Military IC aftermarket trends -- Q & A with Dale Lillard, president of Lansdale Semiconductor
StorySeptember 11, 2020
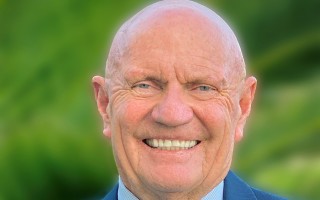
Decades-old military platforms like the Aegis weapon system and the Patriot missile defense systems, as well as key systems for fighter jets like the F-16, continue to go through modernizations and embrace open architecture designs, but critical integrated circuits (ICs) used in these systems have not changed since they were originally designed in the 1970s and 1980s. The U.S. military relies on aftermarket suppliers such as Lansdale Semiconductor to design these components exactly as they were first built by various semiconductor companies decades ago.
In this Q&A with Dale Lillard, president of Lansdale Semiconductor (Phoenix, Arizona), he shares how the military IC aftermarket performs compared to the rest of the defense electronics market, how this market segment is impacted by the global pandemic, and the vagaries of counterfeit-part mitigation. He also provides updated insights into several controversies he called attention to in the government IC-procurement process over the years. Edited excerpts follow.
MIL-EMBEDDED: Dale, please provide a brief description of your responsibility with Lansdale and how the company participates in the military-electronics aftermarket industry.
LILLARD: I am the president and owner of Lansdale Semiconductor, having purchased the company in 1987. I came up with idea of a military-semiconductor aftermarket in 1980, 40 years ago. My passion and hobby is restoring classic automobiles, where I’ve nearly always had the benefit of aftermarket support for most of the cars that I buy. It’s essential to restoring these classic cars and I thought that if I were a weapons-system supplier, I would want that same type of aftermarket support.
Lansdale now manufactures more than 2,500 classic design ICs in the original package, exactly as they were created and produced by AMD, Fairchild, Freescale Semiconductor, Harris, Intel, Motorola, National, Philips (formerly Signetics), and Raytheon. We were able to buy the tooling and manufacture the militarized ICs used during the military buildup of the Reagan administration in the 1980s. Approximately 80% of the weapons systems in service from that time are still using some military ICs manufactured during the 1970s and ‘80s. All those lines are still active – the last one I purchased was in 1993. I also have a commercial product line I purchased in 2002 that produces building-block ICs for the RF industry and for some aerospace applications.
They don’t make militarized ICs anymore, so the end user is forced to go with COTS [commercial off-the-shelf] technology. However, it’s more difficult for aftermarket support of commercial parts for military systems today. In the 1980s and 1990s militarized products were consolidated and the DLA [Defense Logistics Agency] maintained the specifications in a QML ([qualified military line] ensuring consistent support from the various manufacturers. The military components were designed into systems and aftermarket suppliers knew they would need to be supported. It is difficult to determine which commercial products would be profitable to support. My recommendation to customers is that if you have a system using commercial ICs that needs to maintain a long life, you should make EOL [end-of-life] buys, as you will never get the parts cheaper and also because you will not get the support that we have provided for military ICs of the ‘80s or ‘90s.
MIL-EMBEDDED: Has the current downturn due to the pandemic impacted your market? I’ve been told that it’s making many companies rethink using overseas foundries and suppliers and to buy more from American suppliers. Do you see that as well?
LILLARD: It impacted me. My manufacturer for the commercial market, based in Indonesia, was forced to shut down immediately one day. When I looked at where to go next, there were not a lot of options and I wanted to avoid China. So I brought the test part of that business into the U.S. For the assembly I moved it to Thailand.
Our commercial-product-line business – which supplies commercial communication applications such as televisions – has also slowed down because of the virus. Hotels are not ordering TVs right now.
Regarding future onshore semiconductor manufacturing, Arizona may be a location for U.S. suppliers to turn to, as Taiwan Semiconductor is looking to build its newest fab here in the state. That’s an indication that people are waking up to the semiconductor supply-chain challenges. Currently, the DLA auditors are not allowed into Taiwan Semiconductor in Taiwan, but perhaps that will change when it’s located in the U.S. Because the reality is it’s better to be here in the U.S. when it comes to IC production.
MIL-EMBEDDED: Department of Defense (DoD) funding is strong and flowing down through the supply chain. Does that benefit aftermarket suppliers as well? What would be a bad climate for aftermarket suppliers – a shrinking defense budget?
LILLARD: It’s kind of interesting. The aftermarket business cycle is typically the opposite from the rest of the defense-electronics market. When the government doesn’t have money to buy new toys, they make sure they maintain the old ones. As the DoD funding is at a high right now, my best business is in new production. The major contractors are selling major systems – that still use the parts Lansdale produces – and we are supporting those systems. The DLA itself, which usually buys spare parts from us, has been extremely slow in its procurement activity compared to last year. As money has moved to new systems, there has been a shift.
There has also been an uptick in Foreign Military Sales of weapon system platforms made in the 1980s and 1990s, such as the F-16 and [Patriot Missile Long-Range Air Defense System]. Some components in these systems are still supplied by Lansdale, which has of course been good for business.
MIL-EMBEDDED: Over the decades Lansdale has always been bold in standing up when it sees bad practices by the government. Most recent was in 2013 when the DoD was looking to mark components with plant DNA to help mitigate the spread of counterfeit parts. This practice was quite controversial, as it technically did not ensure that a part was not counterfeit and was instead a way for unauthorized distributors to become suppliers to the DoD. Eventually the practice stopped, correct? Where do things stand now?
LILLARD: I have not watched it closely since the DLA stopped making us mark the products we sell to them with DNA, but it is my understanding that the DLA continues to put DNA on each IC component they purchase. I’m not sure exactly why they still use the plant DNA, but when I talk with inspectors, I hear they are doing it for logistics and to maintain date codes and traceability on when products come in. They appear to have stopped claiming it prevents counterfeits, because it doesn’t. Counterfeit parts have been found with plant DNA markings on them.
Marking the products with DNA was an expensive process for suppliers to take on. Lansdale never did it as we sold through our distributor, who then added the DNA markings. Distributors are no longer required to do that, but we still use our distributor when selling to DLA.
[To read more on the DNA marking controversy, go to https://militaryembedded.com/comms/rf-and-microwave/dna-problem-solver-money-pit.]
MIL-EMBEDDED: What is the biggest challenge when mitigating counterfeit parts today? How do you overcome it?
LILLARD: There is no other solution except to buy from authorized suppliers. I look at the auto analogy again: When I’m working on my 1965 Ford Mustang and looking for replacement parts, I can buy something from China that has on paper all the right information, but when I go to put it in the car I find that the holes don’t match or it’s incompatible in some other way. Only the original manufacturer knows what they’re doing, whether it is automotive parts or military ICs. Lansdale has supported and contracted with the original manufacturer on our military ICs, so you know you are getting the same part. If you can’t guarantee that with a modern part, then I say it again, make big EOL buys.
MIL-EMBEDDED: Nearly 20 years ago, you raised some red flags about the fact that when manufacturing processes change, it can impact the reliability of a part, say, in an F-15 radar system. You were referring to the emulation methods used by the Generalized Emulation of Microcircuits (GEM) program at the U.S. Defense Supply Center Columbus (DSCC) in Columbus, Ohio. GEM was essentially trying to create new versions of components that you and other companies supply. Does this still occur, or have the processes become more reliable over the last two decades?
LILLARD: The processes are not, in fact, more reliable. The more advanced technology gets, the harder it is to duplicate our parts. Rochester Electronics, Lansdale, and others are doing a good job taking care of military-aftermarket IC needs. The GEM program doesn’t do a part if we make it, and the end user has to be cautious before they use it. I suspect they are still playing that game. You cannot just take a part and put into a radar system if you change the original technology. There is a risk involved.
Also, much like when restoring antique cars, you have a new generation of engineers, who – while talented and smart – are not the original designers that worked on these systems in the ‘70s, ‘80s, and ‘90s. They’re gone, and the new engineers may not understand the system completely, especially if the process has changed. It becomes more difficult with product insertions.
[To read more on the GEM process issue, go to http://www.lansdale.com/news_about_lansdale.php?a=detail&id=12.]
MIL-EMBEDDED: What are the typical defense applications Lansdale components end up in? Radar systems? Missile guidance? Communications?
LILLARD: The Aegis Combat System has used components from Lansdale over the decades and still does. No matter how much this system is modernized, it still needs the parts we make. The Patriot Missile Long-Range Air Defense System is another that is still active. Outside of that it is hard to say, especially with U.S. applications, as the DLA doesn’t tell us what systems the parts end up in. I must sell 150-200 different sole-sourced military parts each year of the 800 sole-sourced ICs I have.
MIL-EMBEDDED: What is the oldest product line Lansdale still supplies to defense customers?
LILLARD: The oldest is one of my favorites and it’s not a military system per se, but has similar characteristics. We sell robust HTL (High Threshold Logic 18-volt) products originally designed by Motorola in the 1960s for Westinghouse nuclear power controllers. We get business every year from them. Bulletproof parts that you can’t change, just as with our military ICs.
MIL-EMBEDDED: Looking forward, what disruptive technology or innovation will be a game-changer in the aftermarket world five to 10 years out? Predict the future.
LILLARD: I don’t believe the U.S. military will get rid of all these older systems; Congress will prioritize spending more on social programs than on replacing F-16s with F-35s, as the F-16 and platforms like it can be maintained for another 50 years. It is difficult to replace everything in an old platform with newer systems. Developing new platforms like the F-35 while maintaining and upgrading older, defensive systems like the Aegis is how the U.S. military maintains its role as the world’s most powerful military force.
R. Dale Lillard, president of Lansdale Semiconductor (Phoenix, Arizona), is an industry pioneer in the manufacturing of high-reliability aftermarket ICs and semiconductors. Lillard joined the company in 1980 as operations manager. He previously was product manager at Motorola Semiconductor Products Sector in Phoenix. Six months after joining Lansdale, Lillard was promoted to company president at just 29 years of age. He purchased Lansdale in 1987. Under his leadership, Lansdale continued its unprecedented growth by recognizing the critical need to support legacy ICs. With Lillard at the helm, Lansdale is today a leading supplier for the global electronics-components marketplace. He coined the term “semiconductor aftermarket.” Lillard graduated in 1972 from the University of New Mexico at Albuquerque with a bachelor of science degree in electrical engineering.
Lansdale Semiconductor http://www.lansdale.com