Military robotic systems funding steady as the systems continue to save lives
StoryApril 09, 2015
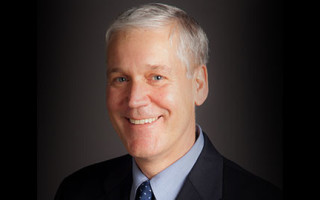
U.S. warfighters often sing the praises of unmanned ground vehicles like iRobot's 510 PackBot because it saves lives in areas such as improvised explosive device detection (IED). In this Q&A with Tim Trainer, Vice President, Robotics Products International, iRobot Defense & Security business unit in Bedford, Mass., he discusses how UGVs have impacted the warfighter from a safety and efficiency standpoint and covers the outlook for robotics technology in the military. Edited excerpts follow.
MCHALE REPORT: Please provide a brief description of your responsibility within iRobot and your group’s role within the company.
TRAINER: I am Vice President of Robotic Products International at iRobot. I cover everything outside North America including the Asia/Pacific and European regions. My legacy is from the defense side, as a retired U.S. Navy Captain. My early years at iRobot were in the defense market and it has been a nice transition to the international business as that market focuses on what is successful and working in the U.S. market.
MCHALE REPORT: The Department of Defense (DoD) released its FY 2016 budget request in February with an increase in overall funding, almost a reverse trend from the last few years. How do you see the funding outlook for unmanned ground vehicles? Has the DoD clearly defined what missions it will need these platforms for over the next five years?
TRAINER: There is evidence of increased funding that we can see within the DoD and in major programs. The military and Army have regrouped and taken a look at what they need for ground robotics. That vision had taken a pause and is now refocused. This is good news that has not been seen for the last couple years.
The major programs focused on ground robotics include Common Robotic Systems- Individual (CRS-I), a 20-pound vehicle that is getting research and development funding; the Man Transportable System (MTRS) Increment 2, which has funding; and the Squad Multi-purpose Equipment Transport (SMET). New mission requirements for ground robotics will drive industry and government investment. Some will be joint programs with the Army and Marine Corps generally, while some will go DoD wide and involve the Navy and Air Force as well. Special Operations Forces (SOF) will also have unique opportunities that will often be more customized.
The budget reductions and troop drawdowns aside, all folks see that and understand that the Army and other services will need to sustain current systems, which also makes us feel fairly good about where the market is going.
Internationally it’s a dangerous world out there that can benefit from robotic systems. Aside from the military, we’ve also deployed our platforms to help secure major events in Brazil, including the Papal visit, World Cup, and the upcoming summer Olympics. Growth has been very good internationally.
MCHALE REPORT: Please provide an example of current unmanned ground platforms iRobot supplies to the U.S. and International countries.
TRAINER: Our most popular military platform is the 510 PackBot, of which 4,500 are deployed to U.S. military and domestic customers around the world. We also have a new HAZMAT configuration kit for the multi-mission PackBot system.
iRobot also provides robotic solutions to state and local first responders, nuclear facilities, industrial applications, and for the expanding chemical, biological, radiological, and nuclear (CBRN) mission set. Counter-improvised explosive device (IED) work also continues, especially with the risk of chemical weapons attached to an IED. We are always looking at new sensors to enhance mission effectiveness.
MCHALE REPORT: What types of payloads do iRobot’s unmanned ground vehicles carry? ISR sensors? Have any been weaponized?
TRAINER: We have not weaponized any of our robots, but do have a payload we call a disruptor, and that some call a water cannon. It is essentially a shotgun barrel attached to the robot that can fire a water charge at high velocity and at short range to separate an IED initiation device from its explosive charge, rendering it safe. It can also discharge clay and steel rounds.
From there we also have thermal cameras for ISR capability, two-way audio, and GPS for mapping and to allow operators to understand where the robot is to map out suspected hazards. Recently the Canadian Department of National Defense for their Recce system requirement competitively selected our new PackBot CBRN HazMat suite.
MCHALE REPORT: What is your approach to using COTS embedded computing technology and open architectures in your payload and control systems?
TRAINER: For payloads we prefer to buy those from the market then integrate them onto the robot so we can focus on what we do best, which is robotics.
We have leveraged commercial computing technology for our new uPoint Multi Robot Control (MRC) system – a universal control system for all the company’s defense and security robotic platforms. It incorporates at touch screen tablet that runs on the Android operating system. Prior control stations leveraged a laptop with a joystick for control. The MRC uses an Android app that has touch screen control virtual joystick that enables operators to touch and drag anywhere on the main video feed to control the robot. It also enables users to share data with other team members. Through networking technology it can tie into the cloud to offload some computational requirements to provide even greater processing capability.
The Army has also looked at Android tablets and the CRS-I system is also expected to leverage the Android technology.
MCHALE REPORT: Reduced size, weight, and power (SWaP) requirements are hitting all applications in defense electronics. How are they impacting your unmanned ground vehicles and their payloads?
TRAINER: Historically operators want something that weighs nothing, costs nothing, and does everything. In other words SWaP has always been an important consideration especially in dismounted missions. Our five-pound 110 FirstLook was designed with SWaP in mind. It is so light an infantry soldier can carry it with him and actually throw it into a target area.
Extending the endurance of these systems and increasing computational capability are also critical design factors. More and more things are driving autonomy in these systems. As we shrink the platforms we are also enabling more computational power with each generation of processing chips in the same footprint. An example of this would be the uPoint MRC mentioned above, which while smaller has more computational capability than previous control stations.
MCHALE REPORT: What type of training is involved for using your ground robots on missions?
TRAINER: Ideally we wouldn’t have to provide much training. An example of a platform with minimal training requirements is the 110 FirstLook system. If an operator has to deploy the system into a village or an unknown situation we want the task of remembering how to operate the device to be intuitive and easy so they can focus on the mission. This is also an issue with first responders and police, who are not always training with their robots, often only using it once a month. Therefore ease of use is paramount.
MCHALE REPORT: What feedback do you get from military operators of your unmanned ground vehicles?
TRAINER: What we hear from them is that they are getting tasked with increased mission sets and are asking us to help them prosecute those different missions with robots. Our robots came in to the world as a counter-IED system and now they are used for checkpoint operations, SOF support CBRN support, etc. The growth of the systems happens with new capabilities and the addition of new missions.
MCHALE REPORT: What impact do you think robotic technology has had on the warfighter?
TRAINER: It really brings safety and standoff to the U.S. service person. For example, from an aviation perspective in Vietnam to attack a target we would send a whole squadron, in the first Gulf War, we would send a flight of aircraft, now we are sending one drone aircraft to attack multiple targets. Similarly, unmanned vehicles allow standoff and reduce the risk to the individual warfighter. The same thing is happening with unmanned ground systems, where we are separating warfighters from hazards and helping them perform these dangerous tasks more effectively and safely.
UGV mission sets will continue to grow as capabilities expand. We will see the same progression on the ground that we’ve seen in the air though the ground-based terrain environment, which poses a significantly more difficult physics problem than that faced by airborne vehicle.
MCHALE REPORT: Looking forward, what disruptive technology/innovation will be a game changer for unmanned ground vehicle designs and/or payloads? Predict the future.
TRAINER: The Holy Grail is autonomous operations. We won’t get there in five years, but maybe in 10. This will reduce the workload on operators, allowing them to control multiple robots. Robots might be sent into hostile environments as a squad, entering a village or building to identify suspect packages and or people and then report back to central command.
What will help enable this is leveraging what works from the commercial side of our business and using it for defense platforms and vice versa. This trend has increased since we re-organized our engineering operations by merging the government and consumer divisions together. We married the higher tech from our lower volume markets with the expertise from our high volume markets. It provides an opportunity for cross-pollination and the germination of revolutionary ideas.
An example would be how we developed our Ava remote presence platform, where the robot moves about an office space providing high-definition video, teleconference capability with sensors that enable obstacle avoidance – all things that were originally developed on defense side of our house that has found a home in our remote presence business. Interestingly some of that technology is now finding its way back to the defense side.
Tim Trainer is vice president, robotics products international for iRobot’s Defense & Security business unit. Prior to this appointment, he served as interim general manager and vice president of operations where he was responsible for all manufacturing, contracting and program management. Prior to that role, Trainer was vice president, programs and vice president, engineering. He joined iRobot after a 30-year career in the U.S. Navy, including positions as commanding officer of the Naval Aviation Depot (NADEP), North Island, Calif., head of Naval Air Systems Command’s Air Vehicle Engineering Department and various program positions. Trainer holds a bachelor’s degree in mechanical engineering from Marquette University, a master’s degree in aeronautical engineering from the Naval Postgraduate School in Monterey, Calif., and he is a graduate of the U.S. Naval Test Pilot School in Patuxent River, Md.