Military UAS procurement outlook strong, counter-terrorism and communication relays highlight future missions
StoryMarch 12, 2015
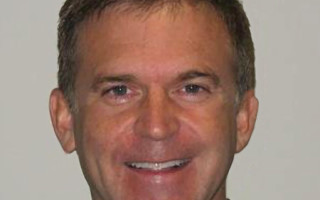
Unmanned aircraft systems (UAS) have been a game changer for the U.S military, providing persistent surveillance and lethality in the Gulf wars and the war on terrorism as such is their mission. In this Q&A with Chris Pehrson, Director of Strategic Development for General Atomics Aeronautical Systems, Inc. (GA-ASI), he discusses his outlook for unmanned aircraft procurement, the use of COTS in UAS payloads, UAS pilot training, and the potential for laser weapon capability in UAS platforms. Edited excerpts follow.
MCHALE REPORT: Please provide a brief description of your responsibility within GA-ASI and your group’s role within the company.
PEHRSON: I am Director of Strategic Development for all Department of Defense (DoD) business, which encompasses Army, Navy, Air Force, Marine Corps, and Special Operations customers. Products include GA-ASI’s full range of unmanned aircraft, ground control stations, and sensor payloads.
MCHALE REPORT: The DoD released it’s FY 2016 budget request last month with an increase in overall funding, almost a reverse trend from the last few years. How do you see the funding outlook for military unmanned aircraft within the DoD such as the Gray Eagle and Reaper variants? Has the DoD clearly defined what missions it will need these platforms for over the next five years?
PEHRSON: The Air Force budget for FY16 includes 29 MQ-9 Reaper UAS, a plus up of 7 over the previously planned procurement of 22 aircraft. The Army budget includes 19 MQ-1C Gray Eagle UAS, which matches planned procurement for FY16. There is a plus up in the Army budget, however, to procure those 19 aircraft as Improved Gray Eagle. This is a more capable variant than the original Gray Eagle with over twice the payload capacity and almost twice the endurance.
I think funding for military unmanned aircraft will continue to increase both for initial procurement and recapitalization of legacy aircraft. Unmanned aircraft are persistent, cost-effective platforms that will continue to be used for missions such as counter-terrorism and counter-insurgency, as well as new surveillance applications and communications relays. There is definitely increased interest in leveraging UAS to function as resilient nodes in airborne communication networks.
Unmanned aircraft are modular platforms that enable multiple mission configurations with varying capabilities, so their future is strong with the DoD.
MCHALE REPORT: Please provide an example of current unmanned military platforms GA-ASI supplies to the U.S. and international countries?
PEHRSON: For international markets, we redesigned the original MQ-1 and developed the Predator XP with modifications to make it export compliant. It is not weaponized and is ISR-capable-only in compliance with International Traffic in Arms Regulations (ITAR) and Missile Technology Control Regime (MTCR) guidelines. We designed it more efficiently than the original Predator, enabling us improve its endurance. Currently the Predator XP is rated at 35 hours, but in testing it has flown as long as 46 hours.
Domestically, the Predator C Avenger is our most advanced UAS platform. It can reach altitudes as high as 50,000 feet, can fly for as long 18 hours, and can carry over 4,000 pounds of munitions or sensor payloads. The Predator C is currently in an extended test program with the Air Force. We also used it to develop our offering – the Sea Avenger – for the Navy UCLASS competition.
MCHALE REPORT: There is an insatiable need for ISR data from sensor payloads, which often means heavy signal processing demands and use of commercial processing technology. In your payload designs, what is your approach to using commercial off-the-shelf (COTS) embedded computing technology and open architectures? How do you manage the obsolescence challenges?
PEHRSON: From a payload perspective, we often work with third-party providers via the government or as a system integrator. That said, we also leverage open architecture designs, COTS solutions such as avionics components, IP-based components, etc. If platforms and payloads are built to open standards, integration is much easier and faster. COTS solutions shorten the procurement cycle and make rapid integration of enhanced capabilities possible.
However, there are exceptions. Some applications, such as Gorgon Stare on the MQ-9, require unique cabling and components, which require more than just plug-and-play changes to avionics boxes or simple software updates.
There are multiple approaches to obsolescence management, some more aggressive than others. For example, we had an engine supplier with an obsolescence issue for the Gray Eagle, so we are now building those engines in-house. That is a pretty aggressive approach to diminished manufacturing sources (DMS). We also manage obsolescence through software upgrade cycles and open architecture designs. We work with the government program offices to ensure there is a plan for dealing with DMS challenges on all platforms and products. We have to pay attention to every avionics, mechanical, payload, and software component when it comes to managing DMS.
MCHALE REPORT: Reduced size, weight, and power (SWaP) requirements are hitting all applications in defense electronics. How are they impacting your unmanned payloads and the overall platforms? What are the tradeoffs with smaller tech?
PEHRSON: We build larger UAS with payload capacities as much as 2,000 pounds, so it’s not always optimal to try to be as small as possible. With smaller platforms, such as Scan Eagle or Shadow, it is necessary for electronics to be small. We have a little more wiggle room. That being said, miniaturizing components enables multi-INT solutions, such as multiple sensors to do signals intelligence, EO/IR, radar, etc. – and all on a single platform. The other advantage with smaller payload components is fuel savings, which increases endurance.
However, when miniaturizing components, one must obey the laws of physics. For example, a camera aperture and telescope lens needs to be of a certain size to take effective imagery.
MCHALE REPORT: How are you adapting your current and future ground control stations to comply with the DoD’s UAS Control Segment (UCS) architecture?
PEHRSON: There are two architectures we comply with in ground control stations (GCS) – the UCS and the UCI [Unmanned Aircraft Systems (UAS) Command and Control (C2) Standard Initiative]. UCS comes out of the Office of the Secretary of Defense and is a top-down concept. It is a more modular standard and our Block 50 GCS is built to comply with it. We are building to the hardware specifications and design. We also sit on UCS working groups to engage in dialogue and help with standards development.
In addition to UCS, the Air Force has UCI, which is more of a bottom-up approach, with messaging between different modules. UCI and UCS are both compatible in the same system with enough forethought early in the design.
MCHALE REPORT: What feedback do you get from military operators of your unmanned aircraft and how does that impact designs? Are they all certified pilots on manned aircraft as well?
PEHRSON: For our Block 50 GCS upgrade we worked with the Human Factors Laboratory at Wright-Patterson Air Force Base to design the cockpit and make pilot task loads easier. Efficiency and flight safety were paramount in the legacy GCS, but the user interface and similar human factor aspects needed enhancements.
For example, we improved how classified and unclassified information is integrated and displayed, improved menu scroll functionality, consolidated multiple intel feeds onto one screen, and provided hands-on-throttle-and-stick (HOTAS) flight controls. The result is a more elegant solution that enables the pilot to focus on the mission rather than the demands of just flying the aircraft. The improved human factor functionality is also more intuitive and reduces the training burden. Human factors are a primary consideration in modern aircraft design, particularly combat aircraft since it enables the pilot to focus on activities outside the aircraft, such as mission execution and avoiding threats.
In the Air Force, unmanned aircraft pilots have to be rated pilots. There is a separate UAS career field where they have to be instrument rated, but it is not full pilot training so they can enter a GCS career field earlier. The Army has UAS operators – warrant officers and senior enlisted – but they are not trained as rigorously as Air Force pilots.
The difference is more cultural, as the Air Force likes rated pilots flying the UAS and making decisions regarding mission execution. However, automation will continue to perform more and more pilot functions, and the pilot or UAS operator will become more of a mission manager or mission commander, possibly directing multiple aircraft in the battlespace.
MCHALE REPORT: GA-ASI recently announced the validation of its Due Regard Radar (DRR) for sense & avoid capability. Does this give your unmanned aircraft the ability to fly in civilian airspace without a manned aircraft escort? If not, then how far you away from developing that capability?
PEHRSON: We validated the engineering concept for our DRR, a system that can detect non-cooperative traffic and recommend maneuvers to avoid such traffic. It provides safe separation and collision avoidance inside a certain range or bubble of airspace around the airframe, enabling maneuvers to prevent a collision.
We’ve tested the MQ-9 with the DRR and we are working with the FAA to get it certified. We think the DRR will satisfy sense and avoid requirements in national airspace, but it will be a long process to get it certified as it takes time for policy to catch up with technology.
MCHALE REPORT: The DoD community loves its acronyms, but there seem to be competing acronyms when it comes to describing unmanned aircraft – UAV (unmanned aerial vehicle), UAS (unmanned aircraft system), and lately GA-ASI has been using RPA (remotely piloted aircraft). Why the switch to RPA? Was it more to assure the public that these vehicles have human control?
PEHRSON: First, let me say that RPA is an Air Force term, not a GA-ASI creation. UAV was the original terminology then UAS became the acronym of choice as it covered not just the aircraft, but the GCS and other components as well. The Air Force chose RPA to make a statement – that they are keeping the pilot in the loop. With RPA they can say to the public and those inside the Air Force that these aircraft are not autonomous flying robots and that a person is still in the loop and in control.
While the Air Force prefers RPA, the Army likes UAS. In the public domain, drone, which can have a negative connotation, has become popular. Drone is the widely adopted terminology, but I prefer UAS since it covers all components of the platform.
MCHALE REPORT: Looking forward, what disruptive technology/innovation will be a game changer for unmanned aircraft designs and/or payloads? Predict the future.
PEHRSON: I believe the next game changer – and this does not just apply to unmanned aircraft but to air combat in general – will be directed-energy laser weapon systems. GA-ASI is designing a laser weapon module to fit in the Predator C Avenger, and we plan to fly an Avenger with this laser weapon in 2018.
As Director of Strategic Development for GA-ASI, Chris Pehrson is responsible for satisfying customer requirements and promoting opportunities for the company’s full line of RPA systems, radars, and electro-optic and related mission systems in U.S. and international markets.