Small but mighty: challenges in military power supply design
StoryNovember 16, 2020
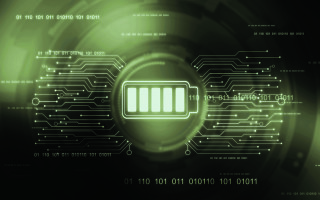
Shrink it down but bolster the processing power. Engineer it so it’s light enough to fly on an airborne platform but never overheats. These are the contradicting design challenges manufacturers still face when building power supplies for military applications. Innovations in the field are ongoing, and both standardization consortia and the U.S. Department of Defense (DoD) are starting to phase out antiquated power supplies.
Edge technologies like artificial intelligence (AI) and machine learning (ML) capabilities are becoming increasingly prevalent in modern military technology; with this new tech comes immense requirements for more processing power. End users are looking toward power supplies that can operate under such stringent conditions while being optimized for size, weight, and power (SWaP) constraints.
The overarching need for such optimization has hindered what could be defined as any groundbreaking modernization in military power supplies as of late but has conversely bolstered both the manufacturers’ and end users’ desire for standardization. Encouraging competition in the industry would be one benefit, while others could include affordability and overall modularity in design.
To address these enveloping obstacles, companies like Vicor (Andover, Massachusetts), Behlman Electronics (Hauppage, New York), and North Atlantic Industries (Bohemia, New York) are cognizant of the idea that while the ability to customize is very important, it doesn’t necessarily mean that standards like VITA [VMEbus International Trade Association] and VPX won’t support a flexible power supply. According to these manufacturers, an easily modifiable design is still achievable through standardization despite the end goal of limiting user-defined options.
With many manufacturers speaking to the gradual decline in demand for VME and CompactPCI supplies powering anything but legacy systems, it appears such widespread efforts for standardization are gaining traction. The result could be power supplies modular enough to finally make headway in terms of power efficiency innovation.
New era of standardization
Industry professionals, however, do still admit that VME could actually be around forever. There just might be a point where the first-generation power supplies could also utilize some of the advantages of standardization down the line.
“We do see some demand for people who are upgrading VME systems, but since VME had no standard size or shape, we try and encourage customers who are upgrading their systems to use a VPX power supply,” says Jerry Hovdestad, director of COTS (commercial off-the-shelf) engineering at Behlman Electronics. “They’re essentially the same mechanical configuration, and now they get the benefit of standardization. In the old VME systems, you would just put a box in the system someplace that provided the voltages you need.”
Consequently, it seems that the future for VME will be that some legacy systems are going to stay the same, with the same power they had in the past, and some could be upgraded when undergoing a refresh of the systems to standardize the power supply. Other manufacturers are looking at it in the same light.
“We do not see much demand on new platforms for VME or Compact PCI,” says Rob Russell, vice president of product marketing at Vicor. “But there is a sizable installed base that will need servicing for quite a while.”
For now, VPX and VITA are at the forefront of power supply technology. The Sensor Open Systems Architecture (SOSA) Consortium acts as a primary influence in this effort and is advocating for military power supplies to be as standard as possible with as few user-defined options as can be achieved.
“The SOSA consortium is developing the standard to enable multisourcing, unlike the current VPX supplies,” Russell says. “Although the preliminary SOSA standards call for fewer outputs with significantly more current required from the 12-volt output, the actual power requirements being discussed are very similar to those in the VITA 62 standard. Vicor has developments in progress to adapt its VITA 62 technology and create a SOSA family of supplies.” (Figure 1.)
[Figure 1 | Vicor’s VITA 62 power supplies are MIL-COTS power supplies that are designed for 3U and 6U OpenVPX systems.]
This 12-volt heavy configuration has been incorporated by VITA 62 and is planned to be adopted by SOSA, according to Hovdestad, a chairman of the VITA 62 subcommittee, with the intent to eliminate much of the option capability in other configurations. In hopes of being adopted by as many platforms as possible, the 12-volt power supply is intended to meet approximately 80% of military requirements.
“There will always be some customization, there will always be some legacy power supplies out there with special requirements, but they want to get the whole industry to move in the direction of this standardization,” Hovdestad says. “It’s being adopted for air, ground, and shipboard supplies. NAVAIR [Naval Air Systems], the Air Force, and the Army have decided to attempt to complete these standardizations so they can get the most flexibility out of their boxes. There are manufacturers out there that now have boxes that can be configured for six or seven different systems with the same cards by just reprogramming the box, so they are certainly seeing some of the benefits of standardization.”
As efforts for standardization gain ground, so do modernization efforts in defense technology. Implementing cross-domain, edge-computing capabilities to enhance the U.S. military’s battlefield presence is necessary to compete with near-peer adversaries but requires levels of processing power that make SWaP optimization a challenge for manufacturers.
SWaP constraints still define power-supply advancements
Few platforms find it as difficult to adhere to SWaP restraints as do airborne platforms. Not only do these systems have to operate in limited space, but they must also fly and remain aloft. Acknowledging that this caveat extends beyond jets and helicopters to unmanned aerial vehicles (UAVs) has been a prevalent discussion among power-supply manufacturers.
“One trend has remained the same: increasing power density and efficiency to meet demanding SWaP requirements,” Russell says. “Whether it is a retrofit or a brand-new platform, they need space and lower weight to add new features. Additionally, we are also seeing applications, such as tethered UAVs, where high-voltage power delivery networks yield major SWaP benefits. The higher the voltage for the tether, the lower the current, which allows thinner, lower-weight tethers. This, in turn, enables higher UAV altitudes, increased functionality, and bigger payloads.”
SWaP constraints, however, bolster the argument for freedom of customization in military power supplies. For a manufacturer to have a keen understanding of specific performance requirements could lead to a power supply design tailored to its respective platform.
“Engineering teams developing military products and platforms have several challenges that a custom power solution can solve,” Russell says. “The main challenge for many aerospace and defense customers is that they do not have the bandwidth to conceive and develop a power solution that will enable them to meet their SWaP and TTM (time-to-market) requirements. Understanding unique military performance requirements and being able to deploy proven modular designs that will pass qualification with a high degree of confidence is essential.”
However, edge technologies and the immense processing power required by AI- and ML-powered systems continue to make SWaP optimization in military power supplies a difficult feat. Paralleling cards to provide higher power with less weight, technology leveraged from commercial processors, and higher voltages are tactics being researched by manufacturers in hopes of mitigating the huge power gulps seen in such systems.
“One major thing to keep in mind is the ‘power-hungry’ systems,” says Lou Garofolo, product manager, power division at North Atlantic Industries (NAI). “One thing which NAI has been doing is looking for the best ways to pack more power into compact, edge-cooled designs. We are constantly looking for the latest technologies available for power components. The added challenge is that these systems typically are required to run under extreme temperatures under full power.” (Figure 2.)
[Figure 2 | NAI’s high-power 6U product, the VPX56H2, is capable of 1,400 watts with capability for the power expected with the new SOSA requirements of a 12-volt-centric output with a 3.3-volt (aux) output.]
The aforementioned 12-volt-centric systems are in development in hopes of mitigating some of the complications presented by power hungry systems. They are designed for the end user to get more power out of a card to eventually power more electronics, but with that comes heat.
Edge technologies are hotter than ever
“The requirement for 12-volt high power is being driven by the requirements for immense processing power,” Garofolo says. “An advantage to having a heavy 12-volt output without the other VITA outputs is that the power supply becomes more efficient, which is especially important when running at higher power levels. Programmability and communication are also essential in these ‘edge’ technologies.”
Power supply manufacturers are optimistic about the new processing capabilities the 12-volt supply could allow for, but they are already taking into consideration the additional aspects of a power supply that will need to catch up. Most of these challenges involve heat and efficient thermal dissipation.
“We’re investigating cooling, or getting more power in processors and in power supplies,” Hovdestad says. “The better we can cool things, the smaller we can make them. There is some movement toward VNX or small form-factor power supplies for making things smaller and lighter and more efficient. But you have to take into account the ability to cool. There are new air flow systems and liquid flow systems that will allow the power supplies to actually shrink down, deliver more power, or both. The better you can cool it, a 1,000-watt supply may become a 4,000-watt supply if you can cool it properly.” (Figure 3.)
[Figure 3 | Behlman Electronic’s VPXtra 700D-IQI power supply has no minimum load requirement and has overvoltage and short circuit protection as well as over current and thermal protection.]
There is yet to be a silver-bullet technology for the ideal military power supply, but manufacturers seem to agree that innovative thermal management can get them pretty close. Despite there still being a prominent need for such cooling properties, bus voltages keep increasing because processing power is mounting as well.
“Multiple applications will require increased bus voltages, which drive the need for new converter topologies and power module packaging to meet SWaP demands,” Russell says. “Conversion and regulation from 28 volts, 48 volts, 270 volts, up to 800 volts or even higher will be needed to meet the needs of tethered UAV applications, high-voltage battery power sources for electric and hybrid vehicles, and other high-performance power systems.”
With progress, the cycle continues. When certain power-supply novelties – like advancements in voltages – contradict other technical transformations – like those in the realm of cooling – manufacturers are left only with their engineering creativity to bring to market the next great military power supply. For some companies, that could mean developing a supply with the ability to tell itself when to cool down.
Making power supplies smarter
Like many military-technology companies, manufacturers of power supplies for military use are looking to the commercial world for inspiration in making more intelligent parts. With the ever-mounting amounts of data that commercial technology is constantly tasked with sifting through, these companies are finding that the answer to doing so efficiently could be traced back to the power supplies behind the processing.
“Power delivery and power efficiency have become some of the largest concerns in high-performance computing and AI applications,” Russell says. “The commercial industry has witnessed a dramatic increase in power consumed by processors, with the advent of ASICs [application-specific integrated circuits] and GPUs [general-processing units] processing complex AI workloads. In most cases, power delivery is now the limiting factor in computing performance as new CPUs draw ever-increasing currents.”
Russell goes on to assert that he believes AI will drive change in the advanced power-solutions arena due to their paramount need for efficient, high-current, and power-dense converters that he says have yet to be engineered in the defense industry.
There lies the rub: Taking inspiration from the commercial industry is the easy part. Designing a power supply that must also operate in the extremely contested environments seen in the battle theater presents its own set of challenges. Engineers at Behlman are working to add intelligence to military power supplies in an effort to reduce the manpower required to maintain a power supply.
“One of our main emphases is working on the intelligence of the power supply and intelligent systems so that they can make use of the information provided by the power supply,” Hovdestad says. “You can tell a lot about the performance of a system by getting up to date, real-time information on power being consumed. These systems can be very smart. They can predict the health of the system, possibly the fault about to happen, so we are working on the intelligence of the power supply.”
Needless to say, military power supply manufacturers’ efforts in standardization, cooling, and implementing intelligence are changing the market. The hope is that in the near future military users will be able to switch power supplies in a weapons system without having to spend millions of dollars on reprogramming an entire system.