Ruggedizing interconnects for military and commercial UAVs
StoryMay 01, 2020
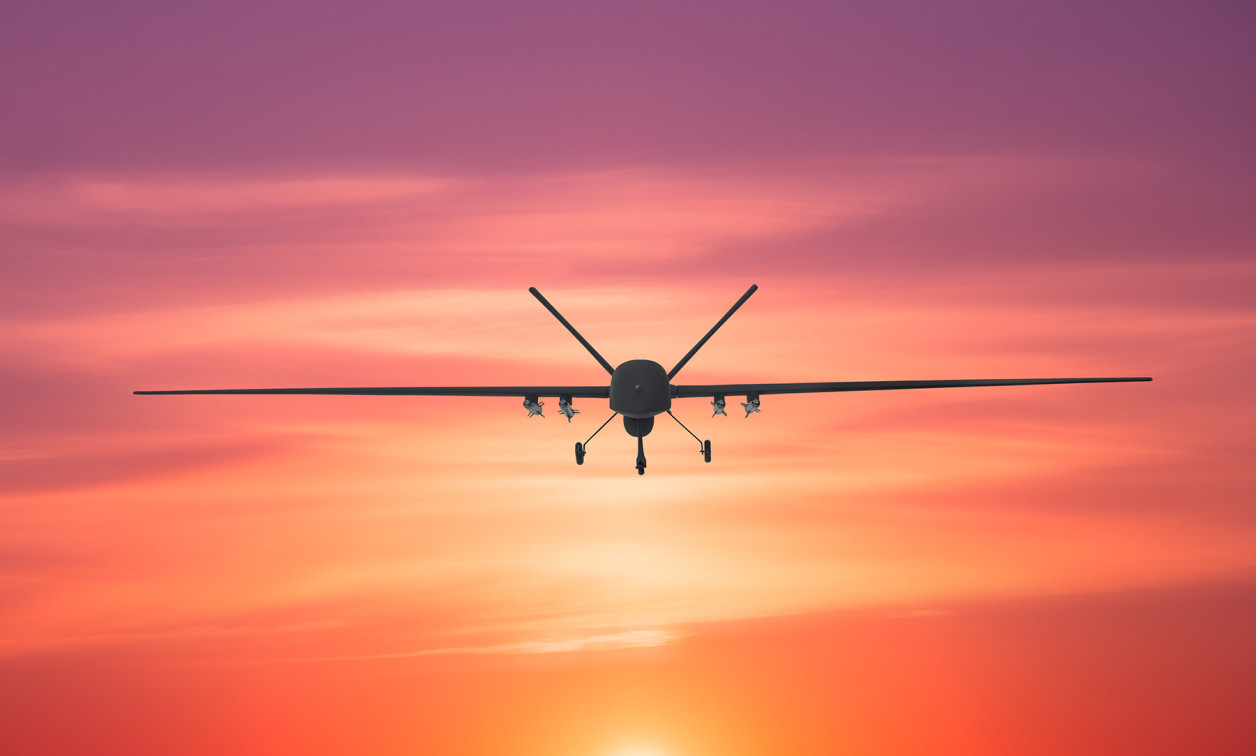
Advances in electrical and electronic components and related interconnect technologies have helped launch a vast drone industry for both military and commercial use. Small drones – classified as unmanned aerial vehicles (UAVs) – are incredibly popular and useful.
According to the U.S. Department of Transportation’s Federal Aviation Administration (FAA), UAVs are a fast-growing segment of the entire transportation sector – with nearly 1.5 million drones and 160,000 remote drone pilots currently registered in 2019¹. One report estimates that the drone industry will have grown to a $100 billion global market by 2020².
Unmanned aerial vehicles (UAVs) have evolved over the past number of years from hobbyist recreational uses to use in military operations and professional enterprise/commercial endeavors. Aerial remote sensing; border/perimeter patrol; delivery functions; urban and rural policing; and surveying and mapping for forestry, oil and gas, and agriculture are just some of the critical jobs drones now perform.
Military and commercial drones employ an array of electrical and electronic components in complex systems and subsystems in which reliability cannot be compromised. For example, in medical transport where medication, blood, or devices must be rapidly shipped to critical locations, the consequences of failure can be serious. In firefighting or military surveillance applications, failure can be catastrophic.
Consequently, the electrical and electronic interconnects used in recreational drones cannot be applied in commercial and military drones. Electrical wiring interconnection systems (EWIS), wiring harnesses, and connectors for batteries, controllers, motors, and flight systems must be tested and designed to withstand extreme environmental and performance demands. The emergence of these challenging environments is, in some cases, driving the development of new rugged interconnects targeted for UAVs.
Robust battery interconnects
Drone electric-propulsion motors, electronic speed controllers (ESC), flight controllers, global positioning system (GPS) modules, cameras, sensors, radios, and more all draw upon battery power. This reality makes the reliability of battery interconnects a critical factor in EWIS design.
Recreational drones generally use power connectors from varied sources – often commercial with no common standards. Reliability test data is limited, which creates uncertainty because interconnect performance is very sensitive to solder processing and wire management. In addition, component power ratings can be misleading and need to be quantified. Rating procedures need to account for such questions as: What temperature rise is factored into the power rating? What environmental conditions did the testing account for, such as altitude rating? A lot of critical data is missing from hobby-grade connectors.
On the other hand, military-grade legacy connectors rated for harsh environments are used for battery interconnect in military UAVs. But these interconnects are typically larger and not the best option when size and weight are critical. Designers face a dilemma between selecting interconnects that are either underbuilt or overbuilt for UAV applications.
Moreover, the introduction of smart battery technology requires additional signal pins to support a communication link between the charging system and battery pack. Smart batteries use specialized hardware and software to report information on voltage, current, and capacity, as well as temperature, impedance, and state of health. Additionally, a battery identification resistor is typically inserted inside the battery pack between an extra pin and ground to prevent a wrong battery being used in the charging system.
Finally, designers of UAVs for critical applications in the industry have indicated that a new interconnect is needed specifically for batteries operating under harsh environments where the interconnect is often exposed.
A solution for this application provides a rugged interface in a small form factor (SFF) to ensure reliable delivery of power or mixed power/signal to various UAV components. (Figure 1.)
Figure 1 | Ruggedized connectors for UAV power delivery can bring as much as 80 amps per power contact/4 amps per signal contact in a small form factor. Image: TE Connectivity.
|
The design of unmanned power (UMP) connectors is based on interconnect technology already used in harsh environments. Central to the UMP design is a type of high-conductivity 80A power contacts used in military power supplies and data centers. Crimped contacts provide repeatable reliability suitable for high-volume manufacturing on 8AWG to 14AWG wires and are field terminable. Packaging for UMP products employs 2-power, 3-power, and mixed power/signal configurations to address the pin requirements for UAVs. In addition, there are cable-to-cable and cable-to-board solutions in each pin configuration, with panel-mount options.
Reliability features include:
- For vibration resistance, the slim housing design incorporates contact locks and latching options to secure two connectors to ensure retention against vibration.
- For high temperatures, pigtails use high-grade, flexible silicone blend wire rated at 392 °F (200 °C) and 600 V.
- For reducing risk of solder-joint failure, removable crimp contacts are used to assure repeatable, reliable terminations and to facilitate easier field replacement.
Managing size and weight constraints
“Beefing up” electrical and electronic interconnects to make them robust for harsh environments can also add weight and volume. High-efficiency relays and contactors can be used to handle higher voltage and amperage within a compact footprint to help meet the demanding size, weight, and power (SWaP) requirements of UAVs.
Robust interconnect solutions that also handle UAV SWaP challenges come in all shapes and sizes. For “micro” circular connectors based on robust MIL-DTL-38999 Series 3 standards, microcircular connectors such as the DEUTSCH Wildcat Micro connector offer a significantly reduced shell size with two housing sizes and four layouts accommodating 3, 5, or 9 contacts.
- For small, micro-, and nano-miniature connectors: Compact rectangular, coax,and sealed circular connectors offer extreme weight and space savings. SFF rectangular connectors are fully sealed for IP67 rating and accommodate blind mating (see Figure 2). Smaller-scale connectors, like Nanonics connectors, are designed to fit micro miniature D, subminiature, and ultra-miniature coaxial needs.
- For compact fiber connectivity: ARINC 845-compliant EB termini (EB16) combine high performance and noncontact vibration resistance in mini sizes for single-mode and multimode fiber. Advanced transceiver modules – like new ParaByte fiber optic transceivers – feature a small thermal signature and support up to 12.5 Gb/sec transmission rates per channel.
- For less bulky cabling: Cross-linked insulation in Raychem cabling from TE is mechanically tough, thermally stable, and much lighter compared to thick-walled soft-polymer insulation in conventional cables.
- For space-efficient board-to-board and box-to-box connectivity: Light, next-generation high-speed backplane connectors that comply with the VITA 46 VPX standard are available with reliable quad-redundant contacts and support for 25+Gb/sec data speeds.
Figure 2 | Fully sealed 369 series rectangular connectors handle harsh environments with a space-efficient footprint. Image: TE Connectivity.
|
Secure, reliable UAV interconnect solutions
The need for reliable, rugged interconnects is critical in military and commercial drones. The number of takeoffs and landings in UAV applications is extreme, which can significantly stress the electrical interconnect system. Moreover, high-frequency power switching may be needed to enable rapid bus transfer in the event of power loss. It’s important to understand these new extreme environments and the required reliability levels to design in the appropriate products. For UAV designers, a “follow-the-wire” methodology uncovers critical factors in selecting the appropriate high-power and voltage solutions.
Today’s UAV projects benefit from the cross-discipline development of interconnect and power-management solutions from automotive, aerospace, energy, and rail sectors. Insights from industry standards groups – such as the Society of Automotive Engineers – address challenges imposed by higher power and voltage levels. Standards bodies are discussing next-generation SFF interconnects for safety-certifiable embedded computing modules and systems packaging suitable for UAVs. Using rugged interconnects for UAV electrical and electronic components will enable these vehicles to carry out tomorrow’s critical missions.
As the market continues to expand for small UAVs, the need for ruggedized SFF interconnect will grow. The ongoing development of cost-effective, efficient, SWaP-optimized interconnects designed for harsh environments will remove the temptation to employ commercial interconnects used in recreational drones flying over our backyards in mission-critical tasks. MES
References
¹ https://www.faa.gov/news/press_releases/news_story.cfm?newsId=24534
² https://www.goldmansachs.com/insights/technology-driving-innovation/drones/
Michael Walmsley, global product manager for TE Connectivity, has more than 35 years of experience with interconnects, primarily in engineering and product management roles. His areas of expertise include interconnect solutions for embedding computing, rugged high-speed board-level, and RF connectors. Michael is also associated with the VITA organization (www.vita.org), which drives technology and standards for the bus and board industry. He holds a bachelor’s degree in mechanical engineering from the University of Rochester and an MBA from Penn State.
William Newton is product manager, aerospace, defense, and marine at TE Connectivity. He has focused his time at TE on collaborating with global counterparts to complete projects and launch multinational initiatives. He holds a BS from Elizabethtown College and an MBA from Lebanon Valley College.
TE Connectivity
www.te.com