Overcoming EOL and limited supply-chain visibility
StorySeptember 10, 2024
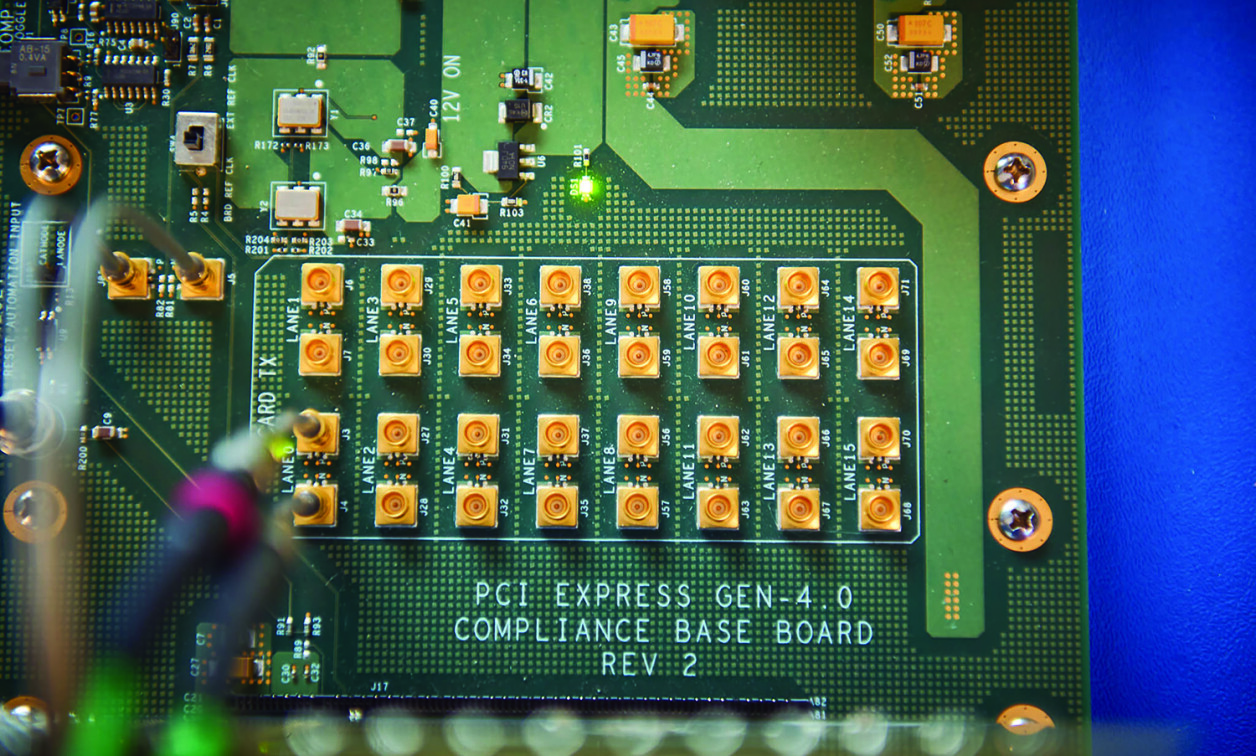
Component obsolescence and end-of-life (EOL) issues can present major obstacles in the electronics supply chain. Designers and companies in the military-electronics arena can overcome these serious challenges by implementing proactive strategies such as obsolescence analysis and forecasting to identify at-risk components early. Also useful: second-sourcing as a way to identify alternative components during the design process. Establishing strong relationships with different suppliers is crucial to secure advance notice and support for transitions, maintain strategic inventory levels of critical components, and design products with flexibility to adjust as required. Additionally, investments in continuous redesign and qualification processes ensures that products remain up to date and compliant with industry standards and regulations.
Component obsolescence and end-of-life (EOL) are significant obstacles in the larger military-electronics supply chain. While hardly a new phenomenon, the rate at which electronic components reach EOL and obsolescence has dramatically increased over the past several years. The current state of the electronic component market, and the state of the supply chain overall, make it much more difficult to source even nonobsolete components. The acceleration of EOL announcements along with widespread trade disruptions across the globe has created a truly volatile environment. Owing to the relatively long product life cycles required by the military and aerospace verticals the supply chains for these applications are even more susceptible to disruption.
To effectively meet the challenges in the current market, it is crucial to understand the root causes of product and component obsolescence and the factors that drive EOL. The insights gained from diagnosing these causes enable manufacturers to employ different strategies and practices to mitigate the effects of obsolescence, EOL, and various other supply chain disruptions.
The primary factors impacting obsolescence
Before beginning to mitigate their effects, it is crucial to understand the root causes of component and product EOL and obsolescence. Broadly, the factors driving EOL and obsolescence can be categorized into: technological, economic, and regulatory. (Figure 1.)
[Figure 1 ǀ PCB transistors, components, and laminates are among the products facing obsolescence in the military-electronics arena and the wider electronics world.]
Technological: Electronics and their components are far and away the most rapidly advancing products across markets. Continuous research and development lead to frequent introductions of novel technologies while semiconductor, processor, and memory innovations rapidly surpass the capabilities of older components. Further, as electronics expand into new verticals, a wide degree of specialization must occur. To use military verticals as an example, the adoption of SWaP-C2 [size, weight, power, cost, and cooling] pushes manufacturers to improve and make nearly every component more efficient. Conversely, military hardware manufacturers also must support a considerable number of legacy products.
Economic: Newer components offer notably higher processing speeds and capabilities, making older components unable to meet evolving performance requirements. As manufacturers gain more experience with new techniques, it often becomes cheaper to manufacture these newer, more advanced products than older models.
Technological advancements drive a constant cycle of innovation and obsolescence, pushing older components to EOL as more advanced and efficient technologies emerge. This cycle is crucial for progress but creates challenges for both manufacturers and consumers in terms of component sustainability and legacy product support.
Regulatory: The regulatory and compliance factors driving EOL and obsolescence are fairly straightforward. Wider and more comprehensive environmental laws and regulations [that affect the use of substances in products sold into the European market] – such as RoHS [Resistance of Hazardous Substances], WEEE [Waste Electrical and Electronic Equipment], and REACH [Registration, Evaluation, Authorization, and Restriction of Chemicals] – ban the use of certain chemicals, materials, or manufacturing processes used in older components. The same applies for safety and standards compliance: New standards can suddenly make older components and processes noncompliant and deemed unusable.
Supply-chain disruptions
The dynamics of the electronic component supply chain influence the overall market, affecting production costs and product availability. The supply chain for electronic components is highly globalized, with different stages of production often spread across various countries. While this widened production helps in cost reduction, it does increase vulnerability to geopolitical and logistical issues. This reality is especially true for areas and regions that produce highly specialized components or products. (Figure 2.)
[Figure 2 ǀ The supply chain for electronic components is highly globalized, with different stages of production often spread across various countries.]
Natural disasters
Natural disasters are among the most common and visible supply chain disruptions. One of the most recent examples was the 7.4 magnitude earthquake in Taiwan on April 3, 2024. Although Taiwanese manufacturers expect only minor impacts on their production, the event illustrates the inherent vulnerability of the electronic component supply chain. Taiwan is responsible for manufacturing more than 90% of the world’s most advanced semiconductors, and roughly 60% of the total semiconductor market.
Trade restrictions and tariffs
In May 2024, in coordination with acts to increase U.S.-based component and semiconductor manufacturing, the U.S. government announced widespread tariffs on Chinese imports. Among the tariffs is a 50% duty on semiconductors, set to begin in 2025. While one of the main goals of this import tariff is to protect and accelerate U.S. semiconductor manufacturing, it has accelerated a supply-chain shift in Taiwan, thus concentrating more of the global manufacturing into a single geographic location. The concentration of manufacturing has essentially created a single point of failure for the entire semiconductor manufacturing industry.
Mitigating EOL and component obsolescence
The electronic component supply chain’s complexity and globalization make it both efficient and vulnerable. Effective management and risk-mitigation strategies are essential for maintaining market stability and competitiveness in the face of potential disruptions.
Obsolescence analysis and forecasting can largely improve the electronic-component supply chain by identifying and managing the risks associated with the life cycle changes of components, products, or systems. Such a move involves monitoring the status of components, forecasting their EOL dates, and implementing strategies to mitigate the impact of obsolescence, such as sourcing alternative components, proactively planning for redesigns, or managing inventory levels. A wide variety of software solutions and obsolescence databases are now available to aid in this process. (Figure 3.)
[Figure 3 ǀ Shown: An example of a software dashboard tracking obsolescence forecasting.]
With a more informed and data-driven obsolescence forecast, manufacturers can more easily take steps to ensure supply-chain resilience. By fully understanding component life cycle status, manufacturers are better able to manage relationships with suppliers, enabling the identification of alternative components and suppliers in advance and ensuring a more resilient supply chain.
There are many benefits to forecasting and supplier management beyond fulfilling the need for components. By managing obsolescence effectively, manufacturers and designers can better allocate resources to focus on innovation and product development, rather than devoting resources and manpower to legacy component issues. All of this combines to create a smoother transition to newer technologies, minimizing disruption to ongoing projects and product lines.
If, however, a manufacturer is unable to transition a product away from obsolete parts, there are still a few viable alternatives to address for EOL components and products. One such option is a legacy equipment manufacturer (LEM). An LEM is a type of specialized electronics producer that manufactures, supports, and services embedded-board level products after an OEM is no longer able to support the product and EOL notices have been issued. LEMs offer an effective stopgap to support legacy and EOL products but should not be viewed as a long-term solution. Generally, the lead times associated with LEM manufacturing are longer and the finished product costs are higher.
Proactively combating obsolescence and EOL
Component obsolescence and EOL present major obstacles in the larger electronics supply chain, which can be a critical problem in the military electronics sector. These challenges can be overcome by implementing strategies such as obsolescence analysis and forecasting to identify at-risk components early, together with second sourcing to identify alternative components during the design process. Establishing strong relationships with different suppliers is crucial to secure advance notice and support for transitions, maintain strategic inventory levels of critical components, and design products with flexibility to adjust as required. Additionally, investing in continuous redesign and qualification processes ensures that products remain up-to-date and compliant with industry standards and regulations.
Drew Thompson is a technical writer and marketing specialist for Sealevel Systems, the leading designer and manufacturer of embedded computers, industrial I/O, and software for critical communications. He holds an M.S. in global studies and international affairs from Northeastern University. Thompson can be reached at drew.thompson@sealevel.com.
Sealevel Systems • https://www.sealevel.com/