Bringing the benefits of GCIA to next-generation ground vehicles
StoryMay 15, 2023
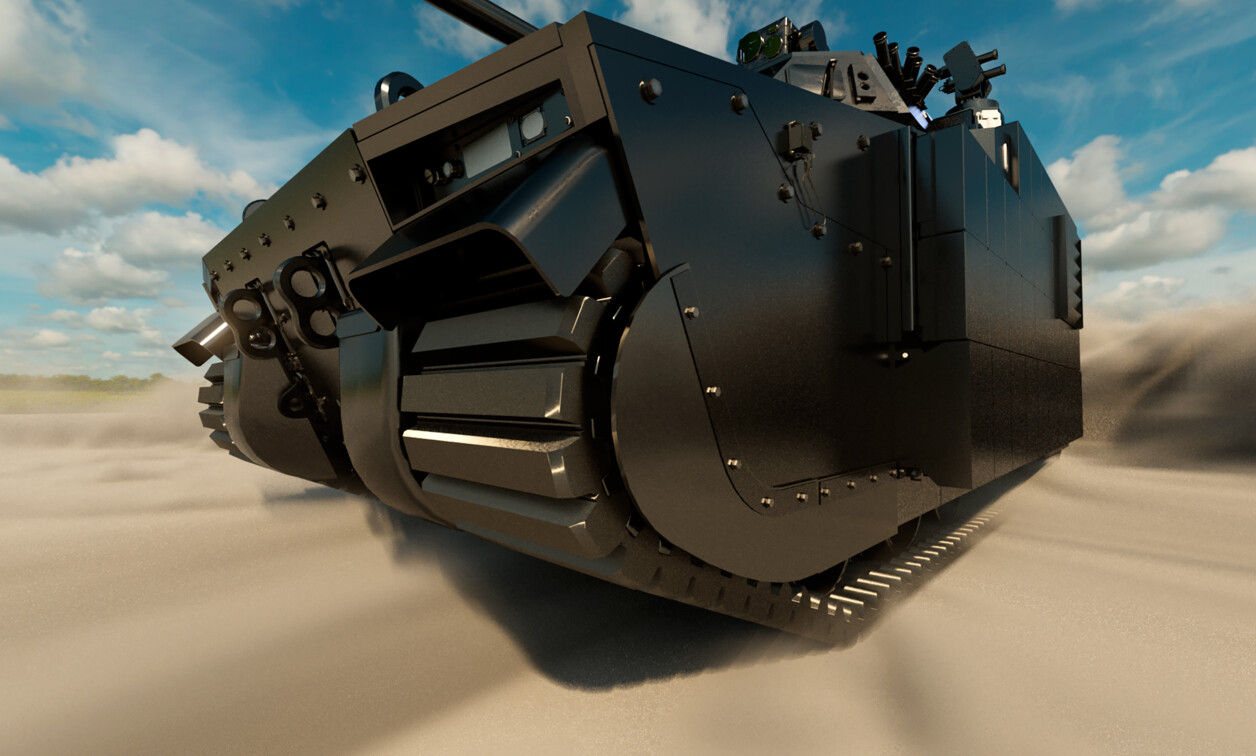
The partnership between Curtiss-Wright and BAE Systems to develop a standardized Modular Open System Approach (MOSA) open architecture for next-generation ground vehicles is an example of how the benefits of MOSA-aligned open standards can be leveraged to deliver new capabilities to next-generation ground vehicles, such as the U.S. Army’s Optionally Manned Fighting Vehicle (OMFV).
Technological change is driving a new generation of ground combat vehicles, as seen by the U.S. Army’s Optionally Manned Fighting Vehicle (OMFV) competition. Through the OMFV competition, the Army is seeking a new infantry fighting vehicle that is agile, lethal, and survivable while also ready to deploy today’s and tomorrow’s most advanced technology and support tomorrow’s emerging capabilities.
Modular Open Systems Approach (MOSA)-aligned solutions are critical for enabling technology on ground vehicles to be rapidly refreshed and new capabilities quickly fielded to meet emerging threats on the battlefield. A vehicle designed with this level of flexibility can consistently meet and exceed the Army’s specific agility, lethality, and survivability goals. MOSA builds in the room to grow to match the Army’s needs and can be easily upgraded and adapted to remain dominant in the fight.
Key Army initiatives – such as Project Convergence, which led to the creation of standards like Ground Combat Systems (GCS) Common Infrastructure Architecture (GCIA) and CMOSS Mounted Form Factor (CMFF) – have been part of the Curtiss-Wright mission. It has also been directly involved in the development of many of the foundational standards referenced in GCIA, such as OpenVPX, SOSA, VICTORY [Vehicular Integration for C4ISR/EW Interoperability], MORA [Modular Open RF Architecture], and CMOSS [C5ISR Modular Open Suite of Standards]. GCIA is helping to move the next-generation combat vehicle away from traditional stovepiped and purpose-built electronics and toward a standardized core infrastructure that can host all of the capabilities needed for OMFV.
The GCIA standard
The GCIA standard defines the requirements for a network computing infrastructure that can host all of the vehicle’s required functions and enables different sensors and effectors to be easily integrated and plugged into that core infrastructure over time. The use of a GCIA infrastructure eases integration on a specific platform and facilitates integration and data movement between platforms. GCIA delivers numerous benefits, including portability of technology and rapid incorporation of new technology.
It builds on existing standards such as the Sensor Open Systems Architecture (SOSA) Technical Standard and the OpenVPX hardware standard that defines the rugged modules called out in SOSA. By specifying rugged processing, networking, I/O, and graphics modules aligned to the SOSA profiles and built using the OpenVPX modules called out in SOSA, ground vehicles are increasingly moving to a MOSA-based GCIA compliant architecture.
The MOSA system elements included in the GCIA architecture include line-replaceable modules (LRM), line-replaceable units (LRU), chassis, fully integrated systems, and the scheme of connectivity. In addition, the U.S. Army’s Standardized A-Kit/Vehicle Envelope (SAVE) – a new physical size, weight, and power (SWaP) and connector standard for fielding new C5ISR [Command, Control, Computers, Communications, Cyber, Intelligence, Surveillance and Reconnaissance] capabilities – can be leveraged to speed and simplify the installation of CMFF systems in Army vehicles by regularizing the size, shape, and physical interfaces (RF, data, power, etc.) for mounting those types of systems. SAVE joins the CMOSS standards – such as VICTORY, MORA, and OpenVPX – already called out by the GCIA framework, but it covers only the purely physical elements, instead of defining how data flows between the systems integrated on a vehicle.
Delivering key MOSA assets
A GCIA implementation delivers on key MOSA benefits, including the ability to quickly react to evolving threats, easily upgrade systems, and reduce vendor lock to lower costs and drive interoperability. In addition, the standard addresses failure resiliency, because the GCIA system infrastructure uses a distributed network with no single point of failure.
The ability to move applications and functions using distributed network resources to any spot in the vehicle will provide an unprecedented new level of fault resiliency compared to today’s vehicle architectures, in which there is very little built-in redundancy. A distributed network architecture enables multiple different functions to be hosted in the same chassis or located in different places on a vehicle, since they are all connected over the GCIA internal vehicle network (IVN) with data transported using well-defined standards such as VICTORY. (Figure 1.)
[Figure 1 | An eight-slot, user integration-ready powered enclosure uses natural convection cooling and can reduce the work of CMOSS/SOSA Technical Standard 1.0 system development.]
GCIA defines how the network moves and shares data to support all the resources needed to host the different functions on a ground combat vehicle. For example, GCIA defines a version of Ethernet that supports TSN [time-sensitive network] standards for safety-critical data movement on the standard core network. The GCIA network can accommodate very low latency paths while providing determinism. Diverse capabilities – such as fire control, targeting, 360° situational awareness, and vehicle-protection systems – can all be hosted by the GCIA-defined infrastructure, which minimizes or eliminates the need for specialized hardware.
Today, new ground-vehicle capabilities are typically hosted in their own discrete boxes, all of which host their own internal computers and require a space claim on an already-crowded vehicle. Each box will usually have its own software, which also needs to be able to communicate with the next layer of software on the vehicle network. All of this has to be qualified, which takes a long time to do and adds program risk. GCIA helps to mitigate risk. While it looks to the SOSA Technical Standard for system profile definitions and VITA hardware standards, GCIA limits their approved use to only a handful of SOSA profiles and a narrow subset of hardware standards.
These constraints force designers to build from a much-smaller set of building blocks right from the get-go, which will greatly reduce the time required to field new technology and tech refreshes in ground-combat vehicles. GCIA focuses on the requirements for enabling a core compute networked infrastructure that will enable a system designer to simply “plug in” all desired capabilities. For example, it directs the use of specific processing and software, and defines the types of displays (dumb versus smart) and security (multilevel security boxes versus single-level boxes).
System designers can use the specified building blocks to develop their software on the very same hardware platform that all other GCIA compliant suppliers are using. That means solutions developed for GCIA-based applications will be transportable between different hardware elements, not just within the vehicle itself, but also from platform to platform and from compute instance to compute instance.
GCIA represents a paradigm shift on how to establish a next-generation vehicle architecture by defining an overall integrated solution. The standard will play a major role in bringing the many advantages of MOSA to next-generation ground vehicles such as OMFV. Such open architecture/distributed network-based combat vehicles are expected to meet and exceed the Army’s requirements now and for years to come.
Jacob Sealander is Chief Architect, C5ISR Systems, for Curtiss-Wright Defense Solutions. He has worked at Curtiss-Wright since 1996 in various design, engineering, and management positions including engineering manager of embedded systems, mechanical engineering manager, and manager of product line engineering. Sealander can be reached at jsealander@curtisswright.com.
Curtiss-Wright Defense Systems https://www.curtisswrightds.com/