Airborne attritable systems and open systems
StoryMarch 18, 2025
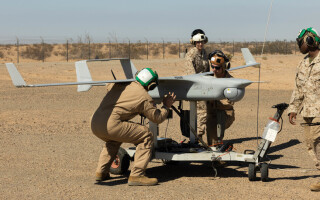
The U.S. Department of Defense (DoD) is investing heavily in airborne attritable systems as a cost-effective approach to project force and influence. The DoD’s directive to use modular open systems approach (MOSA)-based solutions positions commercial off-the-shelf (COTS) component vendors to meet the form factor, weight, and cost limit requirements of airborne drones uncrewed aerial systems (UASs). This move toward lower-cost and more easily replaced uncrewed systems opens up new opportunities for suppliers of COTS components.
Traditionally, the U.S. battlefield arsenal has included expendable items such as missiles, along with expensive sophisticated manned platforms like fighter jets. Expendable systems are designed and intended to be used once, without the expectation or need for retrieval. For sophisticated manned platforms, such as tanks and fighter jets, however, retrieval is critical due to the monetary cost or mission sensitivity as well as their role in troop safety.
Recently, a third category known as “attritable systems” has emerged, which sits between these two extremes. Attritable systems are intended to go out, perform their mission, and return. The key difference between sophisticated manned platforms and attritable systems is that attritable systems accomplish their mission at a much lower cost so that failure to return will not have a significant overall impact, making it more acceptable if an individual system is lost. Because of their lower cost – compared to the tens of millions of dollars posed by sophisticated platforms such as an F-35 – attritable systems can be built in far greater quantities. While attritable equipment is not actually meant to be expendable, when compared to sophisticated manned systems, a higher rate of loss may be deemed acceptable by the commander.
What systems are attritable?
In today’s arsenal, certain categories of uncrewed systems are often designed to be attritable. Airborne systems provide the best-defined classes of these platforms, driven by the fact that they need to share civilian airspace. U.S. Department of Defense (DoD) interest in attritable systems has grown substantially in recent years as new technology has becomes available. While it’s possible to buy a small, low-cost uncrewed aerial system (UAS) at a big-box consumer store, it must operate within the rules of the FAA, which classifies UASs into five distinct groups.
Where attritable applications fit into the various airborne UAS groups is not a hard-and-fast rule, but the sweet spot seems to be around Group 3: For example, if a Group 5 Global Hawk was downed, fairly extensive efforts would likely be taken to retrieve it because of the sophisticated sensors and potential sensitive data the aircraft carries. In contrast, an inexpensive Group 1 UAS is almost never worth retrieving, especially if doing so would risk a soldier’s life. In terms of re-use, an expendable system is expected to be used only once, an attritable system might be used from one to hundreds of times, and a sophisticated system used many times for years.
Group 1 airborne UASs are typically inexpensive, small, and hand-held. In a warfighter scenario, a Group 1 craft might be carried by a soldier who can send it into a building to look around corners and doors using an onboard camera to help identify the presence of an adversary without putting a warfighter at risk. Examples of such platforms include RQ-28A, RQ-11 Raven, WASP, and Puma.
Group 2 drones are typically built for low altitude and longer endurance and can fly as high as 3,500 feet. Missions may last for an hour or two, compared with maybe 20-30 minutes for a Group 1 UAS. With Group 2, the possible payload weight starts to go up as well: Where a Group 1 craft might be able to carry 5 pounds of payload, a Group 2 UAS may be able to carry twice that. Examples of Group 2 platforms include ScanEagle, Flexrotor, SIC5, and PDW C100.
Group 3 uncrewed aerial systems (UASs) are intended for medium-altitude, long-endurance missions. This category of craft can have a maximum takeoff weight as much as 1,320 pounds. Group 3 UASs basically represent the sweet spot for attritable UAS platforms due to their combination of relatively low cost and generous maximum takeoff weight. Examples include Shield AI, V-BAT, RQ-7B Shadow, RQ-21 Blackjack, Arcturus-UAV Jump 20, Navmar RQ-23 Tigershark, SIC25, and Vanilla Unmanned.
Group 4 and Group 5 craft will typically have a maximum takeoff weight greater than 1,320 pounds, with Group 4 UASs sometimes equipped to carry a missile and Group 5 systems intended for use in both for reconnaissance missions and strike. Examples of Group 4 include MQ-8B Fire Scout, the MQ-1A/B Predator, and MQ-1C Gray Eagle; examples of Group 5 UASs include MQ-9 Reaper, RQ-4 Global Hawk, MQ-4C Triton. (Figure 1.)
[Figure 1 ǀ Group 5 uncrewed aerial systems, like the Triton seen here, are larger platforms designed for both reconnaissance and strike missions, typically fielded by the U.S. Air Force and Navy. Image courtesy Northrop Grumman.]
Group 1 and Group 2 UASs are more likely to be fielded by the U.S. Army, while Group 3, Group 4, and Group 5 are more likely to be seen in Air Force operations.
Open standard – UAS connection
There are a number of open standards that have been adopted for the design and implementation of UASs. These standards include Mod-pay (Special Operations modular payload design standard); the Sensor Open Systems Architecture, or SOSA, Technical Standard; Vehicle Integration for C4ISR/EW Interoperability (VICTORY); the Future Airborne Capability Environment, or FACE, Technical Standard; GRA, Big Iron, COBRA, Modular Open RF Architecture (MORA), MI-CORPS, and Weapons Open Systems Architecture (WOSA). The DoD’s directive to use modular open systems approach (MOSA)-based solutions positions commercial off-the-shelf (COTS) component vendors to meet the form-factor, weight, and cost-limit requirements of airborne drones from Group 2 to Group 5. The Group 3 systems – the attritable UASs with the best combination of relatively low cost and generous maximum takeoff weight – fall squarely into this group.
Fielding of attritable systems is not far away, as several are being actively developed now. Examples of existing programs for attritable airborne systems include the U.S. Air Force’s Collaborative Combat Aircraft (CCA) Loyal Wingman program. For CCA, the Air Force is working under what it calls a “planning assumption” of the need for 1,000 CCA systems initially and anticipates ordering more than 100 CCAs for Increment 1 in the next five years. (Figure 2.)
[Figure 2 ǀ Collaborative Combat Aircraft (CCA) are capable of collaborating with next generation crewed combat vehicles at a significantly lower cost while increasing survivability on the battlefield. Image courtesy Curtiss-Wright/Kratos.]
Other examples: General Atomics flew its unmanned XQ-67A CCA platform for the first time in February 2024 and began production of the aircraft a few months later. In January 2025, Anduril announced its plans to establish a new factory in Columbus, Ohio, to manufacture its Fury attritable UAS, which is intended to use Anduril’s Lattice software. Also in January 2025, the Air Force held the first test of CCA piloted-drone teaming capabilities with an F-35, during which Lockheed Martin and industry partners demonstrated what the Air Force termed “end-to-end connectivity including the seamless integration of AI technologies to control a drone in flight leveraging the same hardware and software architectures built for future F-35 flight testing.”
The DoD has already awarded 30 contracts so far for attritable UAS solutions under its Replicator initiative through the Defense Innovation Unit (DIU) and Blue UAS. The Blue UAS program, which was stood up in 2020, is described by DIU as “a holistic and continuous approach that rapidly vets and scales commercial unmanned aerial system (UAS) technology for the Department of Defense.”
The U.S. Army and Navy are also developing unmanned attritable solutions for unmanned ground vehicles (UGVs), un-manned underwater vehicles (UUVs), and unmanned surface vehicles (USVs). As with UAS platforms, size, weight, and mission type influences where the concept of “attritableness” best fits for the various categories of each of these platforms.
COTS vendors can support the development of attritable systems with MOSA-based solutions that combine the ruggedness and reliability needed to support UAS re-use with the form factor and cost-effectiveness requirements that attritable unmanned platforms require. (Figure 3.)
[Figure 3 ǀ Curtiss-Wright Parvus DuraCOR 313 is an example of a rugged COTS processor based on MOSA, aimed at use in size, weight, power, and cost (SWaP-C)-sensitive manned and unmanned vehicles.]
Jason DeChiaro is a system architect at Curtiss-Wright whose responsibilities include supporting customers in architecting deployable VPX systems including CMOSS/SOSA compliant designs. Jason has more than 15 years of experience in the defense industry supporting the U.S. Air Force, U.S. Army, and U.S. Navy and the IC community. He received his electrical engineering degree, with distinction, from Worcester Polytechnic Institute in Massachusetts.
Curtiss-Wright Defense Solutions • https://www.curtisswrightds.com/