Navigating the heat: Advanced cooling strategies for high-performance military computing
StoryNovember 26, 2024
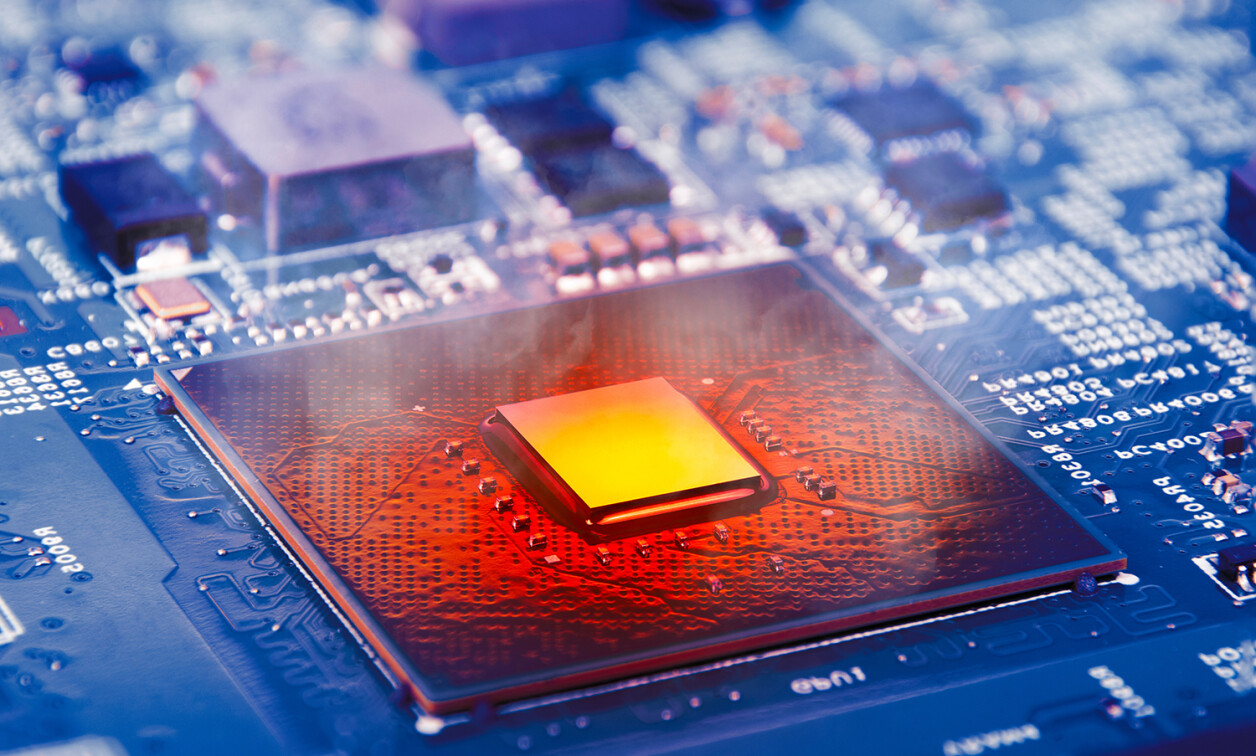
Advanced computing is revolutionizing defense platforms across all domains. Modern C5ISR [command, control, communications, computers, cyber, intelligence, surveillance, and reconnaissance] and the tactical advantages it brings to the battlespace would not exist without the rapid advancement of compute hardware. However, the ability to deploy this hardware in rugged and extreme edge environments depends heavily on the effectiveness and reliability of cooling systems. Preferred methods of cooling like conduction and forced air are often insufficient to meet the thermal needs of these high-performance computers. Systems designers should be aware of both the advantages and challenges associated with next-generation cooling such as air flow-through and liquid flow-through. While each adds some additional complexity and risk to the system they are cooling, they bring enormous advantages in terms of cooling performance. Without implementing these higher-capacity cooling mechanisms, systems in the near future will not be able to take advantage of the latest processing hardware for critical edge applications.
It is hard to overstate the rapid pace at which processing technology has changed in the past five years. Breakthroughs in machine learning and artificial intelligence (AI and ML), coupled with the development and scaling of advanced compute hardware like graphics processing units (GPUs), have transformed computing across almost every industry. While the broad adoption of GPUs enables rapid technological advancements, it also creates significant new demands and challenges. One of the largest obstacles to overcome is managing the power consumption of high-performance chipsets and the resulting heat generated by the processors.
Power consumption of GPUs has increased dramatically since the primary use case for GPU processing switched from rendering graphics to handling AI workloads. As recently as 2021 the highest power consumption of any NVIDIA GPU accelerator was 300 watts (W), with most single processors operating in the 100 W to 250 W range. Their latest chipset, the Blackwell B200, has a max power consumption of 1,200 W per chip. This massive increase in power consumption requires new approaches to electronics cooling from the data center to the edge. (Figure 1.)
[Figure 1 ǀ A thermal-analysis image demonstrates how heat builds up at the processor location; it also shows the importance of ensuring the PCB has the right thermal-management tools to protect the processor from overheating.]
Cooling high-performance electronics
Until recently high-performance GPUs like those from NVIDIA, AMD, and Intel were found primarily in data centers and research labs. These purpose-built facilities are designed with cooling in mind, and typically use a combination of cold room air conditioners (CRACs), chillers, and targeted liquid cooling to dissipate heat generated by electronics. Air cooling is often preferred, as it is cheaper and less complex, but as power consumption increases air cooling is often insufficient to handle the heat generated by high-density electronics racks.
More and more data centers are adopting air-to-liquid heat exchangers (Fig-ure 2) or direct liquid cooling as their primary cooling method. Liquid cooling has many advantages over air cooling; it is more efficient than air, produces less noise, and allows for greater electronics density by eliminating the space required for large heatsinks and sufficient air flow to cool them. However, these systems are often more expensive than air cooling, more complex and harder to maintain, and carry the risk of coolant leaks.
[Figure 2 ǀ This air-to-liquid cooling image shows how heat is pushed out of a cabinet housing electronics by way of cold air pushing warm air down out to the return water hose.]
As high-performance computing moves out of the data center and to the edge, especially in aerospace and defense, the challenges associated with cooling become more complex. Many issues exist at the edge that aren’t present in the data center, including environmental extremes, rigorous SWaP requirements, shock, vibration, and motion profiles not encountered in climate-controlled, stationary data center applications. In addition, the critical nature of aerospace and defense applications means systems cannot fail, even when subjected to significant stress. Managing thermal load in such extreme applications is a major challenge for system designers. Thankfully, the VITA 48 standard provides multiple options for cooling rugged embedded electronics.
VITA: multiple options for beating the heat
VITA 48 is a standard developed by the VMEbus International Trade Association (VITA) that defines mechanical specifications for ruggedized systems, particularly focusing on cooling methods for embedded systems used in harsh environments. It encompasses a variety of cooling techniques tailored to support high-performance electronics, such as military and aerospace systems, where managing heat dissipation is critical.
Key cooling methods outlined in VITA 48 include conduction, forced air, air flow-through, and liquid flow-through cooling. Each is briefly described below. While cooling capacity is given here as a general reference, please note that actual cooling performance can vary greatly depending on system design and environmental factors.
Conduction Cooling (VITA 48.2)
- Method: Transfers heat directly from electronic components to the system’s enclosure, typically through heat frames or wedge-locks.
- Usage: Effective in environments where airflow or liquid cooling is not feasible, such as sealed or rugged systems used in military or space applications.
- Advantages: No reliance on moving parts like fans; highly durable and suited for shock and vibration-heavy environments.
- Cooling capacity: Approximately 80 W to 100 W per slot
- Factors influencing capacity: Thermal interface materials, efficiency of heat conduction paths, and the thermal conductivity of the enclosure play a significant role.
Forced Air Cooling (VITA 48.1)
- Method: Air is circulated over modules or a heatsink using fans, without exposing the electronics directly to the external environment.
- Usage: Effective in rugged, sealed systems where it’s important to protect electronics from dust, moisture, or contaminants, while still benefiting from air cooling.
- Advantages: Simple and cost-effective; fans can easily be added to increase cooling capacity.
- Cooling capacity: Approximately 120 W to 180 W per slot
- Factors influencing capacity: Airflow velocity, fan efficiency, ambient air temperature, and heatsink design.
Air Flow-Through (AFT) Cooling (VITA 48.5, VITA 48.8)
- Method: Air is directed through a channel or cavity within the modules to cool internal components directly.
- Usage: Used in systems where internal airflow is possible, such as those deployed in less extreme environments or where higher levels of heat dissipation are required.
- Advantages: Higher cooling efficiency than conduction and traditional forced air, resistance through card-loks and chassis less important.
- Cooling capacity: Approximately 200 W per slot, depending on airflow rates and the system’s thermal design.
- Factors influencing capacity: Sealed airflow paths, air channel design, and ambient air temperature.
Liquid Flow-Through (LFT) Cooling (VITA 48.4)
- Method: Liquid coolant is circulated through a cold plate or channels in the module, which draws heat away from the components.
- Usage: Suitable for systems requiring very high levels of heat dissipation, such as high-power computing or signal processing applications.
- Advantages: Provides superior heat dissipation compared to air or conduction cooling; ideal for extremely high-performance systems.
- Cooling capacity: Approximately 300-plus W per slot.
- Factors influencing capacity: Coolant type (e.g., water/glycol, dielectric fluids), flow rate, and cold plate channel design.
Each cooling method in VITA 48 is tailored to specific operating environments and system requirements, balancing factors like environmental sealing, heat dissipation needs, and mechanical hardening.
An additional benefit of designing VITA 48 compliant cooling solutions is that VITA 48 is one of several open standards integrated into the Sensor Open System Architecture, or SOSA, Technical Standard, which is used to establish command, control, communications, computers, cyber, intelligence, surveillance, and reconnaissance (C5ISR) systems guidelines. The alignment between VITA 48 and SOSA supports the creation of rugged, high-performance systems that are modular, interoperable, and thermally optimized for harsh environments.
VITA 48’s cooling and mechanical standards provide the critical thermal-management infrastructure that SOSA systems rely on to meet performance requirements in military and aerospace applications. By utilizing VITA 48 cooling methods, system designers can create more versatile, efficient, and upgradable systems.
Matthew Tarney is the Global Vertical Growth Leader for Aerospace & Defense at nVent SCHROFF. In this role he is focused heavily on finding solutions to the thermal challenges facing electronics in the aerospace and defense space. Readers may email the author at Matthew.Tarney@nvent.com.
nVent SCHROFF https://schroff.nvent.com/en-us/