MOSA and JADC2 driving innovation in military vetronics applications
StorySeptember 06, 2022
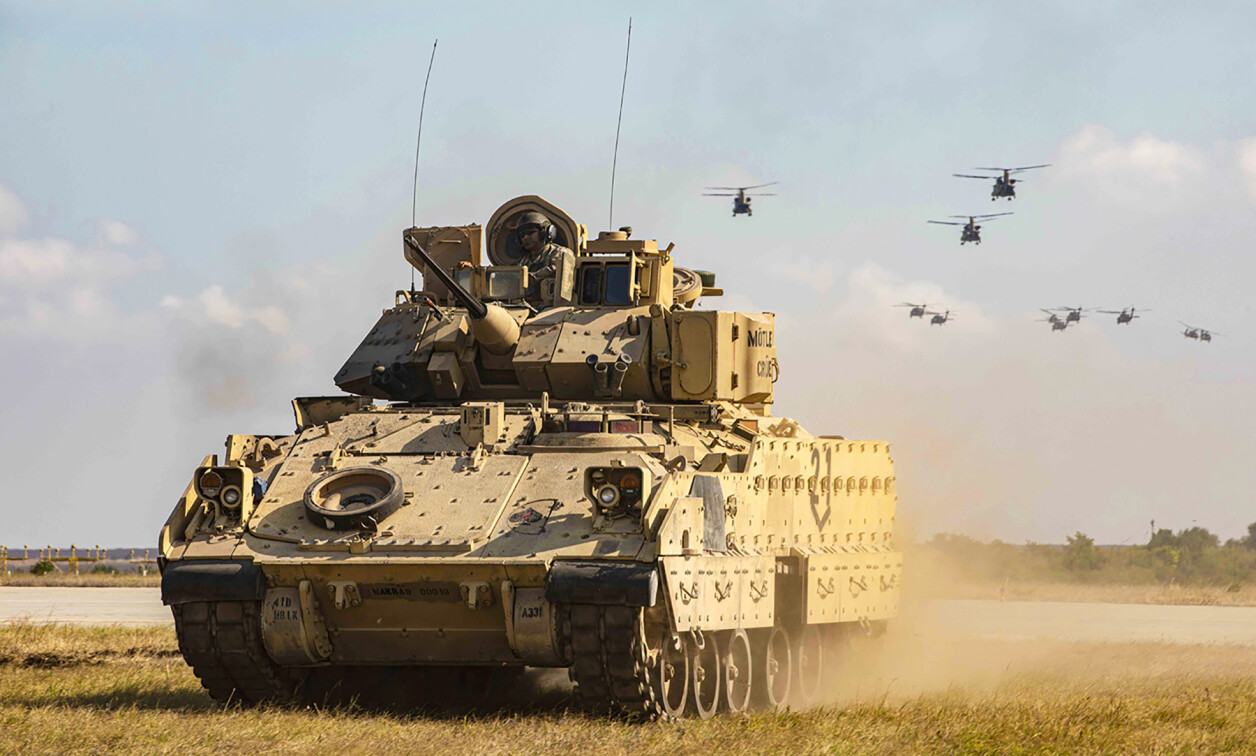
Vetronics systems today are increasingly focused on C4ISR [command, control, communications, computers, intelligence, surveillance, and reconnaissance], interoperability with other battlefield elements, and the capability to be optionally unmanned if necessary. They are also more likely to be built on open architectures as the U.S. Department of Defense (DoD) continues the push toward a modular open systems approach (MOSA) in upgrades and new designs.
For military ground platforms, the term “vetronics” no longer applies solely to vehicle controls, but how the vehicle electronics (vetronics) enable enhanced command, control, communications, computers, intelligence, surveillance, and reconnaissance (C4ISR); position, navigation, and timing (PNT); electronic warfare (EW) capability; optional unmanned capability; and connection to a larger defense network. This connectivity feature is critical as the U.S. Department of Defense (DoD) continues to build its Joint All-Domain Command and Control (JADC2) strategy.
Well-known ground platforms like the Army’s M1A2 Abrams tank, the Bradley Fighting Vehicle, and the Stryker Combat Vehicle will be connected to other platforms on the battlefield to better operate as a joint force. “JADC2 will overhaul military communications and enable U.S. armed forces to better handle the massive amount of information they collect and distribute every single day,” states Mark Hutchins, Executive Director, Protected Communications Systems, Raytheon Intelligence & Space, in his blog on https://militaryembedded.com/radar-ew/signal-processing/key-to-jadc2-converging-strategic-and-tactical-communications. “The strategic-to-tactical convergence of protected communications is key to bolstering JADC2 and should be deemed an urgent initiative to upgrade disparate legacy networks, gain resilience at the edge, and achieve data assurance. The forward-deployed can take advantage of resilient and jam-proof communications from the strategic community, while the strategic community uses the prolific tactical networks, both currently used and in development.”
Much of the technological investment for the Army is focusing on C4ISR, tactical communications-on-the-move comms, and JADC2. The latter is a huge driver across all platforms – land, sea, air, spectrum, and space, says Brad Curran, an industry analyst at Frost & Sullivan. Aspects of it will come from lots of different programs like exquisite satcom systems [the term used for large, highly sophisticated satellite systems often used for intelligence missions] to new air and ground platforms and especially missile defense, when it comes to tracking and countering hypersonic missiles, he adds.
“As the war in Ukraine has demonstrated, just like wars did in Iraq and Kuwait, holding or reclaiming disputed land territory requires Army-like vehicles and personnel,” says Chris Ciufo, CTO with General Micro Systems (GMS – Rancho Cucamonga, California). “Even though you can (and should) bomb your adversary into submission, you need rugged vehicles, materiel, and soldiers and Marines on the ground. The market for vetronics, technologically and geopolitically, looks stronger than it’s ever been for GMS.”
C4ISR funding within the Army is strong and directly impacts ground vehicles: For the Army, Frost analysts put it at $9 billion for 2021 with funding trending at a similar pace in 2022, with $6 billion spent so far and with still more than a quarter left in the calendar year, Curran notes.
Ciufo adds, “We see more RFQs/RFIs and more orders for programs than we can reasonably keep up with. If anything, we are seeing an increase in vetronics demand as systems and sensors are more mobile, and as more advanced requirements – like AI [artificial intelligence] or on-the-battlefield processing – become the norm. We keep adding more capability into our products.”
Vehicles will become a node on the interconnected battlefield or, as some call it, an Internet battlefield of things (IBoT), Curran says.
“With the U.S. government’s massive increases in social spending plus a continued recognition to fully fund the DoD, I expect that ‘best case’ next-gen programs like the Army’s NGCV [Next-Generation Combat Vehicle] may be less about entirely new platforms than about adding much-needed capability to still-capable existing platforms,” Ciufo says. “The M2A3 Abrams is an awesome vehicle that’s perfectly equipped for modern land warfare, God forbid. Yet it could benefit from the ADAS [advanced driver assistance systems] capability you can buy on a new Toyota or GM pickup truck. Better inter-connectedness between airborne, dismounted, and mounted assets would improve the overall battlefield picture and allow tank commanders, for example, to even better position their crew for the current and soon-future [opposing force]. Technology brings all of this into reality, right now.”
Enabling all this innovation will be open architecture designs that can quickly integrate commercial hardware and software solutions.
MOSA’s influence on vetronics
The three services – Air Force, Army, and Navy – mandated a modular open systems approach (MOSA) for all new technology platforms and upgrades, calling it a “Warfighting Imperative” in a 2019 joint memo. Examples of MOSA strategies that affect defense vetronics systems are VICTORY [Vehicular Integration for C4ISR/EW Interoperability], the Sensor Open Systems Architecture (SOSA) Technical Standard, and CMOSS [C5ISR/EW Modular Open Suite of Standards]. MOSA aims to embrace more commonality and open standards in an open architecture design to enable faster deployment of technology to the battlefield while maintaining lower life cycle costs.
MOSA is mentioned in almost all programs, which means that providers of standards-based electronics in the consortia will be relied upon, Curran says. The DoD “doesn’t want to be tied to proprietary gear” in the long run, he notes. The result: The primes and government will work more and more with commercial vendors, especially on the software side, Curran adds.
“MOSA is very, very real and from what I can see the Army is taking it very seriously” because the PEO GCS {Program Executive Office Ground Combat Systems) went through the trouble to create specific requirement documents to take what CMOSS laid down, what comes out of SOSA and narrows it specifically for their needs, says Jacob Sealander, Chief Architect for C5ISR systems for Curtiss-Wright Defense Solutions (Ashburn, Virginia). “SOSA is broad and has lots of options, so this was necessary. For the Army it’s 100 percent [MOSA and] open standards, and the preference by and large for those driven by VITA and SOSA, so you see those requirements hard and fast." (Figure 1.)
[Figure 1 | Curtiss-Wright’s CMOSS/SOSA Starter Kit is ideal for kick-starting the development of Ground Vehicle applications. It is pre-integrated with an SBC, a VICTORY Ethernet switch, and a timing module.]
MOSA is also more than just SOSA and CMOSS, as its a strategy and not a specific standard or specific technology.
“As a member of the Open Group and SOSA, we [at GMS] do believe in this technology, or we wouldn’t be investing in it,” he continues. “But we don’t believe that SOSA aligned OpenVPX boards and chassis are the only way to meet the MOSA mandate. Other standards might also meet the spirit of MOSA. The fact is: Mandating SOSA as the only MOSA approach once again locks the DoD into one particular technology to the exclusion of other technologies that might fit just as well or better.
“Also, commercial civilian technology evolves rapidly. Wouldn’t it be best to keep an open mind about how to use that technology instead of dictating that it can only be used on OpenVPX with SOSA profiles? That feels too constraining and not in the spirit of MOSA,” Ciufo adds.
Ciufo goes on to point out that “MOSA does not specify a technology – it requires the use of open standards as well as the ability to provide P3I [preplanned product improvement] and some form of vendor neutrality. GMS believes an excellent solution to MOSA requirements is found with Intel/Apple’s Thunderbolt technology. Widely used in commercial electronics such as laptops, external hard disks, docking stations and GPU expansion chassis, 40 Gbits/sec Thunderbolt technology added to any system makes that system interoperable with other systems by definition. Like all USB variants (including the latest USB4), you just plug in Thunderbolt technology and it works. (Figure 2.)
[Figure 2 | Product shown is GMS X9 Spider Host, with four Thunderbolt 4 ports in GMS LightBolt connectors. These provide Type-C connectivity for fiber connections plus up to 100 W of power delivery to sensors and remote systems. Also shown are dual 100 Gb Ethernet fiber ports.]
“A small-form-factor system, a display, a sensor, a GPS POSNAV [position/navigation] system, or any equipment interconnected by Thunderbolt technology provides vendor independence for the Army as well as plug-and-play upgradeability,” he continues. “Unplug one vendor’s system and plug in another vendor’s Thunderbolt-connected system. The size, weight, or shape of the system doesn’t matter and shouldn’t be dictated by a standard: If it solves the problem and meets the requirements, it can be used. Thunderbolt technology provides at-the-panel vendor independence with interoperability.”
SWaP-C and MOSA
“For U.S. vetronics applications, [which] are almost exclusively U.S. Army vehicles – current-gen with upgrades or future Army platforms, MOSA is a near-universal requirement since it’s driven top-down from the DoD; however, exceptions to this are frequently given because SWaP-C [size, weight, power, and cost] is still so important,” Ciufo says. “That is: Mandating a 1/2 ATR (short chassis) filled with expensive OpenVPX cards is rarely as efficient as adding a highly optimized 4x4 small-form-factor (SFF) system that tucks neatly under a seat or behind a cabinet.”
There are ways that SOSA and open standards can improve SWaP, Sealander says. “SOSA really lays the groundwork to take a step back from architecting a separate box for every function” from the radio to the fire control to the active protection system.
“With SOSA you take computing capability and move data around the platform, enabling you to architect differently, placing the computer where it fits and move data around seamlessly and with low enough latency that you don’t need purpose-built boxes,” he explains. “You can put whatever function you want anywhere in the vehicle. When this approach is embraced you have efficient reduced SWaP from classic systems, getting more capability in the same or less volume.”
Embedded computing demands
The capabilities in demand – whether high-performance sensors or AI solutions or improved C4ISR – all put pressure on designers of embedded computers from the signal-processing functions to the ruggedization to the reduced size, weight, and power (SWaP) requirements.
“Increasingly, we’re seeing demands for server-like performance in what once might’ve been a ‘simple’ mission processor,” Ciufo says. “While the mission processor still handles main housekeeping functions for the typical system – plus normal I/O like MIL-STD-1553, CANbus (in vetronics), serial ports, a couple of 1 Gbits/sec Ethernet ports and maybe one or two displays – there are new performance expectations. Sensors are higher resolution and/or provide more data, faster. There’s more emphasis on offloading the operator through the use of advanced analytics in the mission processor, as well as processing and interpreting in real time sensor data, like images. These performance functions might’ve previously been done in a separate signal-processing box or VME card – now they get embedded in the mission processor under the term [AI] or ‘edge processing.’
“For GMS, we are responding to the increased sensor and data load, plus the expectation for local and better processing in the mission processor, by adding fatter pipes, embedded GPGPUs, and offering microserver processors,” he continues. “We have multiple Thunderbolt 4 pipes on our X9 Spider small-form-factor systems and X9 Venom OpenVPX boards; we’ve added many more 10 Gbits/sec Ethernet ports plus two to four 100 Gbits/sec Ethernet ports to talk to sensors, other CPUs, or to provide inter-box communication. Eight core processors are common, with optional 20-core Intel Xeon D-2700 (Ice Lake) micro-server CPUs.”
Network demands are also driving requirements, Sealander says. “[Ground vehicle] requirements are focusing on the vehicle backbone with time sensitive networking (TSN), for example. There is going to be a big push for TSN to get rid of MIL-STD-1553 and take advantage of all the TSN benefits that come from an all-Ethernet vehicle backbone such as resource sharing, network resiliency, etc.
“Another requirement that is significant but not new to the ground combat market, is for natural convection cooling,” he adds. “Due to reliability issues active cooling is not wanted. Enabling convection cooling still remains a huge challenge given the power densities of the solutions they are asking for. We continue to come up with new thermal-management solutions to meet this old, but very restrictive requirement.”