Supply-chain headaches
StoryAugust 04, 2021
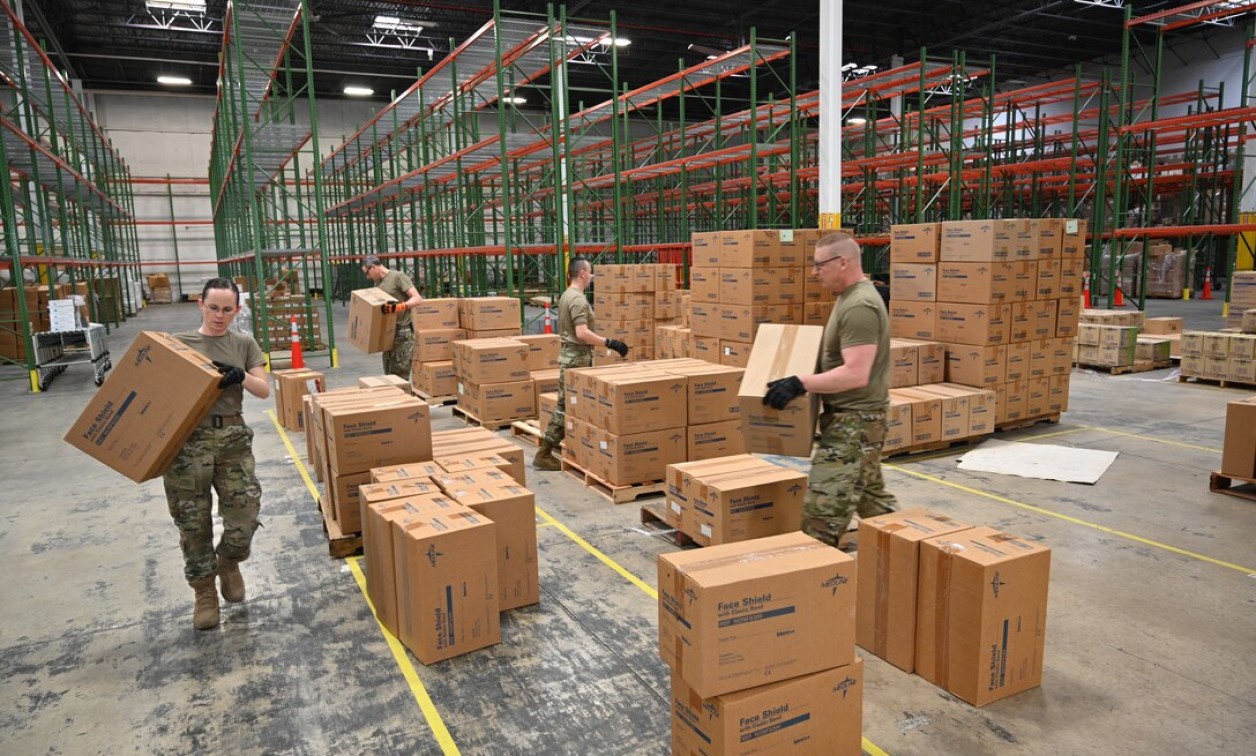
Nearly three decades ago, then-U.S. Department of Defense Secretary William Perry issued a memo dictating the use of commercial off-the-shelf (COTS) technology wherever and whenever possible. In many ways, the edict revolutionized procurement and helped integrate new commercial technology more affordably into defense systems, but it also created supply-chain pain for suppliers that is still felt today.
That pain is named obsolescence and has long been the bane of COTS procurement, as COTS suppliers must juggle the short life cycles of commercial components – think 18 months or less – with the requirements of defense applications for platforms built to last for decades. For example, the B-52 is still flying more than 60 years since it entered service.
COTS suppliers have become expert not at only at ensuring that commercial technology can perform effective and reliably in battlefield environments but adept as wizards at ensuring the same tech will be available five or 10, even 20 to 30 years down the road. Methods for navigating the supply chain madness range from end-of-life (EOL) buys of components to leveraging aftermarket suppliers like Lansdale Semiconductor or Rochester Electronics. The same supply chain sources must also demonstrate trust to not only keep counterfeit components at bay, but also to ensure trust that they will be there year after year.
That obsolescence-management skill is being severely tested these days as the COVID-19 pandemic has highlighted holes in the U.S. supply chain – especially with integrated circuit (IC) manufacturing – as I highlighted in my column in our last issue. In it, I noted that U.S. defense officials are very concerned about increased U.S. funding for domestic semiconductor production in order to reduce our dependence on Taiwanese IC companies.
This current atmosphere is unique, says Jason Wade, president of ZMicro in San Diego. “For some electronic components we are seeing 52-week lead times. Tesla builds factories in less time.”
Overlong electronic-component lead times are affecting all COTS suppliers, including rugged-display manufacturers like Wade and others whom I spoke with for our Industry Spotlight feature on page 36.
“It’s affecting displays, because you have ICs if you have embedded boards in the displays,” says Michael McCormack, president and CEO of CPU Tech in Prescott, Arizona. “Capacitors, resistors, and other components have disappeared out of Taiwan and China. Some manufacturers disappeared off the map in the last couple years. Everything got decimated, pushing lead times out and increasing pricing. Many Taiwanese IC suppliers depend on China for their components. China has placed tremendous geopolitical pressure on these suppliers, so that if they don’t respond right away to a request their supply chain is cut off. We made a decision to eliminate our dependency on China and Taiwan [and] moved our supply chain to more U.S. suppliers.”
Run-of-the-mill inventory shortcomings became gaping holes during the pandemic. “When the pandemic hit everything changed, so the material supply challenge is just a symptom of that bigger picture,” says Steve Motter, vice president, business development, IEE, Inc., in Van Nuys, California. “It’s really impacted manufacturing channels, as they don’t have the inventory at the OEM level as in years past. In many cases these inventories have gone from 100% to zero. We are seeing where distributors are going back to factory lead times. That’s an outcome of the push to have less inventory at the OEMS and at the distributors.”
Glass shortages exist for LCD solutions but the longest waits at the moment are for electronic parts. “The supply shortages we see are mainly for PCB components,” says Ross Hudman, sales and marketing manager, Digital Systems Engineering in Scottsdale, Arizona. “LCDs may have a longer lead time, just north of 24 weeks, but the ones giving us the most headaches are processors and similar components.” These shortages also plague the automotive industry. A PCB may have 1,000 components, but if one of them is delayed 50-70 weeks, it can be quite detrimental to your business.”
For some companies, such shortages could spell huge losses or even bankruptcy, but for COTS suppliers it’s a new facet to a problem they’ve actually managed for decades.
“Being a long-time military supplier, we are used to obsolescence challenges and are able to manage it well,” Hudman says. “Companies not used to this are finding the shortages difficult to navigate.”
COTS military suppliers have an advantage in this situation, as they are adept at adapting. “One must have multiple sources of supply – six to 12 instead of two or three,” McCormack notes. “The EOL management process we provide to people gives us an advantage.”
“As a supplier of military systems that leverage commercial components, we are used to managing the supply chain and obsolescence challenges that come with commercial technology,” Wade says. “That leaves us better prepared than others.”