Expanding the horizons of RF connector designs for harsh military environments
StoryOctober 16, 2023
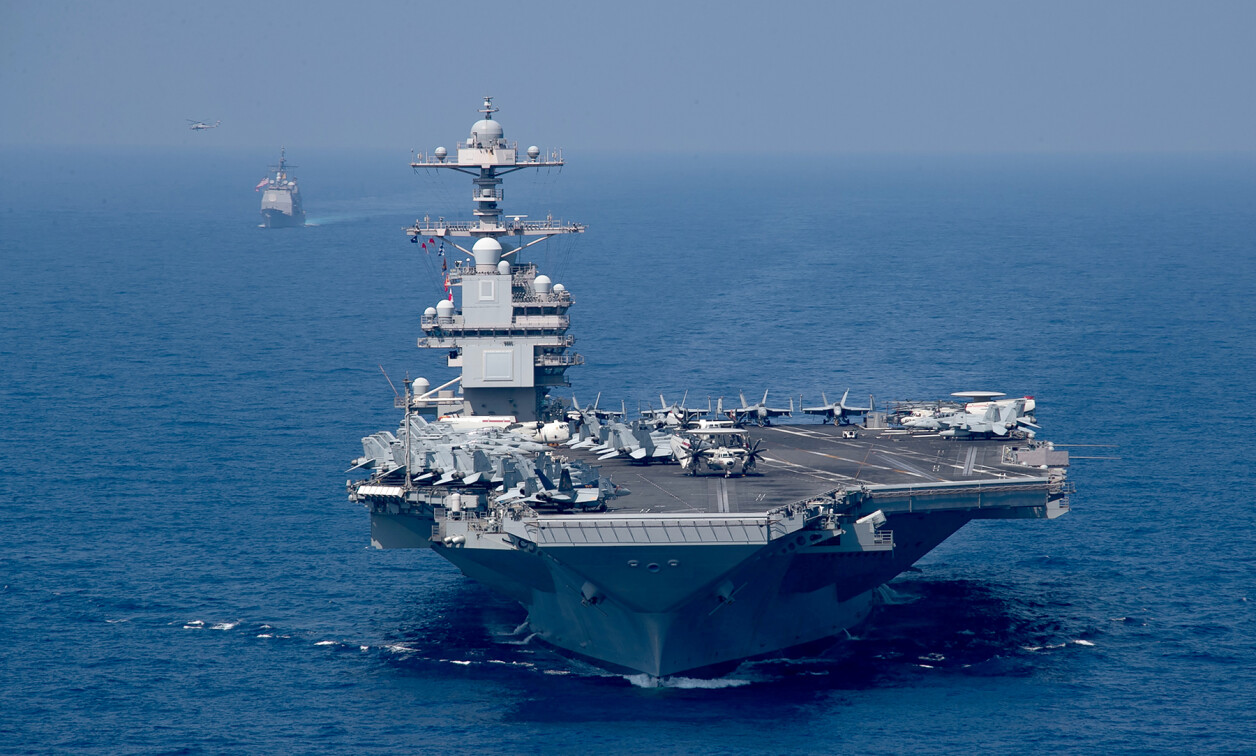
In the realm of aerospace and defense, robust and reliable radio-frequency (RF) systems for mission-critical applications are critically important. They serve as the backbone for a range of vital technologies, including satellite communication, electronic warfare, intelligence, missile guidance, radar, hypersonic systems, and more. Meeting the high demands of these advanced technologies and ensuring they perform without fail in variable and extreme environments requires continuous evolution of hardware components and interconnect solutions.
The effectiveness of aerospace and defense radio-frequency (RF) systems ultimately hinges on the integrity of the hardware components and how they come together. While some installations call for fairly standard products, others demand custom-designed solutions due to unique requirements. In the dynamic landscape of aerospace and defense, the need for high-performance connectors capable of withstanding harsh conditions, intense vibration, and temperature extremes while offering consistent performance is on the rise.
However, legacy connector designs like SMP/SMPM [sub-miniature push-on/sub-miniature push-on micro] connectors no longer fulfill evolving technology demands. Their susceptibility to electromagnetic interference (EMI) and electromagnetic compatibility (EMC), along with their lack of environmental sealing and potential to come apart upon an impact such as a hard landing, have spurred innovative RF interconnect designs to address these challenges more effectively.
These advancements in connector designs are also powering a new class of modern aerospace and defense applications that consistently push the boundaries of power handling and performance. These new connector types, engineered for high peak power at altitude, are set to play a pivotal role in the next generation of military communication systems designed for harsh environments.
These advanced technologies are ushering in a new era of consistently high performance in demanding, variable, and extremely harsh environments and the multifaceted connectivity RF interconnect designs required to handle them.
Embracing standards
An example of the upshift in connectors is the emergence of smaller-sized, O-ring sealed connector solutions that outperform their SMP/SMPM predecessors in several aspects, enabling improved shielding, environmental protection, and mechanical retention. This class includes recently introduced locking miniature push-on and locking miniature blind mate connectors created to address EMI issues for applications that require an environmentally sealed and shielded connector. The locking miniature push-on is also ideal for high-vibration environments such as a carrier landing, weapons launch, or similar harsh platform issues.
This modern class of connectors retains the small form factor of SMPs but adds improved shielding, environmental, and power capabilities, spanning frequencies from DC to 60 GHz. The mating part covers the connector’s slots to prevent signal leakage, which helps them to meet standards regarding performance issues from EMI and EMC interference as well as liquid and salt ingress. In addition, their sealed, rugged design equips them to better withstand harsh conditions and severe environments. At the same time, the overlapping insulators cut off a direct path to the ground from the center conductor to the outer shield, enabling higher-voltage functionality.
In addition, the connectors also feature a latching mechanism to improve mating retention, making it a more suitable choice over options that use threaded bodies; a visual verification feature with red (unlocked) and green (locked) color coding assures connectors are fully mated and locked. Finally, the locking blind-mate version features an additional outer sleeve to provide fully protected tines for blind-mate applications.
Mounting demand for connectors
As military avionics applications continue to advance, the demand for new connector solutions for high-density, high-power applications in harsh environments also continues to grow. To meet these new demands, connector designs like locking miniature push-on and blind mate connectors are evolving to accommodate higher continuous wave power and frequencies above 18 GHz.
These new connector types are aimed at maintaining reliable communication systems in such applications as densely packaged signal intelligence, electronics intelligence, and electronic warfare (EW) systems operating in harsh environments. Connectors retain the overlapping design, environmental seal, and improved EMI performance but build on the family’s features to include new capabilities that enable them to handle high power at altitude.
Moving beyond single interconnects, as the number of boxes and highly densified antennas on aircraft require more cables and contacts per square inch, the new connectors designs described above can be integrated into multiported versions that eliminate traditional coupling nut schemes, offering improved space utilization and operational efficiency. In this configuration, the same interfaces are mounted into male and female shells as bulkhead disconnects, enabling significantly higher densities on the interface.
Navigating multifaceted connectivity challenges
The combination of advanced signal processing and sensing capabilities along with integrated hardware enables critical insights to be obtained from extremely large data sets, empowering military aircraft with more accurate and comprehensive systems while enhancing functionality and safety. As this type of innovation accelerates, connectors must now be able to handle higher frequencies, faster data transmission speeds, and increased power demands in addition to the harsh operating environments of their predecessors.
For example, current systems operate in the 23 to 60 GHz range and beyond, enabling faster target detection and more accurate tracking. These increasing frequency ranges also mean faster data transmission rates are needed to process incoming signals. Onboard processors filter and analyze this data quickly to detect threats and enable a fast response. Printed circuit boards (PCBs) play a crucial role in establishing quick connections between components or between PCBs themselves.
Furthermore, as aircraft push the limits of speed and altitude, connectors must be able to handle higher power while maintaining a delicate balance between weight, size, and power transmission capabilities. For example, consider the radar processor box contained within a jet’s airframe. This box orchestrates a symphony of technologies, including phased array radar systems that use multiple small antennas to steer radar beams electronically. As boundaries are pushed even further in hypersonic flight, emerging connector designs equipped with materials like boron nitride dielectrics that can withstand extreme temperatures are being introduced.
Finally, systems increasingly incorporate integrated antenna elements into the aircraft structure rather than large standalone antennas. This requires many small antennas and connections in a confined space. High-density connectors are aimed at these and other applications. (Figure 1, below.)
Examples include the Times locking connector (TLC, a trademarked product), built around a 40-mil line size design to handle higher transmit powers on an aircraft. This part leverages dielectric materials to enhance its thermal dissipation capabilities, improved by using Fluoroloy-H instead of Teflon; Fluoroloy-H dielectrics have eight times the thermal dissipation of Teflon and are specifically optimized for dissipating high CW power at any altitude. The TLC is aimed at use in applications up to 23 GHz. If the TLC connector design is too large for a specific system, the Times locking push-on connector (TLPC, a trademarked product) can handle high power levels at a much smaller size. It has a 30-mil line size and comes in multiple versions, including a card edge and is meant to thread through the wall of a box or solder to the ground plane and the center pin or the trace on the board for applications requiring a frequency range of up to 32 GHz.
[Figure 1 ǀ High-density connectors are able to handle antenna elements that are integrated into the aircraft structure rather than large standalone antennas.]
Understanding the assignment
RF suppliers who have deep engineering expertise and a trusted heritage of development in mission-critical industries are important when designing applications requiring the highest-performance connectors for the harshest environments. In addition, the company must understand not only the material technologies but the actual applications – the aircraft, environment, and physics involved.
Because military avionics systems are highly complex and do not often use a standard solution, the RF supplier should be available for the technical team to ask questions to understand the application’s unique needs and design an optimized solution, ultimately arriving at better electrical, mechanical, and environmental performance.
To ensure the best possible performance for demanding military avionics applications as expediently and cost-effectively as possible, consider the following when choosing the optimal RF interconnect supplier:
- Qualifications and heritage: Many suppliers offer a good list of standard capabilities, but military avionics requirements are unique. Look for partners with a wealth of military and defense experience to help develop RF systems that can withstand the rigorous military avionics environment, deliver reliable performance, and adhere to stringent safety requirements.
- Dedicated technical experts: The supplier should understand the particular application’s electrical and mechanical trade-offs.
- The breadth of products: To select the right materials, choose from multiple cable constructions, various connector designs (low power, high power, etc.), and assembly techniques from the same supplier. Many technical standards must be met for products deployed in harsh military environments, such as using only acceptable materials or military-spec constructions. There is, however, no standard for how to apply these materials to construct an RF solution that is reliable time after time.
- Manufacturing execution: Ideally, an RF supplier has all the technology and products and understands how to assemble them into a final product. Moreover, the supplier’s manufacturing operations must be high-level: Cleanroom manufacturing capabilities are essential, while traceability is also vital in managing all the parts that make complicated assemblies, as is the ability to source reliably and on time.
Ever-changing avionics needs
To meet the ever-changing needs of military avionics systems, evolving connector designs offer significant footprint reductions in single-mount or multiported versions that support higher densities and power thresholds of modern applications while solving the EMI issues and environmental issues of the previous generation of RF connectors. These advanced technologies are ushering in a new era of consistently high performance in demanding, variable, and extremely harsh environments.
Cameron Foley-Molovinsky is an applications engineer at Times Microwave Systems; he also has worked at Times Microwave Systems as a manufacturing engineer, engineering technician, and engineering intern. Cameron earned a degree from Arizona State University in electrical systems engineering, with a secondary focus in environmental resource management.
Times Microwave Systems • https://timesmicrowave.com/