Power play: Optimizing SWaP on uncrewed systems
StoryMarch 17, 2025
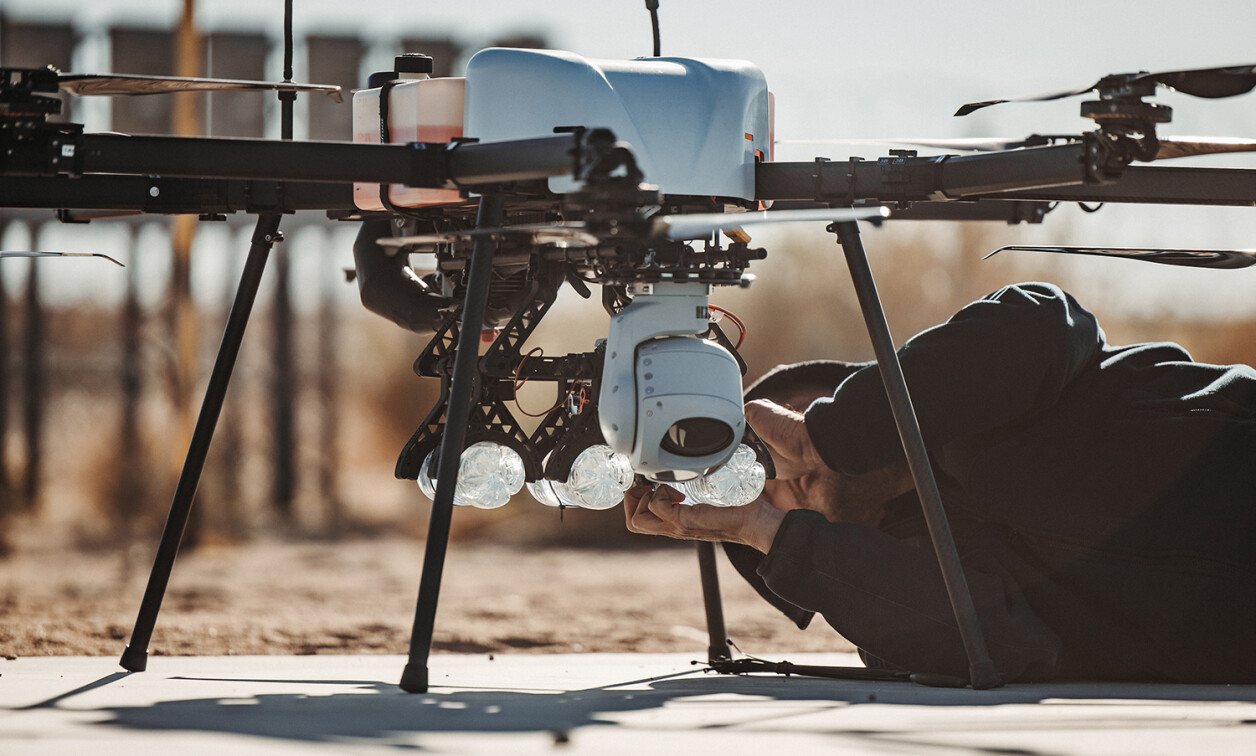
The prospect facing defense contractors is considerable: Pack more computing power, more sensors, and more capabilities into smaller spaces while extending mission endurance. As uncrewed platforms evolve from simple remote-controlled vehicles into autonomous systems with sophisticated sensor arrays, every milliwatt of power must be carefully managed.
A small reconnaissance uncrewed aerial system (UAS) launches into a contested airspace, and its internal systems immediately get to work. The tiny aircraft’s processors crunch real-time sensor data while running artificial intelligence (AI) algorithms, its phased-array radar scanning for threats.
Just a decade ago, placing capabilities such as AI and radar processing on a small UAS would have required a much larger vehicle – or would have drained the batteries in minutes. Now rapid advances in power management and electronics are shrinking what’s possible into increasingly compact packages.
The big challenge: Balancing SWaP-C
Adding capabilities to a platform means – almost inevitably – that power consumption will increase. The U.S. Department of Defense (DoD) has tasked contractors with doing exactly the opposite, however, and that requires a lot of creativity in the industry.
It’s a Herculean task to deliver high-performance processing, sensor fusion, radar, and communications capabilities while working within strict size, weight, power, and cost (SWaP-C) constraints, notes Jeff Massman, senior manager of phased-array platforms for aerospace and defense at Analog Devices (Colorado Springs, Colorado).
“Unmanned systems are becoming increasingly autonomous, requiring real-time AI-driven decision-making, phased-array radar for situational awareness, and high-bandwidth RF communication links, all of which drive up power consumption,” Massman says.
Mark Littlefield, director of systems products at Elma Electronic (Fremont, California), says because uncrewed systems are particularly SWaP-sensitive, “power management and the space taken by the payload hardware are probably the two prime concerns for the system integrator.”
Some experts see size constraints at the component level as the main concern.
“As you get smaller and smaller, all the necessary logistical components of an embedded product – i.e., connectors, power supplies, etc. – play an outsized role in the volume that the product fills,” says Noah Donaldson, chief technical officer at Annapolis Micro Systems (Annapolis, Maryland).
As processing performance increases, so does power-management complexity.
“High-performance computing continues to evolve exponentially and so does the requirement for power,” says Shaun Fischer, division vice president of business development at Abaco Systems (Huntsville, Alabama). “With the growing application of automation and autonomy, the need for more and more power will not subside.” (Figure 1.)
[Figure 1 | The SBC3901 from Abaco Systems is a 3U VPX compute-intensive single-board computer designed for both autonomous and embedded edge-computing systems that require real-time GPU processing, instantaneous data transfer, dedicated encode/decode capabilities, and deep learning (DL) algorithms. Image courtesy Abaco Systems.]
These mounting power needs are compounded by harsh operating environments. Massman notes that “these systems must operate in harsh and contested environments, such as high altitudes and extreme temperatures, where power efficiency directly impacts mission endurance.”
Power management trends
Defense contractors are developing solutions to handle increased sensor and processing loads while maintaining strict power constraints. They range from packaging techniques to advanced materials and intelligent power-management systems.
“We are developing high-efficiency power-conversion solutions leveraging GaN [gallium nitride] and SiC [silicon carbide] materials, which provide higher power density and faster switching speeds while reducing thermal losses,” Massman says. “These innovations are particularly beneficial for powering phased-array antennas, which require precise power distribution to multiple digitizers, beamforming ICs, and transceivers.”
Some companies are solving power management challenges through new packaging approaches.
“We’ve begun integrating new power supplies that meet environmental and performance requirements yet are packaged in unique ways to better fit in small form factors,” Donaldson says, pointing to a direct RF small-form-factor module the company has developed that is a fraction of the size of a 3U VPX board.
Analog Devices engineers developed a packaging technique called 3D heterogeneous integration and high-conductivity substrates, which “enhance heat dissipation while maintaining compact system footprints,” Massman says.
Thermal-management considerations
As autonomous platforms pack more processing power into smaller spaces, thermal challenges grow.
“Thermal management is critical for maintaining performance and reliability in unmanned systems, particularly as they integrate power-dense electronics like phased arrays, AI processors, and multichannel RF transceivers,” Massman says.
Defense contractors are employing a range of solutions – and for some, traditional cooling works best.
“When we can, we use the same tried-and-true low-cost solutions we always have – conduction-cooled solid metal frames,” Donaldson says. (Figure 2.)
[Figure 2 | The WILDSTAR SAF1 small-form-factor module may be deployed as a single standalone unit for edge applications close to the sensor and in other tight-envelope environments, or dual-mounted on a 3U OpenVPX baseboard for processing-intensive applications such as electronic warfare (EW) and signals intelligence (SIGINT). Image courtesy Annapolis Micro Systems.]
“Where power density requires it, we use more sophisticated techniques, like heat pipes, vapor chambers, more exotic materials, or liquid,” he adds.
More complex cooling solutions also require more intelligent thermal-management systems. “Adaptive power scaling further optimizes thermal performance by dynamically adjusting power consumption based on sensor activity, RF load, and mission priorities,” ADI’s Massman explains. “These innovations help unmanned platforms maintain consistent phased-array radar performance, AI-driven decision-making, and high-speed communications, even in high-altitude, high-temperature, or contested environments.”
Engineers must keep the surrounding environment in mind when designing these electronics. Once drones get above 25,000 to 30,000 feet, exchanging heat with cooling surfaces gets more difficult.
That means even though the air itself is very cold, it’s difficult in that environment to keep the electronics cool, Littlefield says. “As a result, for extremely high altitudes one must take advantage of other methods to manage heat like using the airframe or fuel tanks as heat sinks, or even actively managing the electronics by turning things off if they are not needed for periods of time. This last approach requires a sophisticated chassis-management mechanism.”
New semiconductor materials
Power efficiency is also enabled by advances in semiconductor materials and fabrication techniques. These developments range from wide-bandgap semiconductors to chiplet architectures.
For example, Analog Devices is using GaN-based power solutions that the company says generate less heat and offer better efficiency compared to silicon-based devices – which reduces the need for active cooling.
“Wide-bandgap semiconductors like GaN and SiC are revolutionizing power solutions by enhancing efficiency, reducing energy losses, and improving thermal performance, which is critical for unmanned systems and phased-array applications,” Massman says. “GaN’s higher switching speeds and lower conduction losses allow for more compact, power-efficient RF power am-plifiers, beamforming ICs, and radar transceivers, significantly improving phased-array performance.” (Figure 3.)
[Figure 3 | An exploded view of the Analog Devices ADSY1100 series, a family of wideband multichannel RF digitizers. Image courtesy Analog Devices.]
Chiplets can help alleviate power challenges that come from high-performance processors and FPGAs. “The latest FPGAs and GPUs are extremely capable but also power-hungry and untargeted,” Donaldson says. “On the other hand, smaller, more modular chiplets can be mixed and matched at a quicker lead time and lower NRE to optimize power efficiency and performance for particular platforms.”
Fischer asserts that the industry is increasingly moving toward chiplet-based architectures. “The future of high-performance computing is moving towards advanced packaging, where the processing, memory, and other critical computing resources are evolving to chiplets or miniaturized building blocks of various functionalities. Regardless of the system function, the main advantage of chiplets for power consumption is the reduction of energy waste through advanced packaging.
“Reducing power consumption isn’t really an option moving forward, so improving efficiency is key,” he adds.
SOSA and open standards
Open architectures like the Sensor Open Systems Architecture, or SOSA, Technical Standard, provide for small form factors and address SWaP challenges while also enabling interoperability and affordability.
“By leveraging SOSA aligned architectures, such as 3U VPX and VNX+, power-management solutions can be modular, allowing for seamless integration of next-generation beamforming ICs, RF transceivers, and AI processors,” Massman explains. “Standardizing power distribution, data interfaces, and thermal management across SOSA [aligned] platforms reduces development time and ensures compatibility with evolving mission needs.”
Still, there are additional considerations when it comes to using open standards in this area. Littlefield says the SOSA approach is useful for larger platforms, but uncrewed systems can be small enough where it’s hard to use standards-based commercial off-the-shelf (COTS) components.
“Fortunately, [the SOSA Consortium] saw this problem coming and started a small-form-factor effort several years ago, resulting in VNX+ (VITA 90) being adopted into the Technical Standard,” Littlefield says. “VNX+ is small enough that many uncrewed systems that in the past couldn’t use COTS due to SWaP constraints can now reap the benefits of [the SOSA approach].”