Exoskeleton tech makes advances via Lockheed Martin, university partnership
NewsSeptember 10, 2018
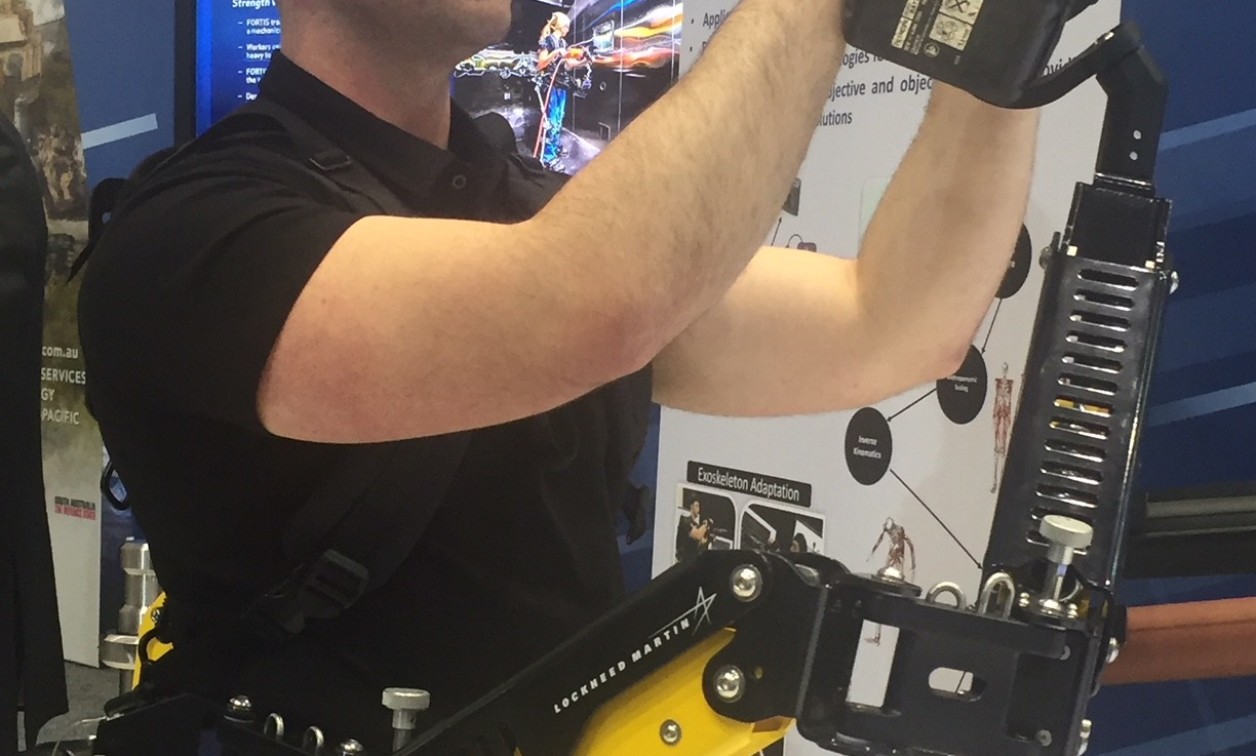
ADELAIDE, Australia. Lockheed Martin Australia and Deakin University?s Institute for Intelligent Systems Research (IISRI) entered into a 12-month research partnership that has resulted in extending the capability of the company's FORTIS Exoskeleton.
The FORTIS is an unpowered, lightweight exoskeleton designed by Lockheed Martin that makes tools weighing up to 36 pounds feel weightless - reducing user fatigue and improving worker safety. Lockheed Martin licensed B-Temia's bionic augmentation technology called Dermoskeleton to incorporate into its exoskeleton program in April 2017.
The IISRI team used biomechanics to test the ergonomic effects of using power tools on the human body by using motion capture obtained from sensors on the arms and shoulders of exoskeleton operators and analyzed by signal processing techniques. Deakin IISRI researchers also designed and 3D-printed new attachments to expand the functionality of the FORTIS Exoskeleton, allowing it to accommodate external loads usually mounted on the back of the human body.
James Heading, business development senior manager, Lockheed Martin Australia, commended the Deakin research team and outlined the inherent challenges associated with exoskeleton research. “Lockheed Martin has a proud history of successfully developing and demonstrating exoskeleton applications that take the work out of many demanding, repetitive tasks,” he says. “Originating from Lockheed Martin’s exoskeleton research to assist soldiers to carry heavy equipment over long distances, the same principles of how the body works and expends energy were applied to exoskeleton development for use in industrial settings.
“The technology supporting the exoskeleton may look simple but developing technologies that are a help and not a hindrance is a deceptively difficult engineering task. No two people are the same, so the exoskeleton needs to be designed to adjust and fit any sized person and accommodate different anthropometry,” Heading adds.
Dr. Hossny, Senior Research Fellow, IISRI at Deakin University, commended the research project, led by Darius Nahavandi as part of his Ph.D. research, for identifying the importance of biomechanic analysis of assistive devices. “The project has accelerated the design-testing loop for designing and tuning exoskeletons. There is often a trade-off to be considered when adopting assistive devices in theworkplace. While assistive devices help channel the load through the skeletal structure of the exoskeleton, our work optimizes the operator’s movement so they are able to cope with increased repetition and indirect loads during motions,” he explained.
Other IISRI researchers involved in the project were Navid Mohajer, Imali Hettiarachchi and Julie Iskander.