Products’ operations, testing and manufacturing facilities are located in Carlsbad, California. Readers may contact him at rick.johnson@randf.com.
Eric Trantina is product manager for integrated solutions and electromagnetic absorbers at Laird Performance Materials, a DuPont business. Get in touch at eric.trantina@laird.com.
Laird R&F Products/Laird Performance Materials * https://www.laird.com/